Project Description
Tomato Processing Line
Tomato Production Line Characteristics
1. The whole tomato paste processing line is including a lifting system, bubble water cleaning system, sorting system, crushing system, preheating enzyme inactivation system, pulping system, vacuum concentration system, sterilizing system and aseptic bag filling system.
2. Production capacity includes 40 tons,60 tons, 100tons, 150 tons, 300 tons, 400 tons, 500 tons, 600 tons, 800 tons, 1000 tons, 1200 tons and 1500 tons of fresh tomatoes per day.
3. The tomato paste concentration rate is 28%, 30%, 32%, 36 38%.
4. The tomato paste evaporator uses a secondary steam condensation recovery system, which greatly reduces steam consumption.
5. Using the special effect of the crusher and low-temperature concentration (first effective evaporation temperature is less than 70 ° C), the material stays in the evaporator for a short time, and the loss of nutrients such as red pigment (ketchup) is small.
6. The whole tomato processing line is fully automatic and all the control parts are using international famous brands such as SIEMENS PLC, SCHNEIDER electronic parts, DANFOSS converter and other world first-class brand parts to ensure the whole processing line with high performance.
7. Tomato paste production uses a low-temperature vacuum evaporator, which greatly reduces energy consumption; at the same time, the flavor and nutrients of tomatoes are preserved to the maximum in a low-temperature state. For the cooling water of the evaporator, the outer tank is recirculated to reduce the waste of cooling water.
8. The entire process design and pipeline connection layout take into account the retention of the original natural aromatic components of the ketchup product. The entire cooling and heating process and material transfer are completed in a short time and a short distance, which effectively prevents the heat-sensitive reflection of flavor substances from escaping; at the same time, it reduces the quality damage caused by the oxidation reaction of tomato puree under high temperature.
9. The tomato paste processing line’s main equipment is all SUS304/316 material, which ensures the end products are of high quality and hygiene.
10. The tomato production machine is flexible; tomato paste, tomato sauce, ketchup, tomato puree or tomato juice can be produced according to the free combination of the products produced according to the customer requirements.
11. All the tomato processing machines is linkage start and stop and are controlled by PLC, which greatly saves labor and enhances production efficiency.
12. The tomato end products can be filled into aseptic bags, flexible pouches, metal cans, small sachets, bottles or cartons.
13. The tomato paste production process typically involves several stages, including washing, sorting, hot or cold breaking, preheating, pulping, concentrating, sterilizing, and filling.
The End Product and Package of Tomato Processing Line
—Concentrated tomato paste: From 4-6 brix concentrated to 28-30brix hot break or 36-38brix cold break tomato paste, filled into aseptic bags (5kg-1000kg) and tin cans (100g-2500g) and sachets(5g-100g).
—Tomato puree: Fresh tomatoes after washed, sorted, crushed, blended, or milled to a thick liquid, but with no significant substance added or removed, the Brix value 4-6 Brix. The tomato puree can also be filled into pouches, tin cans, bottles, or tubes.
—Tomato sauce: Use concentrated tomato paste as raw material, mixed with water, sugar, salt, seasonings and other ingredients and make it into 12-24brix tomato sauce, then filled into small containers like PET/glass bottles, tin cans, sachets, brick cartons, pouches and other packages.
—Tomato Juice: the processing flowchart is similar to tomato ketchup or tomato sauce. But tomato juice has a lower viscosity and it is a beverage and can drink directly.
—Tomato Powder: Fresh tomatoes after pulping, then concentrate into tomato paste, then use the spray dryer to dry concentrated tomato paste into tomato powder. After drying, the tomato powder water content is about 4%-5%, then the tomato powder can be filled into pouches.
