Liquid Nitrogen Dosing System ApplicationĀ
In the food and beverage industry, liquid nitrogen dosing systems are commonly used to preserve the quality and freshness of products such as coffee, beer, wine, milk, snacks, water, fruit jam or sauce and juices. By injecting a small amount of liquid nitrogen into the container(metal cans or PET bottles)before it is sealed, the oxygen is displaced, preventing oxidation and microbial growth. This extends the shelf life of the product, maintaining its quality and flavor over time
The liquid nitrogen dosing machine has the following benefits used in the liquid food and beverage field:
- Light weighting of PET Bottles – Reduces the weight of PET bottles, saving costs and promoting environmental protection.
- Extended Shelf Life – Oxygen content is reduced to a lower level, resulting in longer shelf life.
- Replacing Glass with Plastic Packaging – Eliminates the health hazards and weight associated with glass bottles.
- Easy Labeling – Consistent bottle hardness improves labeling efficiency.
- Bottle Durability – Maintains the original shape of lightweight bottles.
- Elimination of Deflated Bottles/Cans – Increases bottle pressure to eliminate flatness issues.
- Low Oxygen Function – Inert gas packaging helps maintain product freshness.
- Preservation of Organic Product Quality – No need for preservatives to extend shelf life.
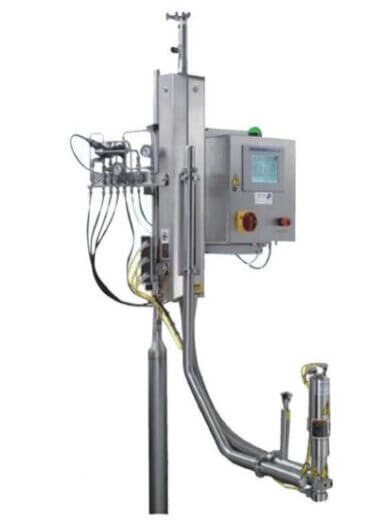
Liquid Nitrogen Dosing Machine Introduction
In the food and beverage industry, achieving a vacuum in packaging containers can be challenging. Connecting the vacuum chamber of the can seamer to the vacuum pump or steam injection are the common methods used, but they have some limitations. Vacuum pumping has a slower production speed, while the vacuum formed by steam injection requires hot filling. To reduce costs, save energy, and improve convenience, nowadays tinplate cans are being replaced by pop-top aluminum cans and plastic bottles/cans. However, these materials cannot be vacuumed and need internal pressure to prevent deformation. So it can only be filled with liquid nitrogen. As the liquid nitrogen vaporizes in containers, it creates a vacuum and increases the internal pressure in cans or bottles, maintaining the container’s shape and extending the shelf life of the product.
The liquid nitrogen filling machine can be directly connected to the vacuum insulation pipeline, and the liquid nitrogen dosing machine can provide a complete liquid nitrogen supply system from the liquid nitrogen storage tank to the dosing line. The compact shape and simple installation are suitable for all kinds of filling lines, and they can match the speed and application of any line.
After the container is filled and before it is sealed, the modern liquid nitrogen dosing technology is used to accurately dose liquid nitrogen at -196°C, and then the seal is immediately sealed. The liquid nitrogen absorbs heat in a short time, and the volume expands by 700 times into nitrogen gas.
The liquid nitrogen dosing machine can accurately control the amount of liquid nitrogen, with the function of no container feeding, and no dosing. It is equipped with programmable logic controller (PLC) and has a compact design that can be easily installed on any filling line. All pipelines are insulated with vacuum liquid nitrogen pipes to minimize liquid nitrogen consumption.
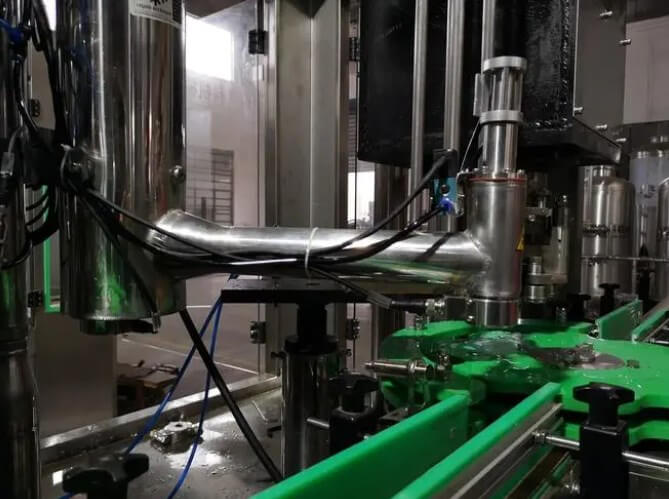
Liquid Nitrogen Dosing Machine Feature
- Positive Pressure Nitrogen Protection – The nozzle is protected by dry positive pressure nitrogen to prevent frost and ice blockage caused by external air entering the inside of the nozzle.
