Project Description
Forced Circulation Evaporator
Application Range of Forced Circulation Evaporator
The forced circulation evaporator is suitable for concentrating products with high levels of solid material content and/or high viscosity like fruit puree(tomato paste, tropical fruit puree or mango puree), medicine products, it is widely used in food deep processing, biochemical engineering, environmental protection engineering, waste liquid recovery and treatment, and chemical industry.
The basic task of an evaporator is simple: to remove the solvent from a solution or slurry by evaporation. Raw fruit juice/puree is concentrated into high-solid and viscosity products by removing water from raw materials.
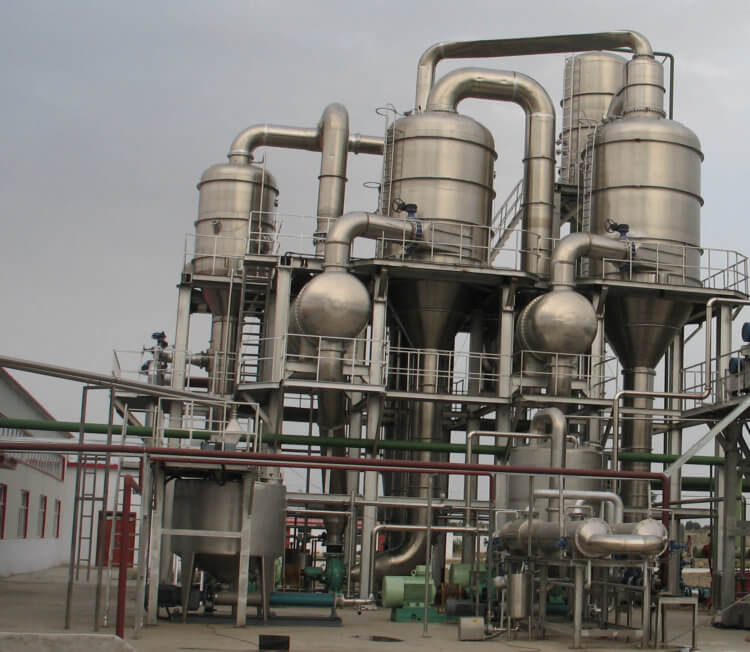
Forced Circulation Evaporator Composition
This equipment consists of multi-effect heater exchangers, separators, condensers, vacuum pumps, balance tank, material feeding pump, material discharge pump, vacuum pumps, electric control boxes, and all pipes and valves:
- Heat exchanger: This is the main component of the evaporator, and it is responsible for transferring heat to the liquid being evaporated.
- Circulation pump: The circulation pump is used to circulate the liquid through the heat exchanger at a high velocity, allowing for efficient heat transfer and evaporation.
- Separator: The separator is used to separate the vapor generated during the evaporation process from the liquid being evaporated.
- Condenser: The condenser is used to condense the vapor generated during the evaporation process back into a liquid form, which can be recycled or disposed of.
- Vacuum system: The vacuum system is used to maintain a low pressure inside the evaporator, which reduces the boiling point of the liquid being evaporated and allows for more efficient evaporation.
- Control system: The control system is used to monitor and control various parameters, such as temperature, pressure, and flow rate, to ensure optimal performance of the evaporator.
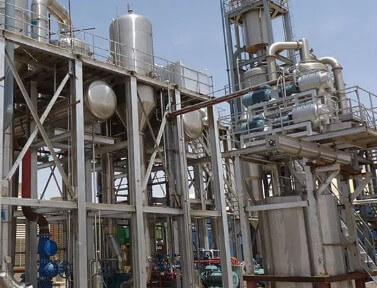
Forced Circulation Evaporator Feature
- Material: All parts in contact with the material are made of SUS304or SUS316 material. The equipment frame use the carbon steel with paint.
- Heat utilization of condensate water: The condensate water produced by the first-effect evaporator flows into the second-effect evaporator, and the sensible heat of the condensate is utilized. The condensate produced by the first and second effects enters the condensate pump and is discharged through the condenser.
- Energy-saving and consumption reduction, the secondary steam separated by the first-effect separator enters the second-effect heater for heating, and the secondary steam separated by the second-effect separator enters the condenser to condense, so the heat is reused and the steam is greatly saved Consumption, while also saving cooling water circulation.
