Project Description
Milk Powder Production Line
Milk Powder Production Line Description
1. Milk powder refers to a powdered product prepared by using fresh milk as a raw material, adding a certain amount of vegetable protein and fat, vitamins, minerals and other raw materials, through the process of sterilization, concentration, and drying to make the milk powder. On the basis of keeping the original quality and nutritional value of the milk, the milk powder has the characteristics of low water content, small size, lightweight, long storage period, convenient eating and easy carrying.
2. Milk powder processing plant includes raw milk acceptance system, raw milk standardization tank, raw milk preheating machine, homogenization, sterilization, milk skimming (to produce skimmed milk powder), raw milk vacuum concentration, sugar preparation (to produce sugared full fat milk powder), spray drying, and milk powder sieving, cooling, filling, inspection, packaging, CIP cleaning station, boiler, cooling tower, air compressor, chiller, connection pipes, valves, bents, pumps, etc.
3. The milk powder production line is controlled by fully automatic PLC with highly automated, safe and pollution-free. The equipment configuration is flexible, it can produce full-fat milk powder, full-fat sugared milk powder, skimmed milk powder, flavored milk powder, etc. according to the different needs of customers.
4. Concentration and drying are the most critical processes in milk powder processing. We use a vacuum concentration evaporator to concentrate and evaporate the water in the milk under low-temperature conditions, minimizing the loss of color, flavor and nutrition in the milk; For milk powder drying, we use the most advanced centrifugal or pressure spray drying equipment, which has the characteristics of fast drying speed, low-temperature drying, good product sanitary quality, and it is carried out under fully enclosed conditions and is not easy to be polluted.
5. The final product of milk powder can be packaged in tinplate cans, plastic aluminum foil composite bags, kraft paper bags, carton box, etc.
6. The entire milk powder production plant equipment is made of SUS304, equipped with a CIP cleaning system, the production process is carried out in a fully enclosed environment, and the final product is inspected by strict inspection equipment to ensure the high quality of the milk powder.
7. The capacity of milk powder production is from 1 ton per day to 100 tons per day available for clients to choose from.
8. The water content in the milk powder is between 2.5 and 5%. Under such a low water content, no bacteria can reproduce. Drying prolongs the shelf life of the milk, greatly reduces the weight and volume, and reduces the storage and transportation costs of the product. Skimmed milk powder has a maximum shelf life of about 3 years, and whole milk powder has a maximum shelf life of about 6 months. This is because the fat in the milk powder oxidizes during storage and gradually loses its flavor.
Milk Powder Production Line End Products
Full-fat milk powder: it is made from milk as raw material, with food additives, and nutritional fortifiers, after concentrated and dried into powder products. Whole milk powder can be filled into composite bags or tinplate cans. When producing full-fat milk powder, the standardization process is a key factor in making the final products with the same quality.
Skim milk powder: it is the most common milk powder. Milk powder is obtained by using milk as raw material, adding food additives, removing fat from the milk through a centrifugal separator, and then concentrating and drying the milk powder.
Full-fat sweetened milk powder: Milk powder is made from milk and white sugar as raw materials and can be added with food additives, after concentrated and dried to produce full-fat sweetened milk powder.
Infant formula milk powder: it uses fresh animal milk as raw materials, fortified with fats, minerals and vitamins as ingredients to make into the milk powder, it is mainly used for feeding babies under 12 months of age as baby food products. The production process of infant formula milk powder mainly involves fresh milk receiving and storage, non-thermosensitive ingredients(fats) wet mixing, milk pasteurization and evaporation, milk powder spray drying, heat-sensitive ingredients(vitamins, minerals) dry mixing, and infant formula milk powder packing.
Flavored milk powder: a powdered product obtained by using milk as the main raw material, adding auxiliary materials, and concentrating and drying.
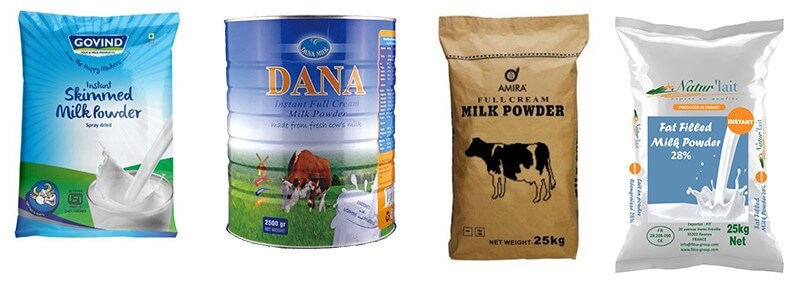
Milk Powder Production Line Technological Flowchart
Fresh milk after the reception, then the milk will be standardized, preheated and separated, then pasteurized, and homogenized, the milk will be pumped into vacuum falling film evaporator, after concentration, the milk will be sent to spray dryer to make milk powder, then cooling to 30℃, after sieving, then milk powder will be filled into containers like bags or metal cans, then through the metal detector, the milk powder in the container will be checked and then print on date and stored into the warehouse.
