In food and beverage plant, food-grade stainless steel plays an important role. Almost all food processing equipment requires food-grade stainless steel materials to ensure that the food produced is safe and hygienic. Stainless steel tanks, pipelines, valves, transfer pumps, unit machines such as sterilizers, cleaning machines, filling machines, etc., all need stainless steel SUS304 or SUS316L. Therefore, the selection and processing of stainless steel are directly related to the safety and high quality of the final product produced in liquid food and beverage processing plant. Today we introduce some basic knowledge and surface treatment of food-grade stainless steel 304 and 316:
Difference Between SUS304 and SUS316L
Food-grade SUS304 is the most common type of steel, must contain more than 18% chromium, and more than 8% nickel content, widely used in food and medical industry. As a widely used steel, it has good corrosion resistance, heat resistance, food hygiene, low-temperature strength and mechanical properties; good hot workability such as stamping and bending, no heat treatment hardening phenomenon (non-magnetic, working temperature- 196℃~800℃), in the general food and beverage processing process, there is no problem in using food-grade SUS304 material as the main material of the equipment.
Food grade SUS 316 is also austenitic stainless steel. It not only contains chromium and nickel but also molybdenum, which improves its overall corrosion resistance as well as its mechanical properties at high temperatures. SUS316 is stronger at elevated temperatures and has improved corrosion resistance than SUS304, especially to sulfates, phosphates and other salts and reducing acids such as Sulfuric acid and phosphoric acid. The Model 316L is an ultra-low carbon version of the Model 316. SUS316L material is used in highly acidic materials or materials containing chloride ions in food industry or in the pharmaceutical industry with high hygiene requirements.
Both SUS304 and SUS316 austenitic stainless steel have good corrosion resistance and high-temperature oxidation resistance, and their main purpose is to prevent corrosion and rust. The corrosion resistance of stainless steel mainly depends on the surface passivation film. If the film is incomplete or defective, the stainless steel will still be corroded.
Â
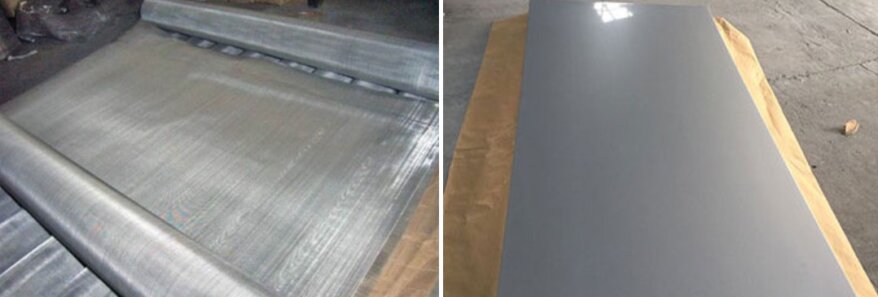
Surface Treatment Process Of Food Grade Stainless Steel Equipment
Stainless steel surface polishing treatment
Mechanical Polishing is the most common surface treatment method for stainless steel plates, tubes and welding seams. it can not only make stainless steel look beautiful, but also can prevent steel from rusting. The reason why stainless steel does not rust is mainly that the metal is an alloy, molecules of this metal are inactive and not easy to chemically react with air. But it does not represent that stainless steel is 100% rust-free, depending on how and where it is used.
After the stainless steel is polished mechanically, a protective film is formed on the stainless steel surface. This kind of film better isolates the chemical reaction of water, air and other molecules. Make the stainless steel surface molecules more compact and firm, enhance the corrosion resistance of stainless steel, and improve the service life of stainless steel. Ordinary mechanical polishing, the inner surface of the stainless steel 2B plate is 300 mesh, and the outer surface is 200 mesh, which can meet the food-grade requirements.