- Low-temperature concentration. The entire evaporation process of this equipment is in a vacuum state, which reduces the evaporation temperature of the material, making the material difficult to scale during the heating and evaporation process, and can better meet the requirements for the concentration of heat-sensitive fruit juice, Chinese medicine, western medicine and heat-sensitive materials.
- Heaters and evaporators are equipped with thermal insulation layers. The polyurethane foam is used for thermal insulation, and the outer surface is matt treated. The entire process of heating, evaporation, and concentration is completed in a fully closed environment.
- The large concentration ratio simplifies the process, shortens the concentration-time, ensure product quality.
- All parts in the equipment, are made by known companies, such as Durrex rotor pump, SpiraxSarco steam valves, Yokogawa level sensors, Maselli refractometer, Siemens PLC, Danfoss inverter, Schneider Touch-Screen, etc, which can guarantee long working life.
- The whole system is controlled by PLC, the operator could control the equipment very easily, all parameters, like temperatures, vacuums, levels, Brix, etc, are displayed on the touch-screen, and could be changed quickly and easily as you need. The PID (Proportion Integration Differentiation) controlling method is applied here, which means a highly precise and stable running situation.
- The machine is equipped with CIP function, which is easy to clean and meeting the food grade hygiene conditions.
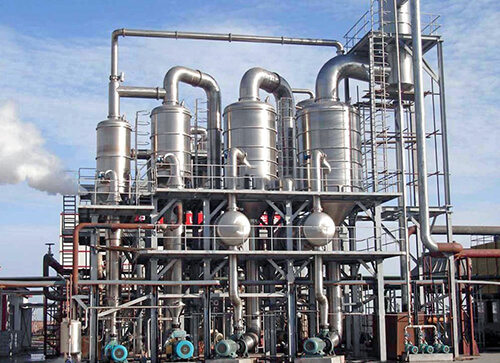
Forced Circulation Evaporator Working Process
The primary steam(boil steam) enters the one-effect heating chamber to heat the material liquid, the material forms a certain pressure difference between the heating chamber and the separation chamber. Under this action, the material continuously rises from the bottom of the heating chamber to the top, and finally spray into the one-effect evaporate chamber through one effect separator. The nozzle at the top sprays into the one-effect evaporation chamber and the material liquid flows back from the curve at the bottom of the evaporation separation chamber to the bottom of the heating chamber. After being heated again, it is sprayed into the evaporation chamber tangentially through the nozzle at the top of the one-effect heating chamber to form a cycle. The secondary steam is separated from the material in the rotating motion. After the material liquid is heated, it is sprayed into the evaporation chamber through a nozzle, and the water is quickly evaporated, and the material is continuously heated and evaporated. The secondary vapor that evaporates in a vacuum is in a vacuum. Under the action, it quickly enters the second-effect heating chamber to heat the second-effect material liquid, and the secondary steam evaporated by the second-effect enters the shell of the preheater and the condenser cooler, and the cooling circulating water enters the tube of the condenser cooler, and cools from the condensation. The top of the tube comes out of the tube and can be returned to the cooling tower. After passing through the cooling tower, it enters the cooling pool to form a cycle. The secondary steam is condensed into water in the condensing cooler and enters the condensate pump. The need to use a collection place, or to the whole plant or recycled into the cooling tower.
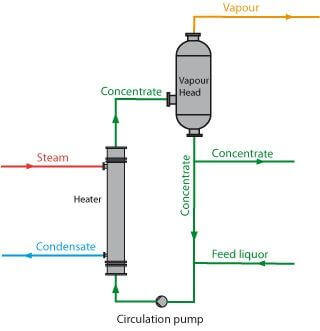
Technical Parameter
Model | Single effect | Double effect | Triple effect | Forth effect | Fifth effect | ||||
---|---|---|---|---|---|---|---|---|---|
Evaporating temperature | 45-90 ℃ | ||||||||
Steam consumption | Depend on the capacity and evaporating temperature of the material | ||||||||
Steam pressure | 0.5-0.8MPA | ||||||||
Material discharge brix | Depend on the material character | ||||||||
Material Feeding brix | Depend on the material character | ||||||||
Capacity(LPH) | 300-2000LPH | 1200-4000LPH | 3000-15000LPH | 8000-50000LPH | 10000-100000LPH |