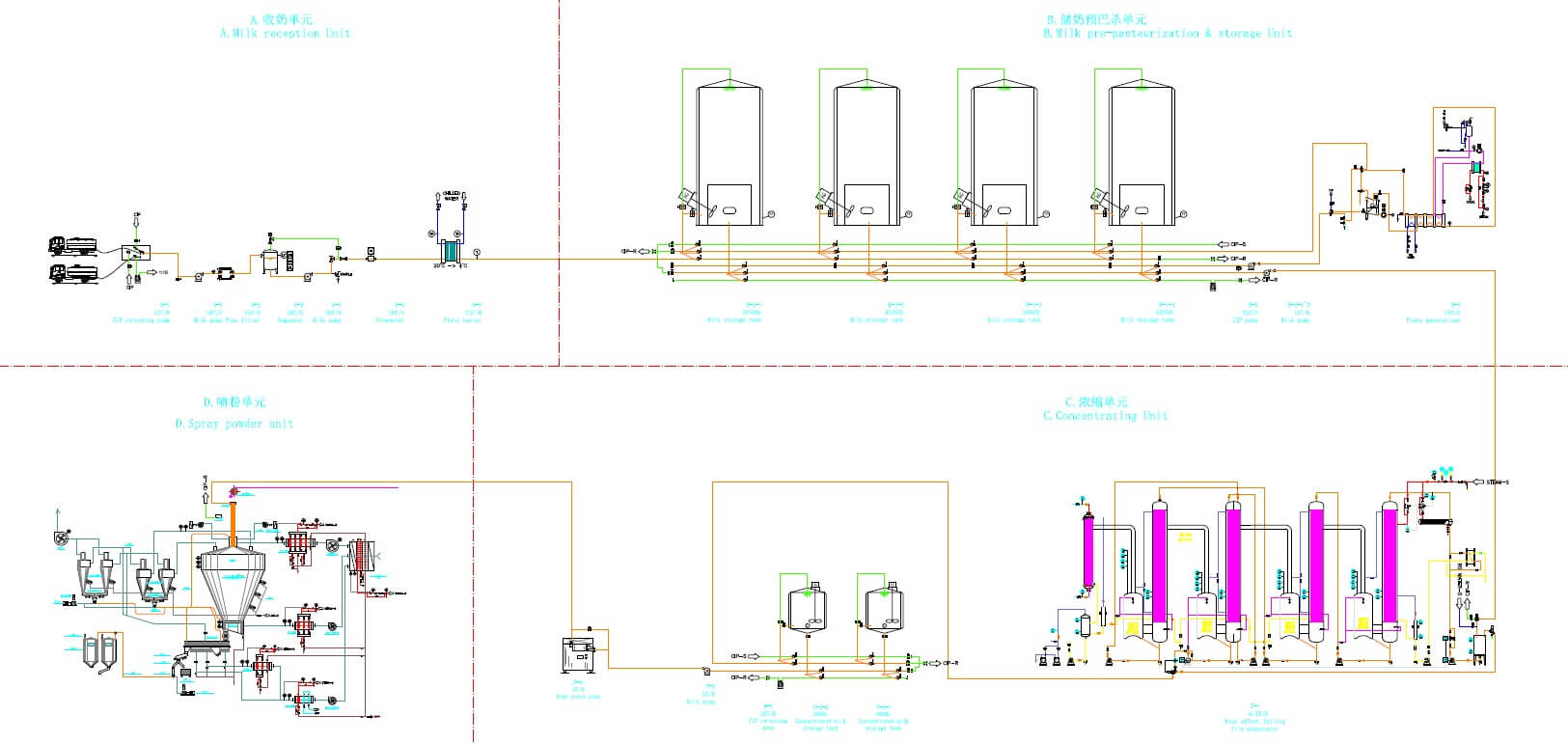
Milk Powder Production Line Key Machine Introduction
Milk receiving and storage unit
As in the milk powder processing plant, there will need a very large quantity of fresh raw milk, so raw milk receiving and quality checking and storage are necessary to ensure the efficient, hygienic, and safe handling of milk from the point of delivery to storage before further processing. Here’s an overview of the process and key components:
Fresh milk receiving and unloading: fresh milk is transported by truck to the milk processing factory, during transportation, the milk must maintain a low temperature to prevent the bacteria reproduction rapidly. Then the fresh milk will be pumped into milk-receiving tanks by the flowmeter on milk pipelines, and a double pipeline filter can be installed to remove all the impurities in milk during transferring.