- Differential Pressure Level Gauge – High accuracy liquid level measurement with gas-liquid separation function to achieve pressure-free dosing.
- Precise Nitrogen Dosing – Provides stable and accurate nitrogen dosing.
- Individual or Continuous Dosing – The speed of switching between dosing modes can be set by the user.
- Vacuum Insulation Technology – Improves the efficiency of liquid nitrogen usage.
- Compatible with Soft Dosing – Suitable for hot filling and cold filling cans or bottles, juice, beverage, jam powder, and granular products.
- Micro-Dosing Technology – Maintains consistency and accuracy of nitrogen dosing on all production lines.
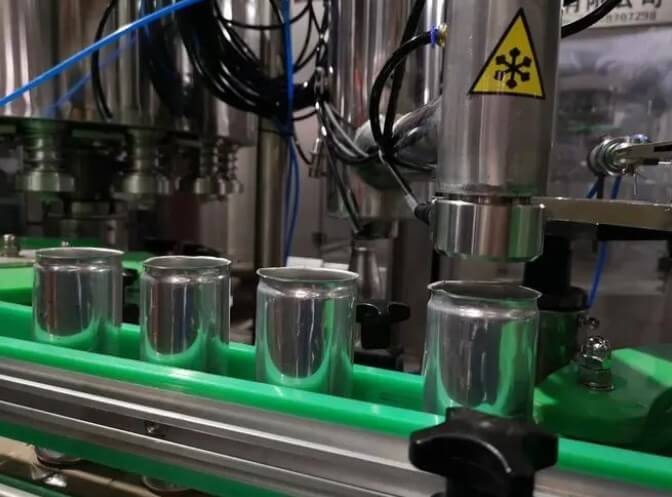
Liquid Nitrogen Dosing System Composition
A Liquid Nitrogen Dosing Machine typically consists of several components, including:
—Nitrogen supply source:Ā This is the source of liquid nitrogen, which is typically stored in a large tank or supplied through a pipeline.
—Nitrogen dosing unit: This unit is responsible for measuring and dispensing the liquid nitrogen accurately. It typically includes a dosing nozzle, a dosing valve, and a dosing pump.
—Control system: This system is responsible for controlling and regulating the dosing process. It typically includes a PLC (Programmable Logic Controller) and a touchscreen interface for operators to input dosing parameters.
—Insulated delivery hose: This hose is used to transfer liquid nitrogen from the dosing unit to the dosing nozzle while keeping it at a low temperature.
—Nitrogen vapor recovery system: This system is responsible for collecting and recovering any excess nitrogen vapor that is released during the dosing process.
—Safety features: Liquid Nitrogen Dosing Machines typically include several safety features, such as pressure relief valves, vacuum breakers, and emergency stop buttons, to ensure safe operation.
Ā
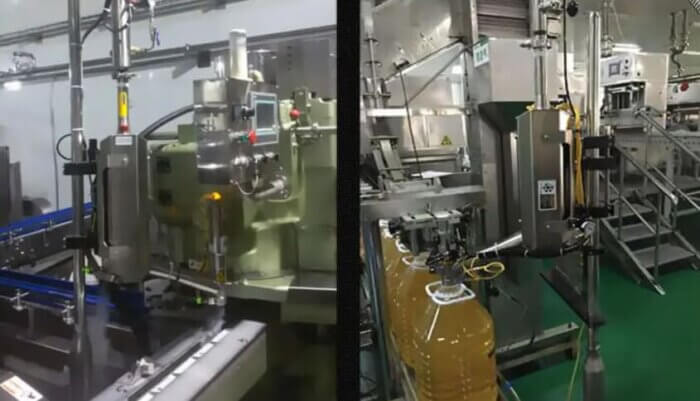
Technical ParameterĀ
Technical Parameter | Value |
---|---|
Material | SUS304 |
Overall Size | 700mm*159mm |
Dosing Nozzle Size | 270mm*51mm |
Supply Facility | liquid nitrogenļ¼0.15Mpa; Nitrogen: 0.5-0.65Mpa; 220V/50HZ/100W |
Liquid Nitrogen Evaporation Loss | 0.15L/H |
Dosing Capacity | 0-200 bottles/min |
Dosing Precision | ±5% |