Aseptic filling: It is relative to hot filling, usually refers to normal temperature filling, also called cold aseptic filling PET (CAFPET) technology. Aseptic cold filling technology was born in the 1920s. In 1961, Tetra Pak first used this technology in commercial production. The PET aseptic filling production line also uses aseptic space plus chemical disinfectants to sterilize to ensure that the entire production process meets the aseptic requirements.
This article will explain the difference between PET bottle hot filling and aseptic filling technology:
The Difference Between Aseptic Cold Filling and Hot Filling
I. Different filling technological process
Hot filling temperature is 89℃, After filling, the bottled juice need to go through the tilt bottle conveyor for cap sterilizing and juice pasteurizer cooling tunnel for secondary pasteurizing. Bottles and caps no need aseptic treatment. Filling environment no need aseptic.
Cold aseptic filling temperature is 30℃, Bottles and caps need to sterilize to ensure aseptic, Fruit juice can be packed into carton packages after filling, no need to do secondary sterilizing.
II. Sterilizing technological process
Hot filling: The hot filling juice can be used with pasteurizer, the heating temperature is about 95-120℃ holding for 15S-30MIN, then cooled to 89℃for filling, When the filling machine is in downtime, the juice will be returned to pasteurizer for re-sterilization. And the juice color, flavor and nutrition have a certain influence.
Aseptic cold filling: The juice uses UHT sterilization technology, then quickly cooled down to room temperature, and stored in an aseptic tank for filling at any time.
III. Packaging container
Hot filling: PET bottles need to be able to withstand temperatures of at least 92°C, so the walls of the bottles should be thick with ribs to prevent thermal shrinkage of the bottles. The mouth of the bottle needs to be crystallized to ensure that the mouth not deform during filling and capping.
Cold aseptic filling: The maximum heat-resistant temperature is 60℃, and the PET bottles can be light-weight bottles and ordinary caps, which greatly reduces the cost of bottles and caps.
Item | Hot Filling | Cold Aseptic Filling |
---|---|---|
Bottle weight | 28g-32g/500ml | 18g-23g/500ml |
Bottle neck | Special crystal bottle neck | Standard bottle neck |
Material stretch rate | High requirements | Standard |
Bearing temperature | 85-92℃ | 60℃ |
Oxygen permeability | Low | High |
Bottle caps | Heat-resistant | Standard |
Bottles and caps cost | High | Low |
Features of Aseptic Filling Line
I. Product safety guarantee
Material sterilization: UHT ultra-high temperature instantaneous sterilization, short heating time, less loss of nutrients, and no obvious changes in quality and taste.
Empty bottle sterilization: Empty bottles made from blowing bottle machine through air conveyor transported to filling station, the inside of the bottles will be sterilized by H2O2, the bottle surface will be sterilized by disinfectant. After the sterilization is completed, rinse the residual disinfectant in the bottle with sterile water, and then blow dry with sterile air to ensure that the residual disinfectant will not affect the material.
Bottle caps sterilization: Use disinfectant immersion sterilization. After the sterilization is completed, rinse the residual disinfectant in the caps with sterile water and blow dry with sterile air.
Maintenance of aseptic environment: Adopting purification room isolation measures, the filling machine area is a hundred-level purification room, and the air filtration system in the purification room can ensure the cleanliness of the air in the filling environment, so that the materials will not be polluted by microorganisms suspended in the air.
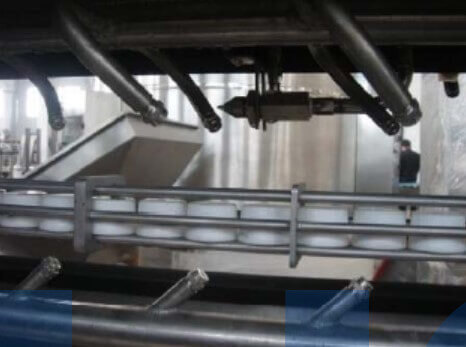
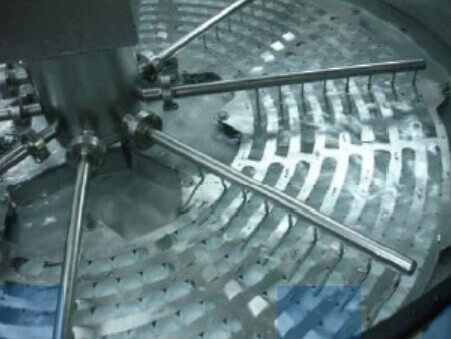
II. Sterility assurance of the main equipment of the production line
Pipeline and valve technology, material surface polishing, surface design of important areas, selection of anti-corrosion materials, etc. are designed and selected in accordance with strict sanitary requirements.
With a complete automatic cleaning system(CIP System), sterilization system(SIP system), equipment external foam cleaning(COP system) and sterilization system(SOP system)
The filling valve adopts to aseptic SUS316L material controlled by flowmeters.
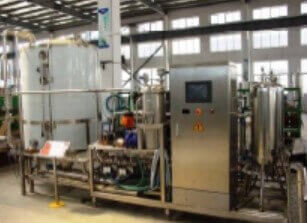
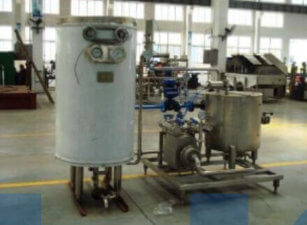