Milk Bottling Plant Description
Whether it is animal milk, or plant-based milk, or milk drinks, pasteurized milk, room temperature UHT milk, yogurt and other milk products can be filled into bottles for consumers to drink. Bottled milk package is popular because of their convenience, lower investment cost compared to aseptic carton filling machines, and recyclable packaging containers and other advantages.
The milk bottling plant consists of milk pretreatment system, milk homogenizing and sterilizing system, milk bottling system, bottled milk labeling and packing system, CIP cleaning system, RO water system, public facility(boiler, chiller, cooling tower, air compressor), etc.
The capacity of the milk bottling plant is from 1000 bottles per hour to 30000 bottles per hour available(based on 500ml bottles), and the milk products can be filled into plastic bottles(PET, PE or PP bottles), glass bottles or aluminum bottles, and the bottle volumes also has a wide range to choose from small bottles like 250ml-1000ml or big bottles 1L-5L.
Milk bottling plant machines are made of SUS304 material, and for each shift production finished, the whole plant will be cleaned thoroughly by the CIP cleaning system to keep the milk processing line in hygienic condition.
According to different milk products, different milk bottling machines need to be chosen, so it is highly flexible and customizable according to customers’ requirements.
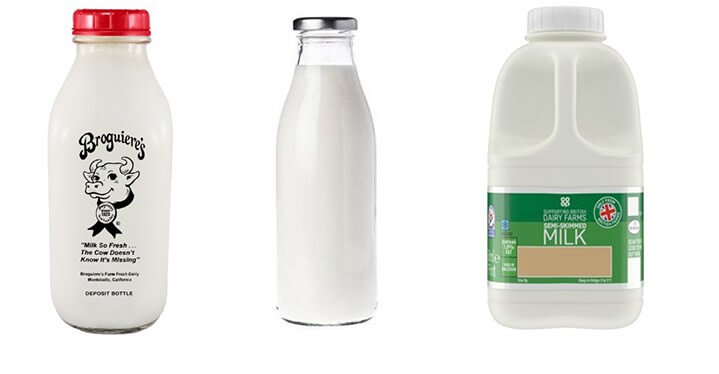
Milk Bottling Plant Production ProcessÂ
Milk pretreatment system
There are three styles of milk pretreatment systems in milk bottling plants:
—Animal milk: Fresh raw milk will be transported to the milk processing plant, then after reception and testing(temperature, protein and fat content, color, microgram testing), the fresh milk will be cooled down to 4degree and stored in milk cooling tanks. According to the end products produced, the milk will be further processed which may involve standardization, prepasteurization, separation and filtering.
—Plant-based milk: The plant-based milk pretreatment system mainly involves raw material cleaning and sorting, soaking, enzyme inactivation, raw material grinding and milling, plant-based milk separation and filtration process, plant-based milk standardization and blending.
—Reconstituted milk: use milk powder as raw material to reconstitute into liquid milk products. The pretreatment system mainly includes milk powder dissolving system, a flavoring dosing system and a milk blending system.
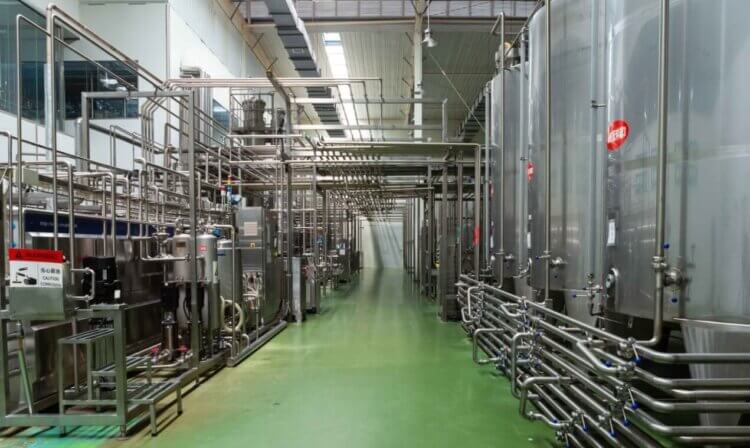
Milk sterilizing and bottling system
The milk sterilizing system has three processes: milk homogenization, milk degassing and milk pasteurization/sterilization. After the milk sterilization process is finished, the milk can be filled into the bottles. Because the milk sterilization and bottling process are the core machines in the milk bottling plant and also are highly related, we will explain the two machines combined in the following:
There are three types of the milk sterilizing and filling process:
—Pasteurized milk: The fresh milk will be pasteurized by the plate pasteurizer at 85℃ for 10-15S, then it will be cooled down to 4℃ and then filled into the bottles. When making this type of bottled milk, the machine investment is the lowest, only the plate pasteurizer+3-in-1 bottle filling system can meet the requirements. But this type of milk need to distribute in the cold chain(4-5℃), and the shelf life of the bottled milk is about one week. When bottling pasteurized milk, both PP bottles and glass bottles are popular packages.
