Project Description
Disk Centrifuge Separator
Introduction of Disk Centrifuge Separator
A disk centrifuge separator is a machine used to separate different components of a liquid mixture based on their density. In the food and beverage industry, disk centrifuge separators are commonly used to separate solids or fats from liquids.
The disk centrifuge separator also called disk stack separator is a kind of vertical centrifuge that can separate solid-liquid and liquid-liquid quickly and continuously. The rotating drum is installed on the upper end of the vertical shaft and driven by a motor through a transmission device to rotate at high speed.
The separation process in a disk centrifuge separator involves spinning a set of disks at high speed to create centrifugal force, which causes the heavy phase to move towards the outer edges of the disks while the light phase particles move towards the center. The separated components can then be collected separately.
The disk separator is specially used for two-phase and three-phase separation. The two-phase separation is to separate the suspended solid from the liquid or separate two liquids that have different specific gravity and are immiscible. The three-phase separation is to separate the two immiscible liquid phases and a phase of solid at the same time.
Disk stack separators and decanters are also able to produce of juices that are very trub stable, classification of the trub particles takes place in the centrifuge. Any undesired, coarse trub particles can be separated according to clients’ requirements to avoid undesired sediments in the juice.
Disk centrifuge separators are particularly useful in the food and beverage industry because they can handle large volumes of liquid and can separate solids with a high degree of efficiency, leading to improved product quality and reduced production costs. They are also easy to clean and maintain(with self-CIP cleaning function), which makes them ideal for use in food processing plants where hygiene is a top priority.
The disc centrifuge has a separation factor ranging from 8000 to 20000 and is typically used to process materials that are difficult to separate effectively using conventional centrifuges, such as highly dispersed liquid-liquid emulsions and liquid-solid suspensions containing small particles with slow sedimentation rates. It can separate suspensions with solid concentrations of less than 3%, and the diameter of the drum ranges from 150 to 1200mm. The separation technical parameters vary widely depending on the separation material.
The disk stack centrifuge separator has continuous production, high throughput and high efficiency, and low energy consumption, the differential speed is adapted automatically and extremely precisely feature.
The solid separation accuracy of the disk stack centrifuge is between 0.1-100μm and the solid content of the material that can be separated is between 0.1%-35%.
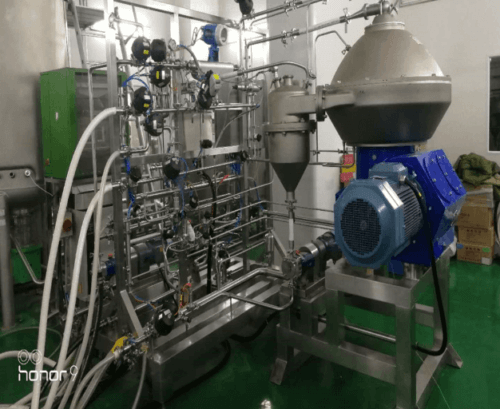
The Working Principle Of Disk Centrifuge Separator
The high-speed disc separator is a vertical centrifuge. The rotating drum is mounted on the upper end of the vertical shaft and driven by a motor through a transmission device to rotate at high speed. Inside the drum, there is a set of disc-shaped parts nested together. There is a small gap between the discs. The suspension is added to the drum through a feed tube located in the center of the drum. When the suspension flows through the gap between the discs, the solid particles settle to the discs under the action of the centrifuge to form a sediment. The sludge slides along the surface of the disc to disengage the disc and accumulate in the inner diameter part of the drum, and the separated liquid is discharged from the drum through the liquid outlet. The role of the disc is to shorten the settling distance of the solid particles and expand the settling area of the drum. Because the disc is installed in the drum, the production capacity of the separator is greatly improved. The solids accumulated in the drum are dismantled after the separator is shut down to be manually removed, or discharged from the drum through the slag discharge mechanism without stopping.