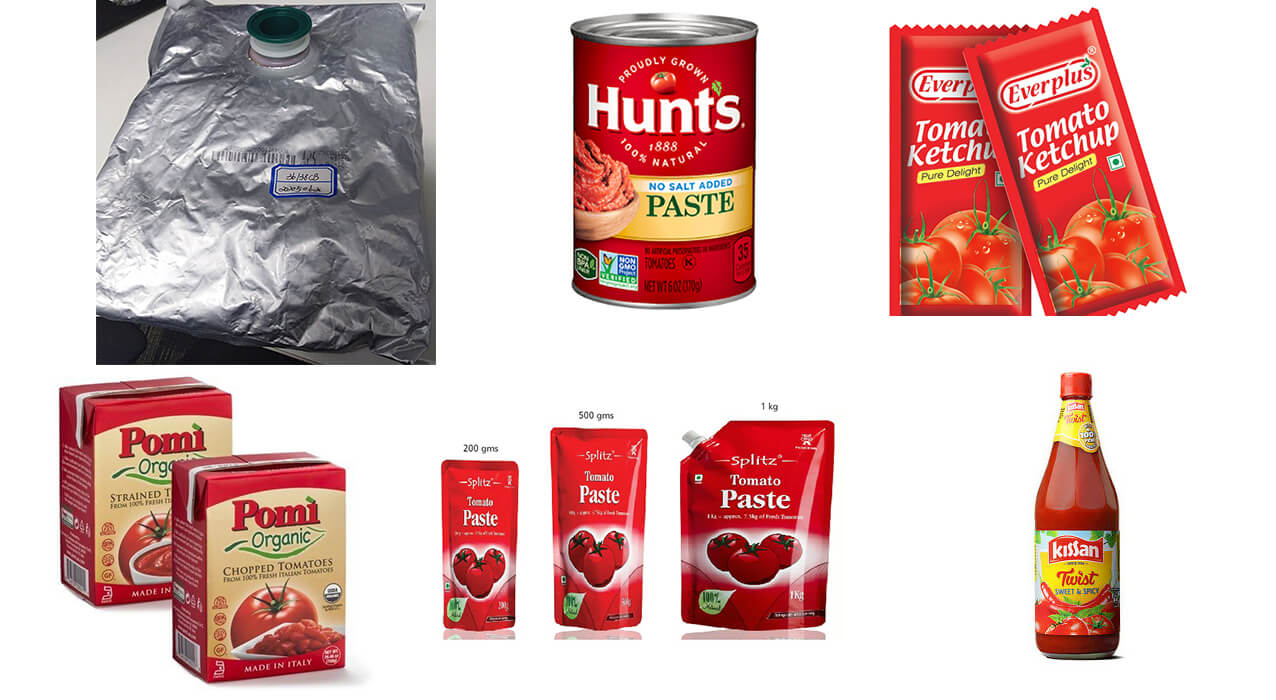
Technological Flowchart of the Tomato Paste Processing Line
Concentrated tomato paste: use fresh tomato as raw materials, fresh tomatoes after air blowing washing, roller sorting, hammer crushing, tubular preheating, double stage pulping and refining, force circulation concentrating and tube in tube sterilizing, then filled into aseptic bags or small container packages.
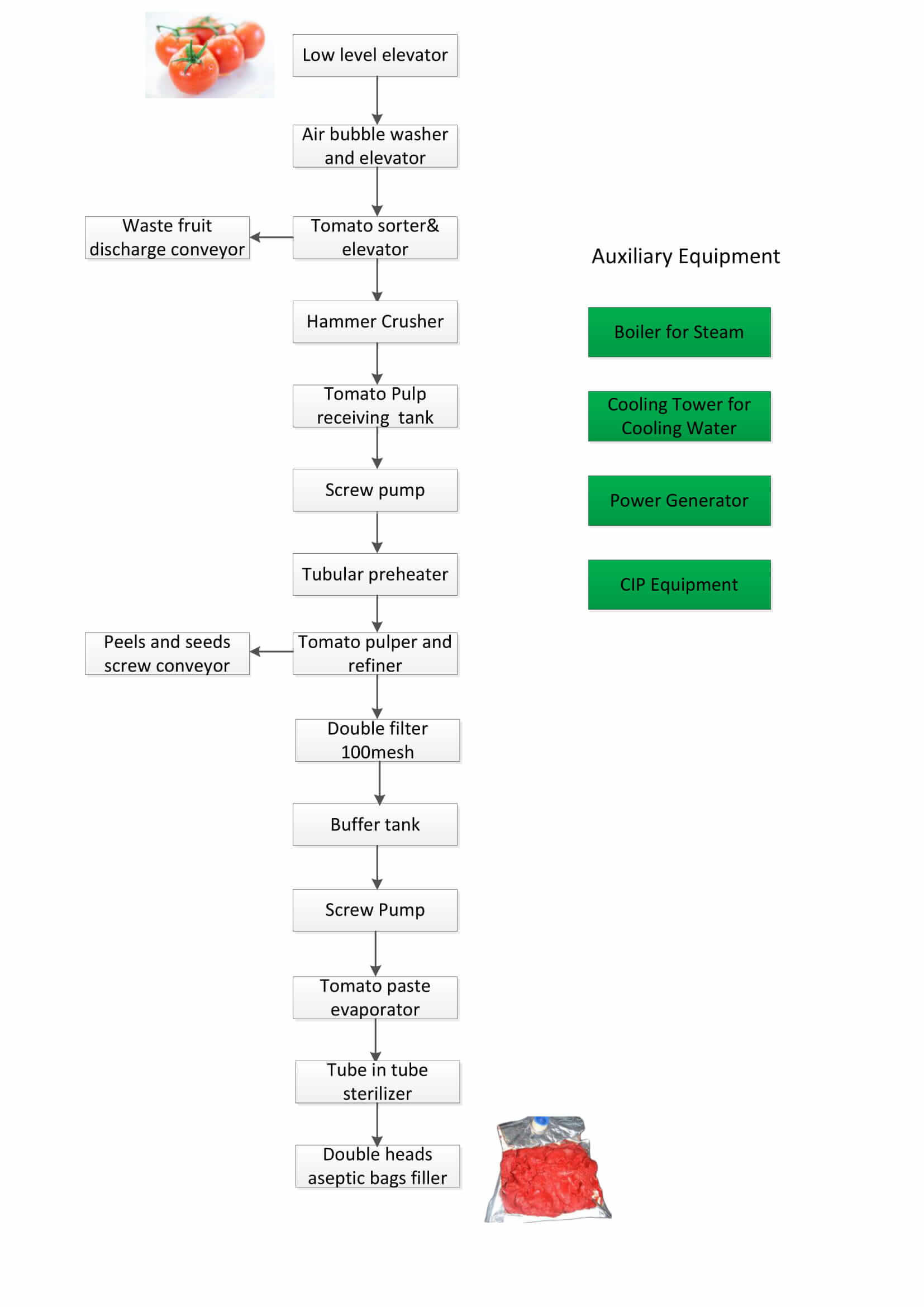
Key Machine of The Tomato Paste Production Line
Fresh tomato washing and sorting machine
Fresh tomatoes will be washed by air bubble washing machine, then we will get the clean tomatoes. After that, we need to sort out the bad and green and unripened tomatoes from the good quality tomatoes in order to get high-quality tomato paste.
As the tomatoes move through the water tank, air bubbles are injected into the water, creating turbulence that helps to dislodge dirt, debris, and other contaminants from the surface of the tomatoes. The combination of water, air bubbles, and mechanical agitation effectively cleans the tomatoes without damaging the skin or causing bruising. After the tomatoes have been cleaned, they are then rinsed with high-pressure fresh water during lifting to the sorting conveyor.
As the tomatoes move along the roller conveyor, they are inspected by workers who remove any damaged or low-quality fruit. The remaining tomatoes continue to move along the conveyor and are sorted by size using the spacing of the rollers.
