Project Description
Enzymatic Hydrolysis Tank
Enzymatic Hydrolysis Tank Description
This series of enzymatic hydrolysis tanks is a fully enclosed, vertical structure sanitary and clean enzymatic hydrolysis reaction equipment. It has been widely used in enzymatic hydrolysis technology in food, beverage, biological engineering, Enzymes are used as catalysts for substances in the pharmaceutical and other industries, and full enzymatic hydrolysis reactions are carried out with the help of the operation of the agitator under suitable temperature and pH conditions.
Enzymatic hydrolysis tank is specially used for fruit and vegetable juice, animal and plant and other substances. Enzymes are used as catalysts for decomposition reaction. The materials in the tank decompose various organic polymers under suitable temperature and pH conditions by the operation of agitator to make them organic Small molecules facilitate the assimilation of the body.
The enzymolysis tank is triple layers, which have the functions of heating, insulation, heat preservation and stirring. After the enzymolysis is completed, steam can be introduced into the enzymolysis tank jacket to raise the temperature of the material to 80-100℃ to inactivate the enzyme. After the enzyme has been inactivated, the material can be cooling down certain temperature through cooling water medium. The temperature of the materials in the enzymolysis tank is around 50℃ during enzymolysis, and the enzyme inactivation temperature is 90℃. Therefore, users need to prepare their own heat medium. The common heat medium is steam or hot water.
Fruit juice contains substances such as protein and starch, which are easy to denature and difficult to preserve. These substances must be enzymatically hydrolyzed during the production process. Generally, pectinase, amylase, 43# enzyme is added to decompose the protein and starch in the juice. Molecular compound. The juice feed generally enters from the bottom of the tank. When the juice reaches the agitator shaft, the agitator is turned on. When the tank is full, the agitator stops and the enzyme is added from the top of the tank.
The enzyme is kept at 50-53°C in the tank and allowed to stand for 90 minutes until the decomposition is basically completed. After the enzymolysis, add gelatin, stir for 5 minutes, turn off the stirring, let it stand for 35 minutes, and then discharge. The total working time of the enzymolysis process is 130-150min, so in order to ensure continuous production, the enzymolysis tank is generally equipped with 3-4 sets.
For different materials, choose a suitable and effective mixing device to achieve the purpose of full mixing and efficient mixing. Before quotation, users need to provide material name, material characteristics (PH value, viscosity value, etc.), enzymatic hydrolysis process, tank volume and so on.
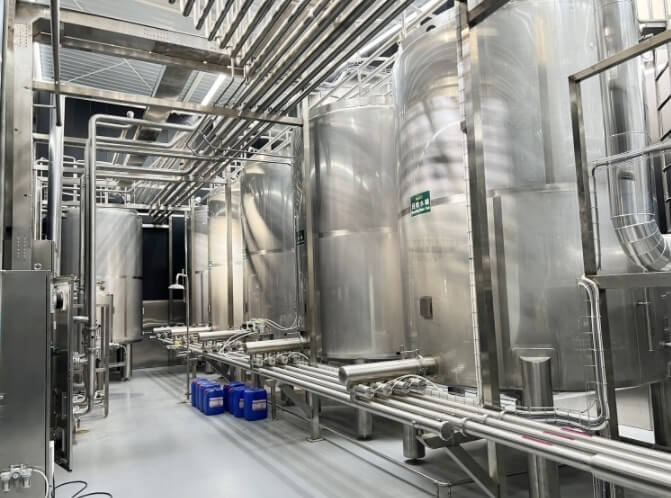
Enzymatic Hydrolysis Tank Feature
- Enzymolysis tank can be equipped with quick-opening sanitary manhole, sight glass, thermometer, respirator, CIP cleaning ball, material inlet and outlet, sampling port, PH meter port, SIP sterilization port, anti-vortex plate, liquid level indicator, hot and cold medium inlet and outlet, agitatior device, etc.
- The surface of the inner tank body is mirror polished, and the openings of the inlet and outlet pipes, sight glasses, manholes and the welding place of the inner tank body are all used in the arc transition of the inner tank body, smooth and easy to clean, no dead corners, and the production process is hygienic and stable.
- The outer surface of the tank is mirror-polished with stainless steel plate, and the primary color is matt or frosted, and the appearance is beautiful and clean.
- An insulation layer is set between the jacket and the outer cylinder, and the inside is filled with high temperature resistant, anti-aging rock wool or pearl wool for heat preservation, which not only heats insulation, but also prevents the operator from scalding.
- The tank material can be made into SUS304 or SUS316L according to customer requirements.
- The top of the tank is equipped with a paddle-type agitator to make the material stored in the tank more fully agitated. The mixing motor is controlled by frequency conversion, which makes the service life of the motor longer. A thermometer and a washer are installed on the cylinder to facilitate the measurement of the temperature of the liquid material in the tank and the cleaning of the tank liner.