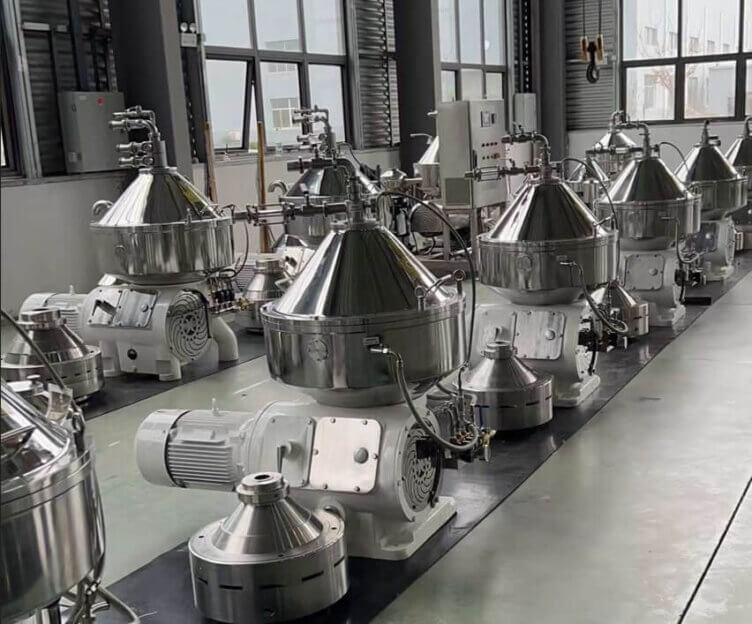
Disk Centrifuge Separator Composition
Disk centrifuge separators are composed of several parts that work together to separate liquids and solids based on their density. Here are the main components of a disk centrifuge separator:
- Bowl: The bowl is the central part of the separator and is where the separation process occurs. It is a cylindrical container that rotates at high speed and contains a set of disks that create centrifugal force.
- Disks: The disks are mounted vertically inside the bowl and are designed to create a series of thin layers of liquid. The number of disks used in a separator can vary depending on the specific application.
- Inlet and Outlet Ports: The inlet port is where the liquid mixture to be separated is fed into the separator, while the outlet port is where the separated liquids and solids are collected.
- Frame: The frame provides support for the bowl and the motor and ensures that the separator remains stable during operation.
- Motor: The motor is responsible for rotating the bowl and disks at high speeds to create centrifugal force.
- Control Panel: The control panel contains the necessary controls for operating the separator, such as speed controls and safety features.
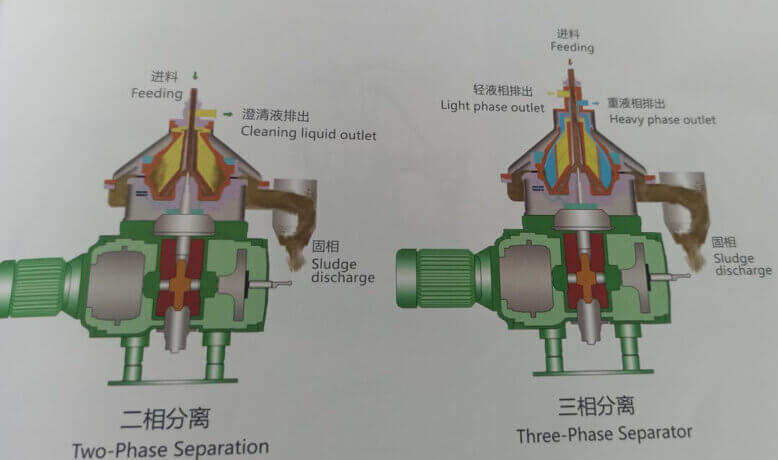
The Application of Disk Centrifuge Separator
Fruit and vegetable oil separation and purification:
As special separation equipment for oil refining and separation, this series of products have the characteristics of high speed, stable operation, fully sealed import and export systems, low noise and good separation effect. The three-phase separator series is mainly used to separate fat oil from the mixture, it can concentrate and purify the oil derived from raw materials such as coconut oil, citrus oil, avocado oil, olive oil, soybean oil, sunflower oil and fruit seeds oil, sesame oil, canola oil, etc.