Fresh milk quality checking: Get a sample of fresh milk do check the color, temperature, fat content, protein content, bacterial count, antibiotics, and other impurities before storage in the milk silo tanks.
Fresh milk cooling and storage: After checking the milk quality, the qualified fresh milk will be cooled to 4℃ and pumped into the milk silo tanks for further processing. During storage, the milk must keep 4 degrees, to realize this, the milk silo tanks must insulation and can feed into ice water in the jacket to cool the milk.
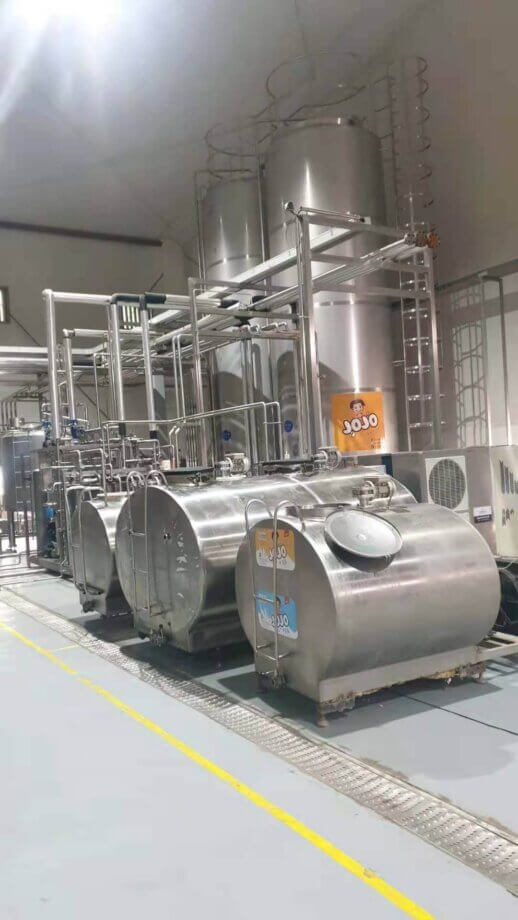
Milk preheating and separation machine
Fresh milk before separation, the solid content is about 8%, after the centrifuge separation, the milk solid content is about 12%.
Centrifugal separation is an indispensable step in the production of skimmed milk powder. After the raw milk is checked and accepted, it is preheated to 35-38℃, and then centrifuged separation. After separation, both cream and skim milk can be obtained. The fat content of the separated skim milk does not exceed 0.1%.
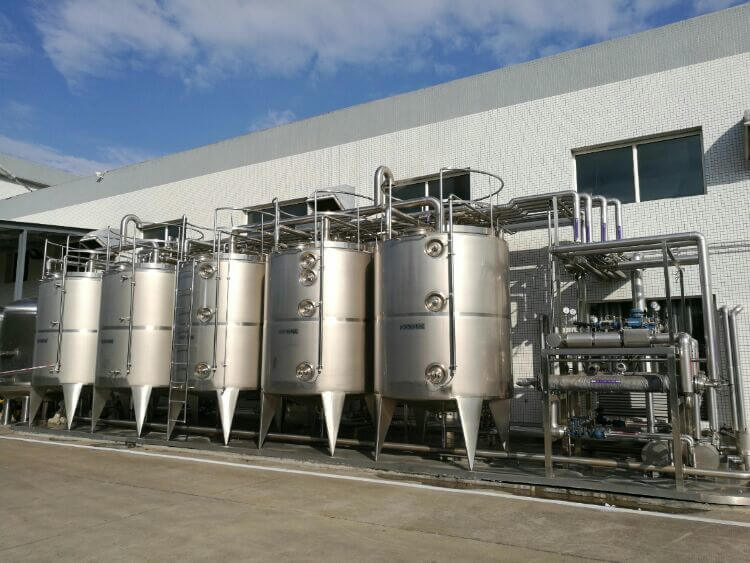
Milk homogenization and pasteurization machine
When raw milk is centrifuged separation and pressure spray drying, it will be mechanically squeezed and impacted by centrifuges and high-pressure pumps to varying degrees, and has a certain homogenization effect. Therefore, when processing whole milk powder, homogenization is not necessary, but if standardization is carried out and cream or skimmed milk is added, homogenization is required. First, the raw milk is heated to about 60°C and homogenized with a pressure of 20Mpa. After the homogenization is completed, the milk is pasteurized by a plate type pasteurizer, the pasteurizing technological flowchart is 85-87℃ hold for 15S, and then the pasteurized milk will be stored in the milk storage tank.