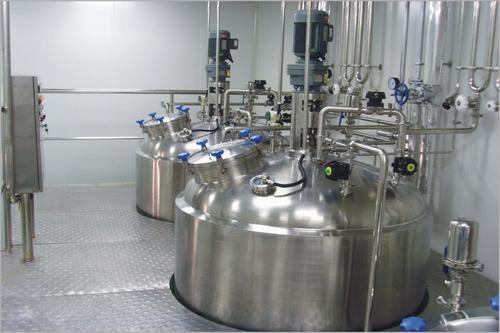
Enzymolysis Tank Application
Enzymolysis tanks in the food industry are designed to provide optimal conditions for enzymatic reactions, including temperature control, pH regulation, and agitation. They allow for controlled and efficient enzymatic hydrolysis, resulting in improved product quality, functionality, and flavor.
- Protein Hydrolysis: Enzymolysis tanks are used to break down proteins into smaller peptides or amino acids. This process, known as protein hydrolysis, enhances the digestibility, nutritional value, and functional properties of proteins. Enzymolysis tanks are employed in the production of protein hydrolysates used as ingredients in infant formulas, sports nutrition products, dietary supplements, and food products for individuals with specific dietary needs.
- Flavor Development: Enzymolysis tanks are utilized in the food industry to develop and enhance flavors. Enzymes are used to break down precursor compounds into flavor-active molecules, leading to the formation of desirable flavors. Enzymolysis tanks are employed in the production of fermented foods, such as cheese, soy sauce, and fermented beverages, where enzymes contribute to the development of characteristic flavors and aromas.
- Fruit Juice and Wine Production: Enzymolysis tanks play a crucial role in fruit juice and wine production. Enzymes, such as pectinases and cellulases, are used to break down cell walls and release juices from fruits. Enzymolysis tanks facilitate the enzymatic hydrolysis of pectin, cellulose, and other components, resulting in increased juice extraction, improved clarity, and enhanced flavor profiles.
- Starch Conversion: Enzymolysis tanks are used in the conversion of starch into sugars. Enzymes such as amylases are employed to break down starch molecules into fermentable sugars like glucose and maltose. This process is important in the production of various food products, including syrups, sweeteners, and fermented beverages like beer and spirits.
- Dairy Processing: Enzymolysis tanks find application in dairy processing, particularly in cheese production. Enzymes like rennet are used to coagulate milk and form curds during the cheese-making process. Enzymolysis tanks provide an environment where enzymes can efficiently break down proteins and facilitate the formation of curds, which are then processed into different types of cheeses.
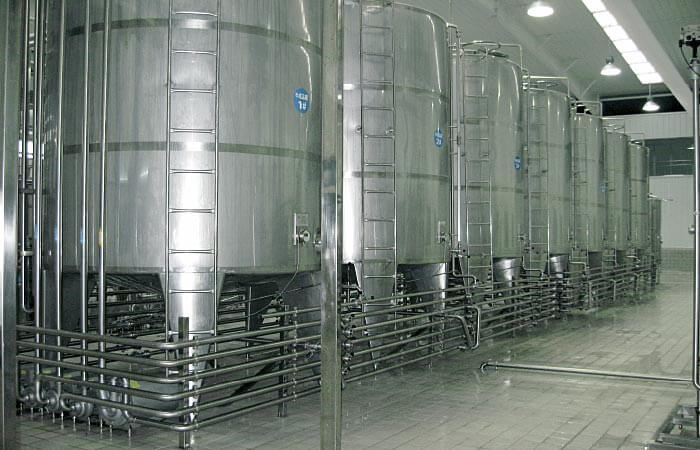
Use and Maintenance
Before using the batching tank, the inside of the tank must be cleaned with light hot water, and then sterilized with steam. Various materials enter the tank through the material pipe fixed on the tank lid, or open the hand hole to pour in. The input material should not be filled too full.
After the ingredients are finished, drain the remaining materials in the tank, rinse with warm water as soon as possible, brush off the attached materials, and then use 75℃-85℃ alkaline water to clean the inner wall of the container. And rinse with clean water, to be used next time.
Always pay attention to the working conditions of the entire equipment and reducer. If the lubricating oil of the reducer is insufficient, it should be refilled and replaced every six months (40# engine oil). When the equipment is not in use, be sure to clean the inside and outside with warm water instead of saltwater. Rinse to avoid corrosion, often scrub the cylinder body to keep the exterior clean and the inner tank bright, so as to achieve the purpose of durability.
Technical Parameter
Tank Volume | 300L | 500L | 1000L | 2000L | 3000L | 5000L | 10000L | 20000L | |||||||
---|---|---|---|---|---|---|---|---|---|---|---|---|---|---|---|
Tank Inner Diameter(mm) | φ800 | φ900 | φ1100 | φ1400 | φ1600 | φ1800 | φ2100 | φ2700 | |||||||
Heating Exchanger Area(m^2) | 2.0 | 2.7 | 4.5 | 7.5 | 10 | 13.5 | 22 | 33 | |||||||
Power(KW) | 0.55 | 0.75 | 1.1 | 2.2 | 3.0 | 4.0 | 5.5 | 7.5 | |||||||
Agitator Speed | 17-155RPM Stepless frequency conversion speed regulation | ||||||||||||||
Agitator Style | Frame type, anchor type, propeller type, paddle type | ||||||||||||||
Working pressure(Mpa) | 0.08-0.3mpa in jacket, 0.1mpa-0.15mpa in tank | ||||||||||||||
Working temperature | <138℃ in jacket; <100℃ in tank | ||||||||||||||
PH Vlaue | 2-12 |