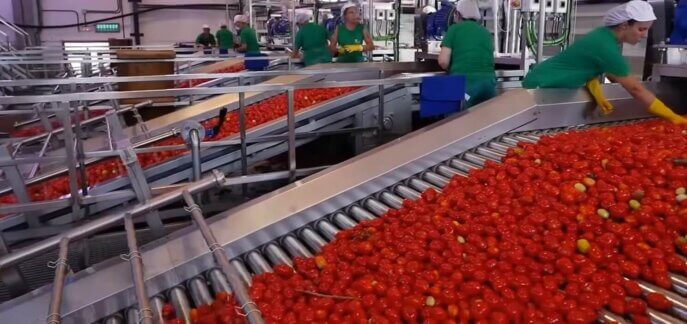
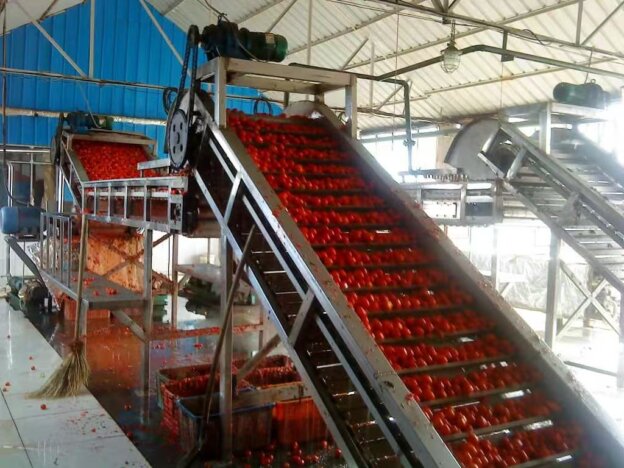
Tomato crusher and pulping machine
After we get clean high-quality fresh tomatoes, we will use the hammer crusher or crusher pump to crush the tomatoes into 3-5mm particles, then we transfer the crushed tomatoes to double stage pulping machine to get the tomato paste which size is 0.4-0.6mm, but in order to enhance the pulp yield rate, before pulping, we use the tubular type preheater to heat the tomato pulp to 60℃ for 15 minutes. The double-stage pulping machine for tomato pulp yield rate is about 90%, after pulping, tomato peel and seeds will be separated from tomato pulp. Tomato pulping machines are commonly used in commercial food processing operations to extract tomato pulp for use in sauces, ketchup, and other tomato-based products.
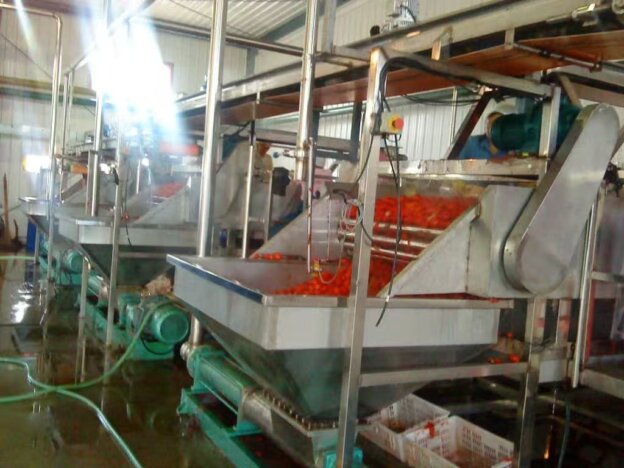
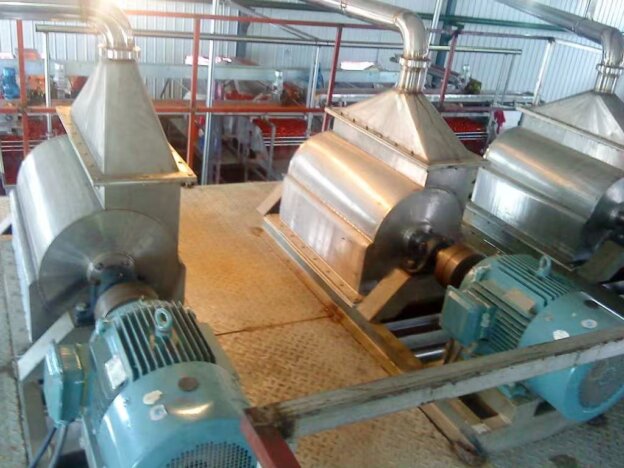
Tomato pulp preheating system
We use tubular type preheater to treat tomato pulp, there are two types of process, one is for hot break tomato paste, tomato pulp will be heated to 85-90℃ for 10-15 minutes; The other type is cold break tomato pulp, which will be heated to 55-60℃ for 10-15 minutes. Destroy pectinase activity, save more pectin; ensure product viscosity; soften tomato pulp, easy to separate and enhance the pulping rate.
