Project Description
Aseptic Tank SystemÂ
Aseptic Tank Application
The aseptic buffer tanks are mainly used for storage and buffering liquid food and beverage(milk and dairy, plant-based drinks, NFC juice, prepared food) to maintain the sterilized products under condition of total sterility, waiting for the aseptic filling. The tanks system can be integrated into a full aseptic line or used in a separate unit for receiving all ultra-high temperature sterilized liquid aseptic products to keep the product of high quality and reduce the loss of nutrients.
The tank is suitable for storing the products with high or low viscosity, with or without fibers, with smaller or bigger particles, and it can also be equipped with a special agitator(with aseptic barriers) to make sure the material is in homogeneity after a long time storage.
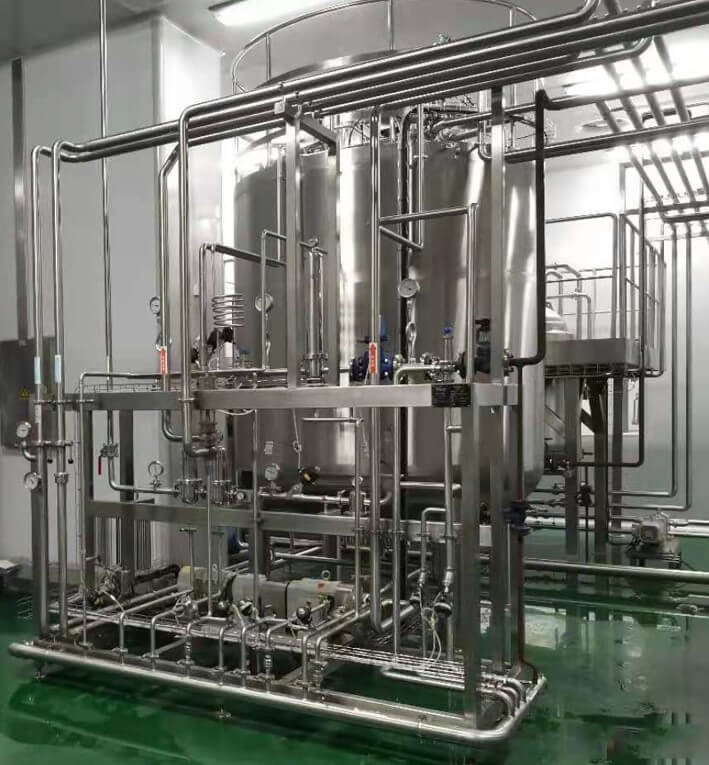
Aseptic Tank Advantage
Aseptic tank systems offer several advantages for liquid food and beverage products, including:
- Preservation of product quality: it is designed to sterilize and maintain the quality of the product. This helps to extend the shelf life of the product, without the need for refrigeration or other preservatives.
- Reduced risk of contamination: It uses a sterilization process that kills all bacteria and other microorganisms in the tank to ensure the products and tank are in an aseptic state. This reduces the risk of contamination and ensures that the product is safe for filling and consumption.
- Flexibility in production: Aseptic tank systems can be used for a wide range of liquid food and beverage products, including dairy products, juices, soups, sauces, and more. The system allows for precise control of processing conditions, such as temperature, pressure, and time, which can be adjusted to meet the specific needs of each product.
- Cost savings: It can help to reduce production costs by eliminating the need for refrigeration and other preservatives, as well as reducing the risk of product spoilage and waste. This can lead to significant savings in storage, transportation, and production costs.
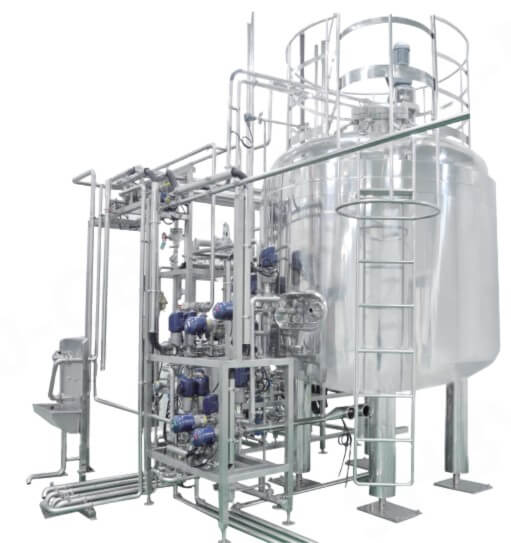
Aseptic Tank Feature
- Pre-assembled and factory tested for easy and quick installation based on standardized designs.
- Can be integrated with a UHT control system or filling machine to meet the needs of UHT by connecting multiple filling machines.
- Uninterrupted production during product change or equipment cleaning to avoid secondary sterilization caused by product backflow.
- The system is configured with a remote module, which can perform system maintenance in real-time;
- Failure to maintain the front and rear sections without downtime.
- Intelligent operation, simple operation and high safety.
- The aseptic tank can be equipped with an optional stirrer, which can stir products that are prone to sedimentation such as chocolate and juice fibers evenly, and can also balance the temperature of the product.
- Tank bodies, pipelines and valves can be designed with SUS316L material for high-acid juice or liquid food.
- Product cooling and insulation functions can be achieved on the shell and bottom.
- Use steam sterilization and condensed water to prevent recontamination during production
- An alternative agitator can be installed on the top of the tank and with the steam barrier.
- Integrated CIP and SIP system to make sure the tank is in high hygiene condition and aseptic state.
- The design pressure of the inner tank is 0.1 ~ 0.4MPa.
- Tank capacity is from 5,000L-40,000L/H, and material incoming flowrate is from 2,000L-20,000L/H.
- The aseptic tank has a hollow jacket with high-efficiency cooling and heat exchanging.
