Sugarcane Juice Processing Plant Description
- The world sugar cane agro-industry was responsible for producing 155.7 million tons of sugar, Brazil, India, USA, China and Thailand are the top countries for processing sugarcane. Sugarcane juice is very rich in sugar and water, which can quickly replenish the body’s energy and water after drinking. If there is heat in summer, drinking sugarcane juice can produce body fluids to quench thirst and improve symptoms. In addition, due to the cold nature of sugarcane juice, it can clear away heat and detoxify, so it can effectively alleviate the adverse symptoms of cough or excessive phlegm.
- Sugarcane processing is focused on the production of cane sugar (sucrose) and sugarcane juice from sugarcane. Other products of the processing include bagasse, molasses, and filtercake. Bagasse, the residual woody fiber of the cane, is used for several purposes: fuel for the boilers and lime kilns, production of numerous paper and paperboard products and reconstituted panelboard, agricultural mulch, and as a raw material for the production of chemicals. Bagasse and bagasse residue are primarily used as a fuel source for the boilers in the generation of process steam. Thus, bagasse is a renewable resource. Dried filtercake is used as an animal feed supplement, fertilizer, and source of sugarcane wax.
- Small freshly squeezed sugarcane juice production plant adopts advanced PLC programmable automatic control, man-machine interface touch screen, and is equipped with a CIP cleaning system, which can clean the machine conveniently. The whole sugarcane juice processing machine is made of SUS304 material, with high efficiency, good hygiene conditions.
- The whole sugarcane juice processing plant includes a sugarcane washing machine, sugarcane peeling machine, sugarcane juice extracting machine, sugarcane juice filtering machine, sugarcane juice homogenizer, sterilizer and filler, CIP system.
- Small freshly squeezed sugarcane juice beverage production line NFC sugarcane juice filling equipment processing machinery is suitable for the filling of bottled or canned beverages, the output is available from 3000 to 20,000 bottles per hour, and the inverter control technology and output indicator function are used to achieve output adjust. The equipment is equipped with a complete reflux system, while avoiding secondary pollution and oxidation of the beverage, and can meet the technical requirements for hot filling of sugarcane juice tea beverages below 95°C. The body structure is good, the control system is complete, the operation is convenient, and the degree of automation is high. Parts in contact with materials are made of stainless steel, which is hygienic and easy to clean.
- The end products of sugarcane juice can be filled into PET bottles or glass bottles, metal cans, cartons, aseptic bags or pouches. The capacity is from 500kg/h-5000kg/h.
- The sugarcane juice can also use falling film evaporator to make the concentrated sugarcane juice, and the end concentrated sugarcane juice is about 60-65brix.
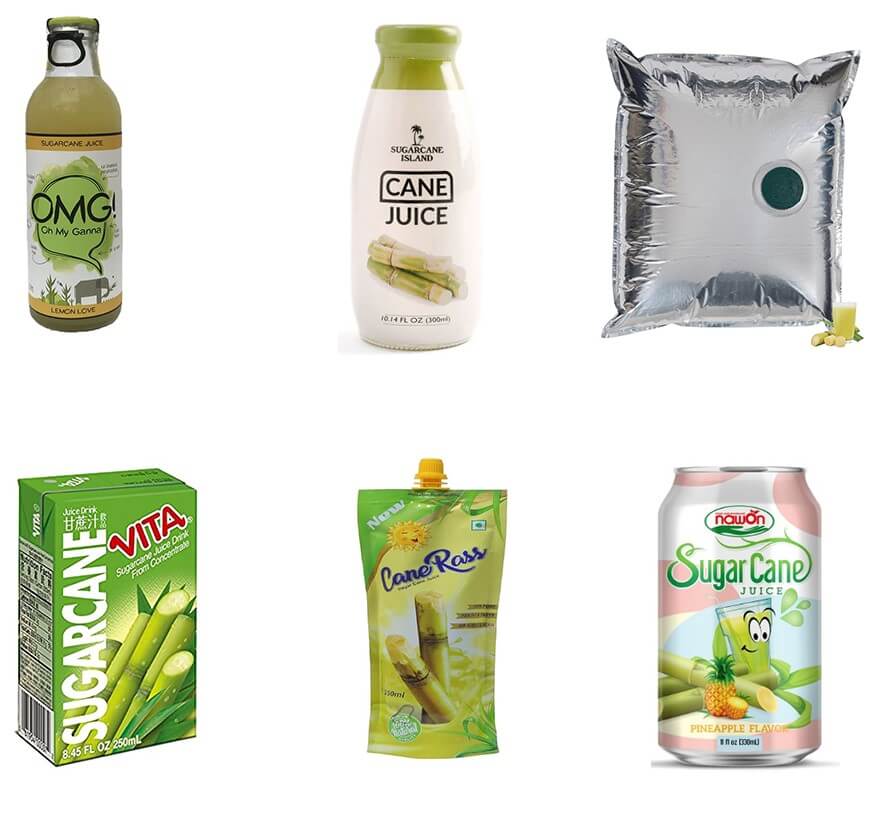
Sugarcane Juice Processing Plant Technological FlowchartÂ
The fresh sugarcane will be washed by the brush washing machine, after washing, the sugarcane will be transferred to peeling machine for peeling by man hand. Then the sugarcane can be cut into pieces and feed into a screw juice extractor or feed into sugarcane juicer machine. After the juice is obtained, then we will use a double filter and centrifuge separator to remove the solids into the sugarcane juice, then blend with flavor agents in the juice blending tank. After that, the sugarcane juice will be homogenized, pasteurized and filled into bottles or cans.