—ESL milk: The fresh milk will be sterilized at 125℃ by tubular sterilizer, then cooled to 4℃ and filled into the bottles. The milk bottle filling machine will be ultra-clean filling, the filling room will be 100 levels clean, and the bottles and caps will be strictly sterilized by H2O2, then The milk can be filled into bottles and sealed by caps. The ultra cleaning bottle filling system will be 4-in-1 monobloc(one disinfectant solution rising bottle, one sterile water flushing bottle, filling and capping)or 5-in-1 monobloc(two disinfectant solution rising bottles, one sterile water flushing bottles, filling and capping)system, it may also equip the SIP and SOP system to make sure the whole filling process is clean. This type of milk shelf life can reach 14-28 days in cold chain distribution.
—Room temperature milk: There are two types of room temperature milk: one is aseptic bottled milk, and the other is hot filling bottled milk.
- Aseptic bottled milk: The UHT aseptic bottled milk usually uses fresh milk as raw material, after UHT is sterilized, the milk will be cooled down to room temperature and aseptically filled into the bottles. This type of milk needs to ensure the packing materials, milk, filling process and filling environment are all in an aseptic state. The bottles and caps will be sterilized with a disinfectant solution and then flushed with sterile water and dried by the sterile air to realize the aseptic state; The aseptic milk will be obtained by UHT sterilizing; The filling process will adopt non-contact electronic valve aseptic filling; The filling environment will be ensured by sterile air and sterile water system. The aseptic milk bottling plant needs a very large investment in machines to ensure the whole filling process is aseptic, so it is not very popular due to the big cost. However, the advantage is that the milk can have a stable shelf life in a room temperature environment, and the milk nutrients and flavor can be kept maximum.
- Secondary sterilized bottled milk: The secondary-sterilized bottled milk usually uses milk powder as raw material to make the reconstituted milk and flavor milk products. The milk will be pasteurized and filled(35-40℃)into the bottles, and then the bottled milk will be fed into a retort sterilizer to do the secondary sterilizing(121℃ for 20min). After such treatment, the milk will also have 6 months shelf life at ambient temperature. But when making this type of milk, the bottles must use PE or PP bottles which have high-temperature resistance features, and after the milk is filled into PP/PE bottles, one aluminum foil sealing machine is applied to seal the bottle mouth to increase the sealing tightness and extend the shelf life of the end products, then the bottles will be sent to the retort sterilizer for the secondary sterilizing, then capped and sent to next process.
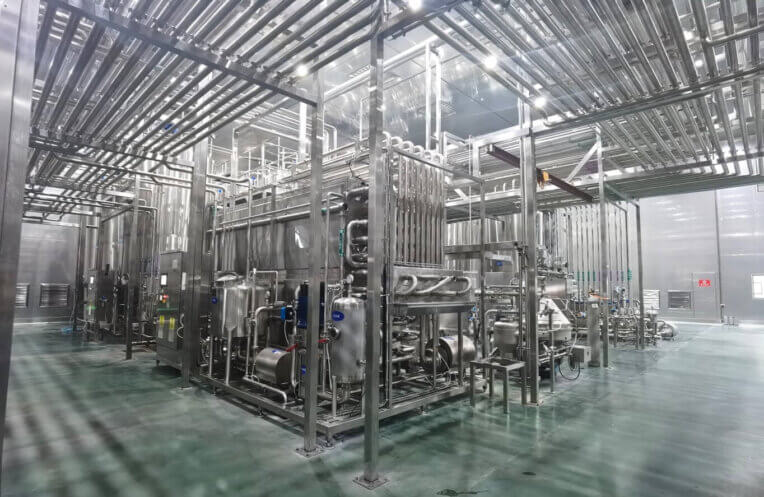
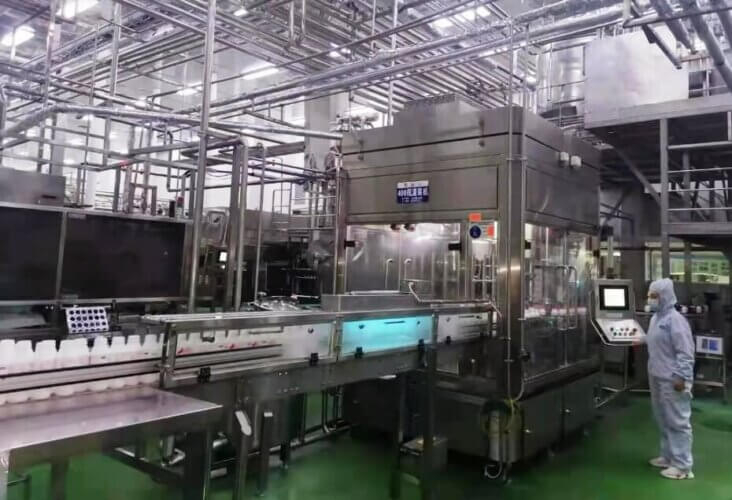
Bottle milk labeling, coding and packing system
Labels with product information, branding, and nutritional details will be stuck on the bottles. And the code printer will also print the expiry dates on the bottles. Additionally, each bottle might receive a unique code or batch number for traceability.