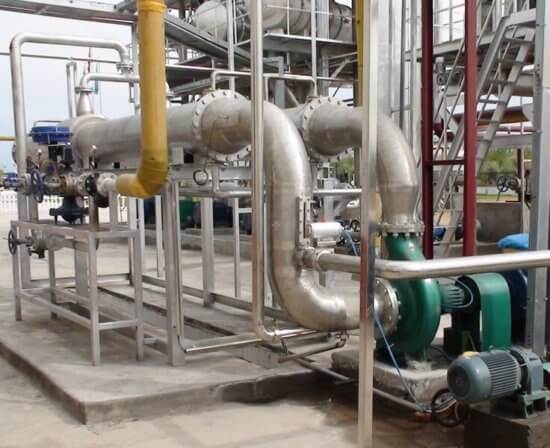
Tomato paste evaporator and sterilizer
The forced circulation evaporator can evaporate the raw tomato pulp (about 5 Brix) into tomato paste (28- 30 Brix or 36-38 Brix). The evaporator uses heat and vacuum pressure to remove the water from the tomato pulp, leaving behind a highly concentrated tomato paste. The tomato paste evaporator typically consists of a large cylindrical vessel with a heating jacket, a steam inlet, and a vacuum system. The tomato pulp is introduced into the evaporator and heated to a high temperature, causing the water to evaporate and leaving behind a thick, concentrated tomato paste.
Then we use a tube-in-tube sterilizer to do heat treatment of the tomato paste to remove the bacteria of the tomato paste to get the long shelf life, and the typical sterilizing process is 108-110℃ holding for 120S. The sterilizer typically consists of a large tube in tube heat exchanger and a temperature control system. The tomato paste is pumped to the heat exchanger by a high-pressure pump, where it is heated to the desired temperature and held at that temperature for a few seconds before being cooled and packaged.
The evaporator and sterilizer are all fully automatic with internationally famous brand control parts and made of SUS304/316 material to ensure high-quality tomato paste.
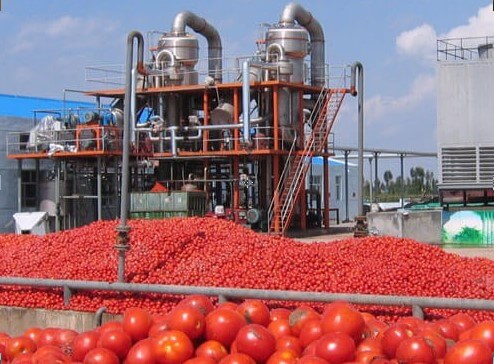
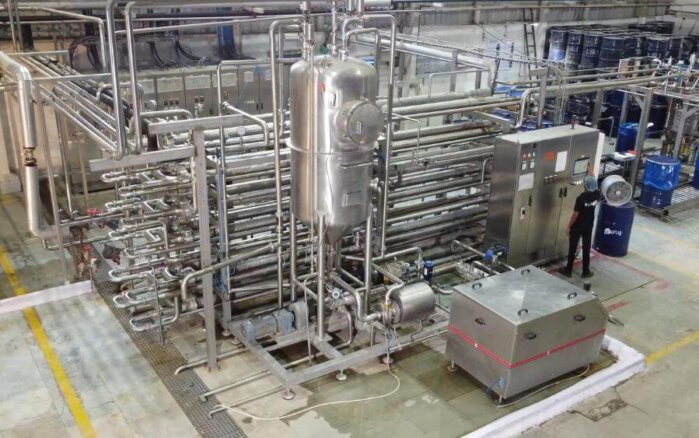
Tomato paste filler
After the tomato paste is sterilized by tube in tube sterilizer, then we use the aseptic filler to fill into 5kg-1000kg aseptic bags, the filling process is in an aseptic environment and the filling temperature is about 30℃. To ensure aseptic condition, the filling chamber will be sterilized by steam and all filling processes will be in a fully closed environment. The tomato paste in aseptic bags can reach 2-year shelf life.