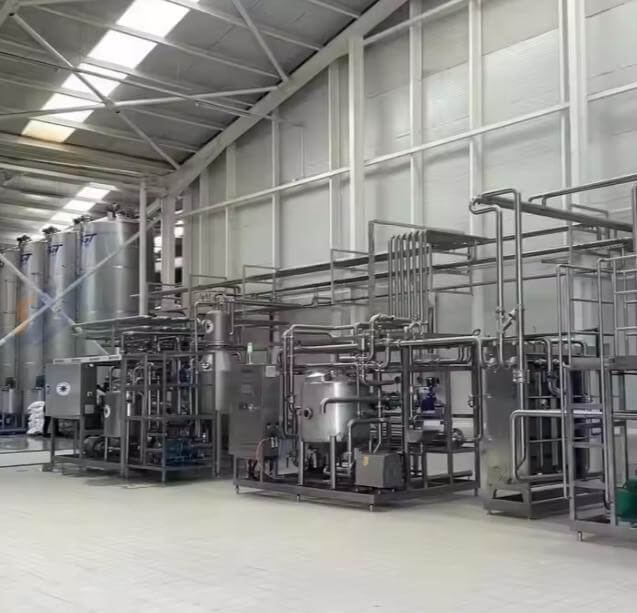
Milk vacuum concentration machine
Fresh milk with 8%-12% solid content will be evaporated to 45% solid content by the falling film evaporator.
Concentration is the use of heating to vaporize part of the water in the milk and continuously remove it, thereby increasing the dry matter content in the milk. The pre-treated milk uses a vacuum falling film concentration evaporator to concentrate to a dry matter content of 45%-55%, so that the concentrated milk is 1/4 of the original milk volume, and the temperature of the concentrated milk is generally about 47-50°C. Evaporative concentration is an indispensable process for the production of high-quality milk powder. Without pre-concentration, the milk powder particles will be very small and contain a lot of air, and the shelf life will be shortened.
Milk evaporation adopts a multi-effect multi-process falling film evaporator. The milk is distributed into the film tube twice or more than twice in the evaporator so that the film is divided into two or more times in the same evaporation area, which increases the flow rate and thickens the material film, which is not easy to scale and coke tubes, bacteria are not easy to reproduce, and the running time is long, reducing the number of cleaning times and cleaning costs.
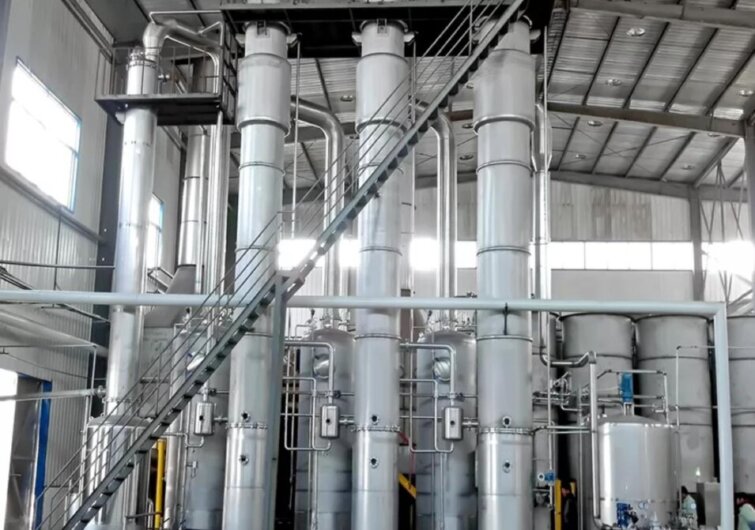
Milk spray drying machine
In the spray dryer, the concentrated milk will be evaporated from 45% solid content to 97% solid content milk powder.
The spray drying is divided into two stages. In the first stage, the concentrated milk is pumped to the drying tower for spray drying. In the drying room, Under the protection of the annular air curtain, the hot air quickly merges with the spray droplets through the diversion hot air distributor, so that the droplets are vaporized in an instant in 0.4 seconds. The pressure of the hot air makes the dried powder quickly blown into the built-in fluidized bed at the bottom. the temperature of the milk powder does not exceed 75°C.