After the bottles are coded and labeled, they will be packed into the cartons, then the bottled milk is stored in temperature-controlled environments to maintain freshness. Once quality checks are complete, the milk is prepared for distribution to retailers and supermarkets for sale.
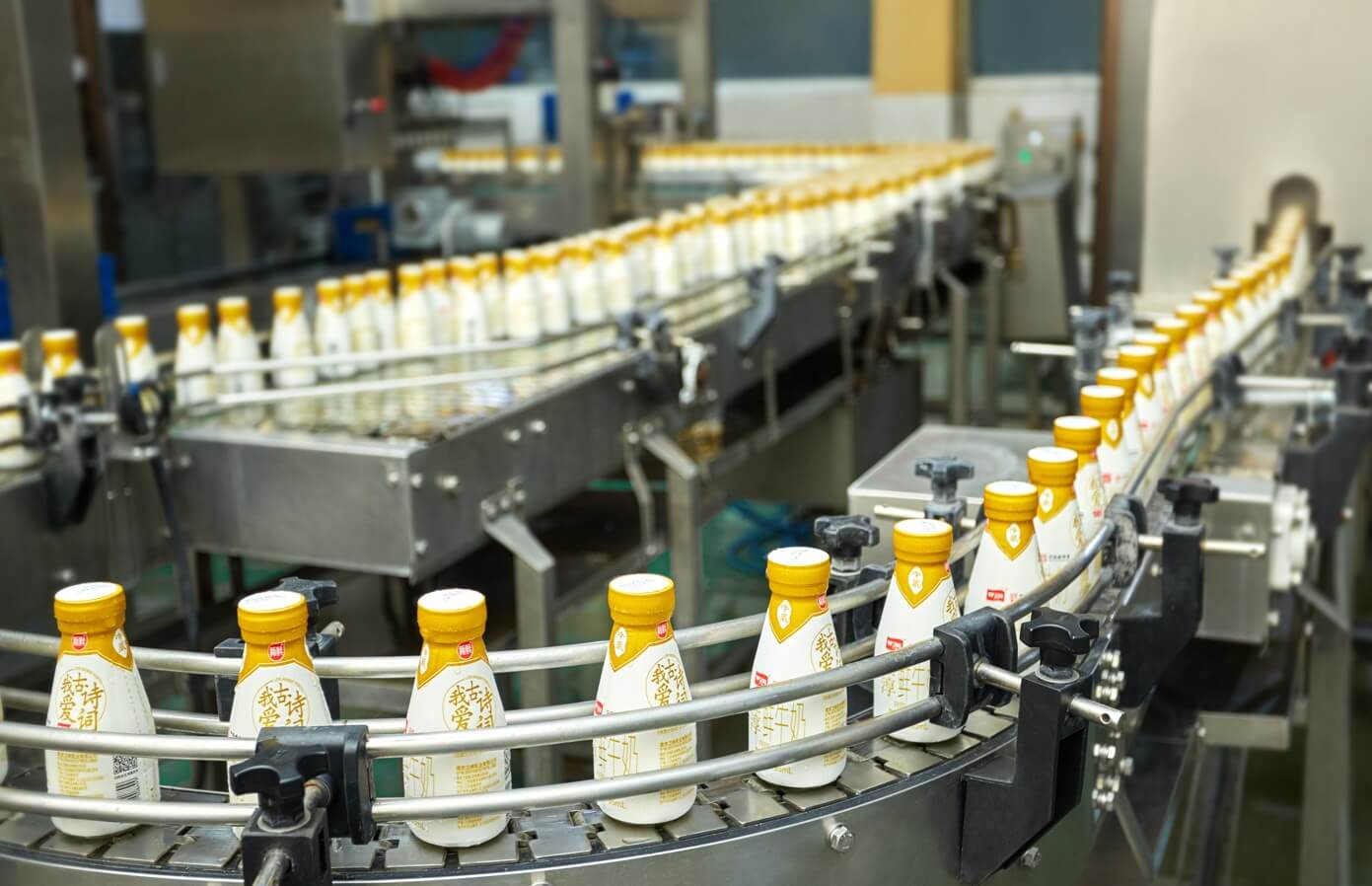