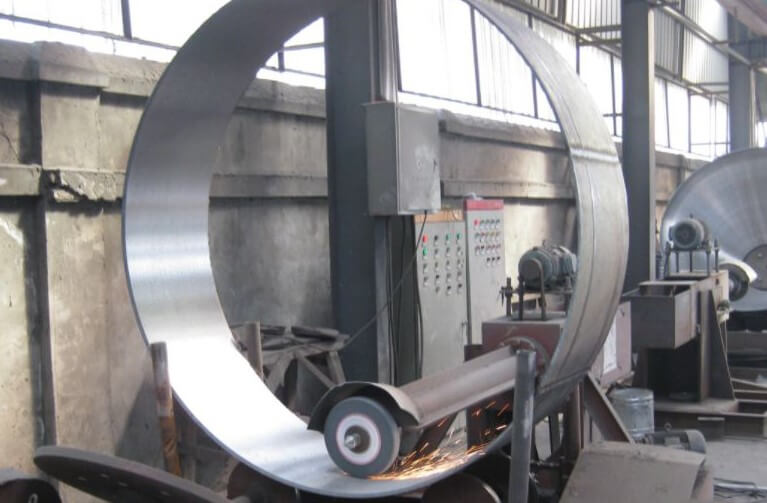
For customers with higher requirements, mirror polishing can also be used – it can make the stainless steel surface bright and clear. The mirror stainless steel surface can be divided into 8k, 10k, 12k according to the grade. The higher the grade, the brighter, and the surface effect are better! Mirror polishing on the surface of stainless steel reflects the true color of the metal by removing the surface roughness and oxide scale (similar to the effect of mirror reflection). Generally, the surface roughness value Ra≤ 0.05 μm, and the surface finish is greater than 10, can be called “mirror” polish.
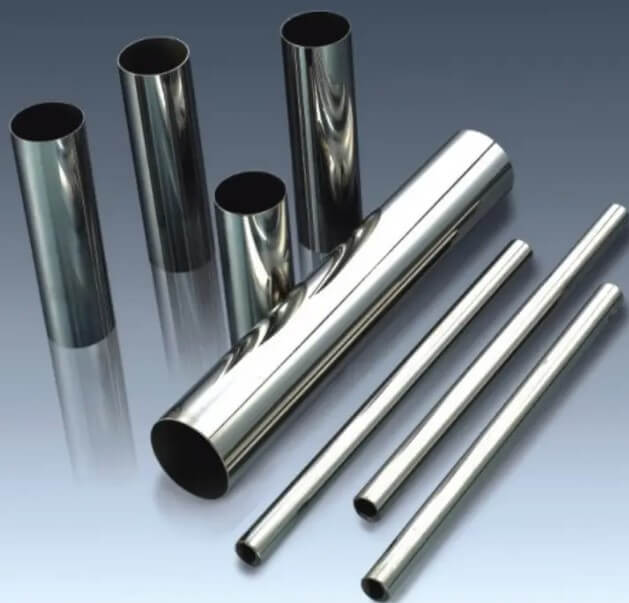
Stainless steel surface sandblasting treatmentÂ
Sandblasting the surface of stainless steel mainly uses the method of spraying micro glass beads to remove the black oxide scale on the surface. The sandblasting treatment can improve the mechanical properties and the fatigue resistance of the workpiece, increase the adhesion between the coating, and the durability of the coating film to be prolonged.
Sandblasting has many functions, it can remove stainless steel castings, the oxide scale on the surface of the forging or heat treatment can also remove the rust, carbon deposits, welding slag and other debris on the surface, and can also remove the edge burrs and some slight directional scratches of the parts. Sandblasting can also improve the surface roughness of stainless steel parts, thereby improving the adhesion of the back surface coating. Sandblasting can also be used as a means of surface decoration treatment.
The stainless steel must be degreased before dry sandblasting, and then dried to avoid affecting the quality of sandblasting, and then select the appropriate sand and air pressure according to the thickness of the parts.