Other than an aseptic bag filling machine, the concentrated tomato paste can also fill into metal cans used as cooking ingredients, this package is very popular in African and Middle-East markets. Tomato paste metal can filling machines are commonly used in large-scale food processing operations, such as canning or packaging facilities, to fill and package tomato paste for distribution to consumers. The machines are designed to be highly efficient and can fill a large number of cans quickly and accurately, helping to reduce labor costs and increase production capacity.
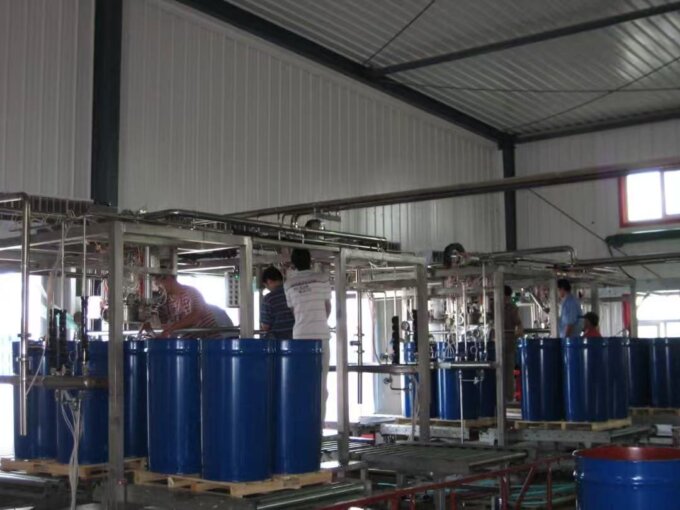
Video Performance
FAQ For Tomato Paste Processing Line
What information do you need to provide when you request a quotation?
Please provide the below-detailed information as much as possible:
- What is end products do you want to produce?
—Our machine can make concentrated tomato paste, tomato puree, tomato juice, tomato ketchup or tomato sauce.
- How many tons of fresh raw tomatoes can you supply per day?
—We supply machines from 20 tons per day to 1500 tons per day.
- What containers do you want to fill, aseptic bags in drums, tin cans, sachets or other containers?
—Bag in drums tomato paste is for wholesalers who use it as raw materials to make tomato ketchup or sauce, whereas tomato paste in tin cans or sachets is for consumption as cooking ingredients.
- What is the Brix value do you require for the end products, 28-30 Brix or 36-38 Brix?
—Cold-breaking tomato paste means that after the tomato is broken, the enzyme is inactivated at <70°C (generally 65°C), and then concentrated to 36-38 brix, and the viscosity of the cold break tomato paste will be low, but the flavor and color are good; The hot-breaking paste is the enzyme is inactivated after the tomato is broken at> 80°C (generally 85 or 90°C), and then concentrated to 28- 30 brix, the viscosity is higher, the flavor and color are poor. Usually, if your tomato capacity is below 250TPD, we do not suggest that you produce 36-38 Brix Tomato paste.
Can we produce 8 hours a day?
We do not suggest that, because if you produce 8 hours a day, then the production line needs to be stopped every day, when the production stop, you need to do the CIP cleaning, then it will cause a lot of waste of raw materials and lower down the whole production line efficiency(Especially the tomato paste in the evaporator).
What auxiliary equipment do we need for tomato paste processing?
–The CIP system is optional because the evaporator and sterilizer have self CIP cleaning function.
–Oil boiler or gas boiler to generate steam, the tubular preheater, sterilizer, evaporator and CIP system all need steam to heat the material.
–Cooling water tower to generate cooling water. The sterilizer, tomato paste evaporator all need cooling water to cool down material after heating.
–Air compressor to generate compressed air. The pneumatic valve group in the production line needs compressed air to perform its actions.
–RO soft water system. The soft water can be used for CIP cleaning water and evaporating water.