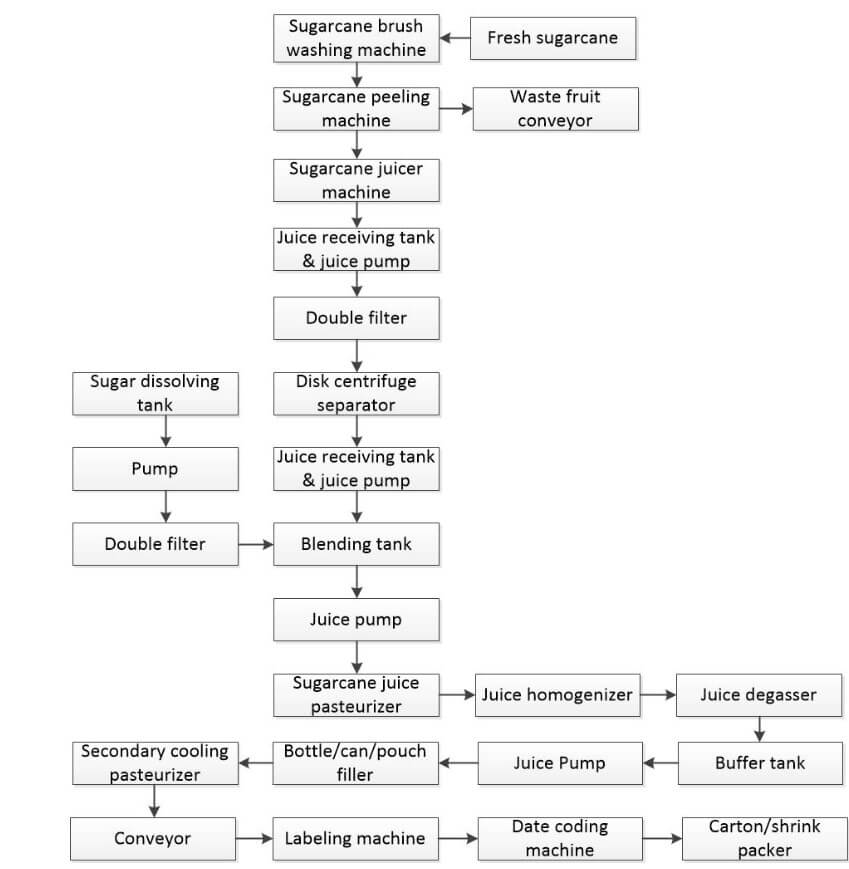
Sugarcane Juice Processing Plant Main Machine IntroductionÂ
- Selection of the original sugarcane fruit: The original fruit should be fresh, full and high-quality fruits, and rotten and contaminated fruits should be eliminated.
- Sugarcane washing: Thorough brush washing machine of the original fruit is to reduce the pollution caused during production, and more attention should be paid when not peeling and squeezing juice. Therefore, the sediment and impurities on the peel must be washed with running water. If necessary, rinse with solution and then rinse with water.
- Peeling and juicing sugarcane: Use a beater to beat and peel, and the pulp is wrapped in a special fruit cloth to squeeze the sugarcane juice. The juice yield can reach 70% and more. Or pour the washed fruit into a press to squeeze the juice, and then filter the peel, fruit seeds and part of the crude fiber through a scraper filter.
- sugarcane juice filtration: The sugarcane juice is filtered and separated by a centrifugal filter to remove the remaining peel, seeds, part of fiber, broken fruit pieces and impurities.
- Sugarcane juice blending: The sugarcane juice after coarse filtration is first diluted with water to a refractive index of 4%. Then mix according to the ratio of 90 kilograms of sugar cane juice and 10 kilograms of white granulated sugar, stirring constantly, so that the sugar is completely melted.
- Sugarcane juice homogenization: The blended sugarcane juice is homogenized by a homogenizer, which can further break the fine pulp and maintain the uniform turbidity of the sugarcane juice. The pressure of the homogenizer is 20-30 MPa.
- Sugarcane Juice Pasteurization: The sugarcane juice will be pasteurized by plate pasteurizer. Heat the filtered sugarcane juice to 90~100℃, keep it for 1~2min, then cool it to 85℃.
- Filling: Heat the sugarcane juice at 85°C~95°C and quickly flow to the filling machine for filling and capping. The filling machine adopts a hanging bottle neck method to drive the bottle mouth, which is convenient to change the bottle shape, fast and labor-saving. The automatic stop system for the stuck bottle, the noise when the whole machine is running, the 200℃ high-temperature sanitary pneumatic filling valve, it is safe, can meet the hot filling temperature above 85℃, and each runner is cleaned and adjusted independently. The GMP-compliant material storage tank has no hygienic vignetting left, which is more convenient to clean, and ensures the safety of interchange between filling materials.
- Sterilization and cooling: Sterilize quickly after sealing, the sterilization type is 5′-1O’/1OO°C, and then quickly cool to below 40°C.
Â