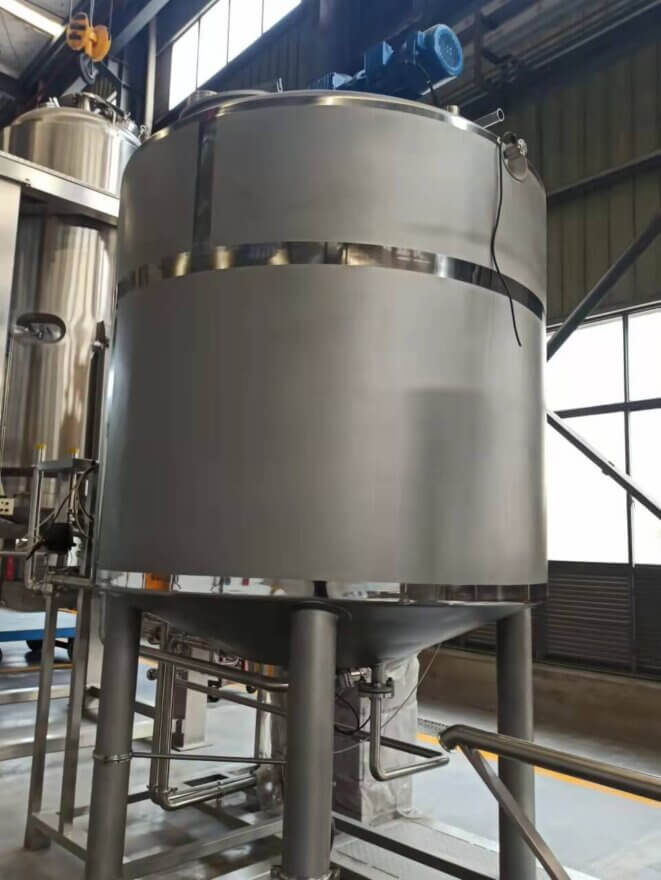
Stainless steel surface passivation treatmentÂ
Acid cleaning and passivation – After the installation of food processing equipment or pipelines, it needs to be acid washed and passivated. In engineering, acid cleaning and passivation is usually carried out, so that the corrosion resistance potential of stainless steel can be maximized. In the process of forming, assembling, welding seam inspection (such as flaw detection, and pressure test) and construction marking of stainless steel equipment and components, surface oil, rust, non-metallic dirt, low-melting metal contamination, paint, welding slag and splashes, etc., these substances affect the surface quality of stainless steel equipment and components, destroy the oxide film on the surface, reduce the general corrosion resistance and local corrosion resistance of steel (including pitting corrosion, crevice corrosion), and even cause corrosion cracking.
Stainless steel surface cleaning, acid cleaning and passivation not only maximize corrosion resistance but also prevent product contamination and achieves aesthetics
Stainless steel workpieces will form an oxide film when placed in the air, but the protection of this film is not perfect. Usually, thorough cleaning, including alkali cleaning and acid cleaning, and then passivation with an oxidizing agent are required to ensure the integrity and stability of the passivation film. One of the purposes of acid cleaning is to create favorable conditions for passivation treatment to ensure the formation of high-quality passivation films.
Â
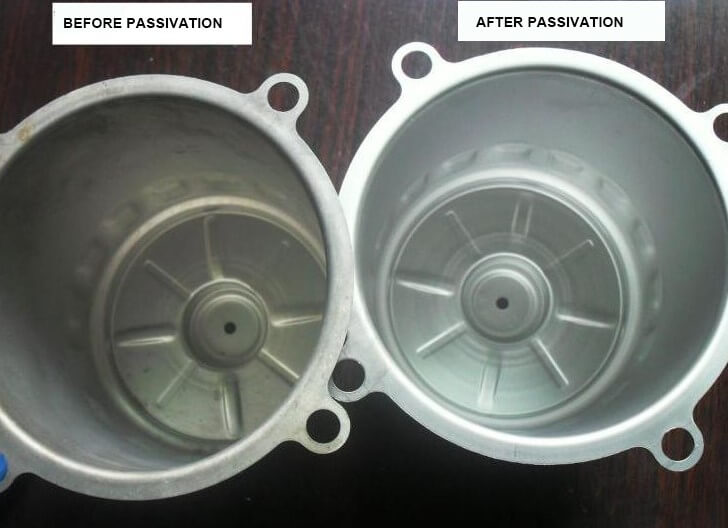