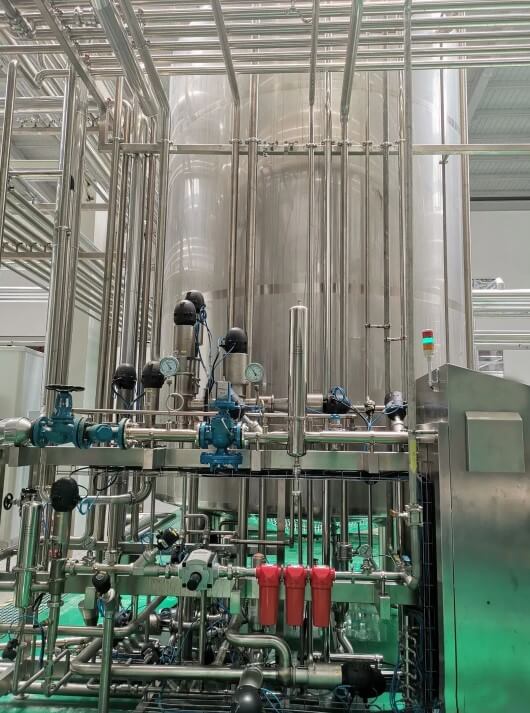
Aseptic Tank Purpose
The aseptic tanks system is most used when the following three situations occurred in aseptic processing line:
- Product buffering: If one of the packaging machines stops unexpectedly, the aseptic tank is used for buffer storage product during the shutdown.
- Product replacement: Two products are packed at the same time. First, one product is filled with aseptic tanks, which is enough to ensure the whole batch of packaging. Then, the UHT equipment switches to produce another product and packs it directly into the aseptic filling machine.
- Product reflow: The UHT system has a product balance tank between 300-500 liters, and the product reflow cycle can keep the filling pressure stable through the balance tank. But sensitive or over-handling products cannot use this return flow, and the flow pressure requirements of the filling machine must be provided by the aseptic tank.
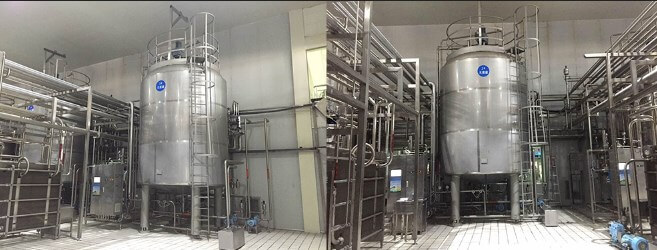
Aseptic Tank Composition and Work Principle
The aseptic tank system is composed of tank body, electronic control cabinet, sterile air pipeline system, clean steam pipeline system, tank instrumentation(angle seat valves, mix proof valves, sensors), agitators, etc.
The tank is sterilized by steam at a minimum temperature of 125°C for 30 minutes. It is then cooled by water circulating through the cooling jacket. During cooling, sterile air is fed into the tank to prevent vacuum formation. After sterilization, the aseptic tank is kept in aseptic conditions with an overpressure of sterile air and with steam barriers (110°C). During production, sterile air fills the tank space above the level of the product. The pressure is automatically controlled to maintain the feed pressure required by the filling machine in operation.
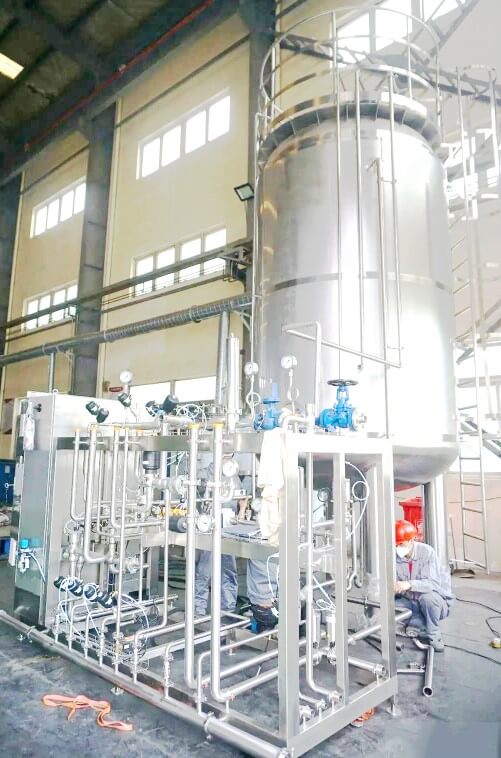
Technical Parameter
Model | Volume | Size | Power | Steam(SIP) | Cooling Water(SIP) | Compressed Air(SIP) | CIP Water Flowrate |
---|---|---|---|---|---|---|---|
BYCKL-5 | 5000L | Ï3800*3000mm | 2.1KW | 200KG/H | 2500L/H | 20M^3/H | 20,000L/H |
BYCKL-8 | 8000L | Ï3900*3800mm | 3.2KW | 270KG/H | 3000L/H | 27M^3/H | 20,000L/H |
BYCKL-10 | 10000L | Ï3900*4400mm | 3.2KW | 340KG/H | 4000L/H | 34M^3/H | 20,000L/H |
BYCKL-15 | 15000L | Ï4200*4900mm | 4KW | 525KG/H | 5500L/H | 50M^3/H | 20,000L/H |
BYCKL-20 | 20000L | Ï4300*5800mm | 5KW | 670KG/H | 6500L/H | 67M^3/H | 20,000L/H |
BYCKL-25 | 25000L | Ï4600*6100mm | 6.5KW | 850KG/H | 8500L/H | 85M^3/H | 20,000L/H |
BYCKL-30 | 30000L | Ï4700*6900mm | 8.5KW | 1000KG/H | 10000L/H | 100M^3/H | 20,000L/H |