Dairy, beverage, juice and beer separating:
Disk centrifuge separators are also useful in producing dairy products such as skimmed milk, cream, and cheese. They can be used to separate the cream and fats from the milk, which is then used to produce butter or cream cheese. The separation process is essential in the production of cheese, as it enables the separation of the curds from the whey.
When producing tea drinks or coffee drinks, the disk stack separators are also used for separating the solids in tea drinks and coffee drinks.
Stack centrifuge separators are widely used in the juice production industry to separate the juice from the pulp, fiber, seeds, and other solids. The separation process is crucial for producing high-quality juice products that are clear, smooth, and free from impurities such as apple juice, citrus juice, pineapple juice, coconut water, etc.
In the production of beer, disk centrifuge separators can be used to separate the yeast from the beer, which is essential in controlling the fermentation process. The separator can also be used to clarify the beer by removing any sediment that may affect the flavor and appearance of the final product.
Plant and herb extraction and concentration:
Mechanical separation technology is one of the most critical parts in the separation, concentration and clarification process of Chinese herb and natural plant extraction. disk stack separators are used in pepper, Chinese medicine, tea and coffee production to extract valuable components such as pigments, oils, flavors, and aroma compounds, improving the overall quality and taste of the final product.
Starch Separation:
Disk centrifuge separators are commonly used in the starch industry for the separation of starch from other components, such as protein and fiber, in raw materials such as corn, wheat, and potatoes. The separation process involves the use of centrifugal force to separate the starch from the other components, resulting in a high-quality starch product with high purity and yield. Disk centrifuge separators are also used in the production of modified starches, which are used in various food and non-food applications. The use of disk centrifuge separators in the starch industry allows for more efficient production processes and increased yield, ultimately resulting in cost savings and higher profitability.
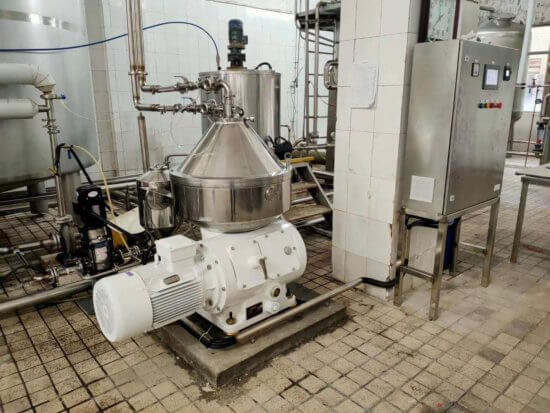
The Technical Parameter of Disk Centrifuge Separator
Model | Capacity(L/H) | Inlet Pressure (Mpa) | Outlet Pressure(Mpa) | Power(KW) | Weight(KG) | Size(mm) |
---|---|---|---|---|---|---|
DN 360 | 2000-5000 | 0.05 | 0.1-0.35 | 7.5 | 1200 | 1530*1150* 1500 |
DN 470 | 5000-10000 | 0.05 | 0.1-0.4 | 15 | 1600 | 1800*1200* 1750 |
DN 550 | 10000-20000 | 0.05 | 0.1-0.4 | 22 | 2300 | 1950*1550* 1960 |
DN 610 | 25000-35000 | 0.1 | 0.3 | 37 | 3000 | 2185*1728* 2082 |
DHN 204 | 1000-1500 | 0.05 | 0.1-0.2 | 4 | 520 | 810*850* 1350 |
DHN 360 | 1000-3000 | 0.05 | 0.1-0.3 | 7.5 | 1200 | 1530*1150* 1500 |
DHN 470 | 3000-7000 | 0.05 | 0.1-0.4 | 15 | 1600 | 1800*1200* 2030 |
DHN 550 | 5000-10000 | 0.05 | 0.1-0.4 | 22 | 2300 | 1950*1550* 1960 |