The second stage is fluidized bed drying, the function of the fluidized bed dryer is to remove excess humidity and cool down the milk powder, and then dry into milk powder with a water content of 2%-3%.
The fine powder recovered by the powder catcher can also be re-polymerized and granulated through the built-in fluidized bed at the top or bottom of the tower, thereby improving the instant solubility of the product.
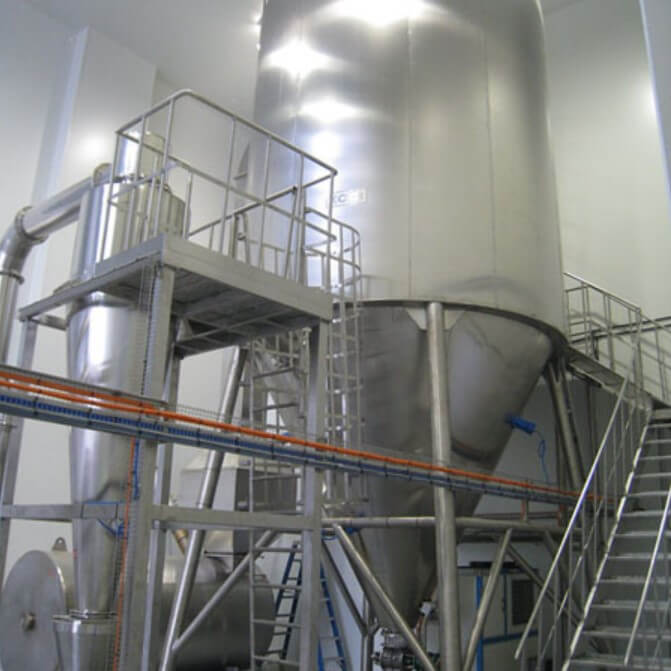
Milk powder filling machine
The milk powder can be filled into metal cans, pouches and foil composite bags. Industrial milk powder is packaged in large bags of 25kg, and household packages are packaged under 1kg, and small packages are packaged in tinplate cans or plastic bags. The shelf life is 18 months, and the shelf life can be extended if nitrogen is filled.
CIP system for milk powder production plant
The CIP system connects pipelines, pumps, tanks and other transportation and production components together to form a circuit, and then pumps a series of cleaning and rinsing solutions through the circuit at different temperatures, the purpose of which is to soak, separate and clean any residual debris, dirt or sediment in equipment and pipeline to make sure all whole milk powder production line with hygienic and clean.
The frequency of the CIP cleaning is very important for high-quality milk powder production. The tanks, pipelines and pasteurizers will be cleaned every day/shift to make sure the product contact surface is always clean; For the milk evaporator and milk powder spray dryer, once a week thoroughly CIP cleaning will be suggested.
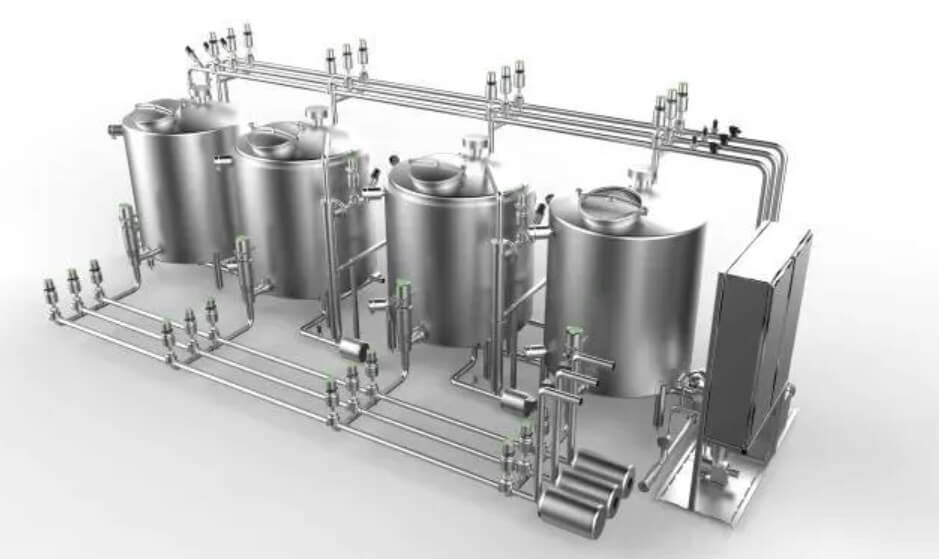