A jacketed tank is a specialized vessel used in industries such as pharmaceuticals, food processing, and chemicals for heating or cooling liquid or semi-solids efficiently. These tanks feature an outer shell or “jacket” that allows the circulation of heating or cooling media, such as steam, water, oil, or refrigerants, to regulate the internal temperature of the stored or processed material without direct contact between the medium and the product.
In the food and beverage field, in order to meet specific technological process requirements, the materials need to be heated or cooled. The jacketed tank is designed for heating or cooling materials through the jacket.
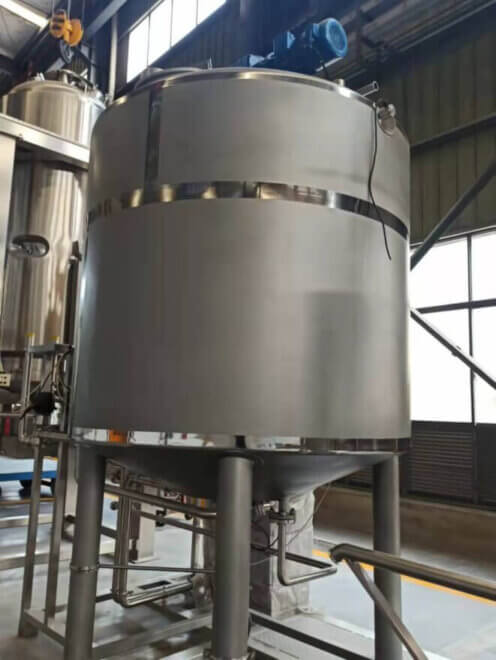
Configuration
The whole body is made of SUS304, and inner layer material contact parts can be made of SUS316L. It usually has three layers: the inner layer is 3-4mm, the jacket layer is 0.8-2.5mm, and the out layer is 2-3mm. The transition section of the inner wall of the tank adopts an arc transition to ensure that there is no sanitary dead corner. The standard configuration of the jacketed tank includes:
- tank body
- Material inlet and outlet
- cooling or heating medium inlet and outlet
- airtight manhole
- Anti-butterfly air vent
- digital thermometer
- liquid level indicator
- discharge valve
- CIP cleaning ball
- ladder
- agitator(paddle, frame, propeller, scrape type)
- reducer
- adjustable legs
- sample valve
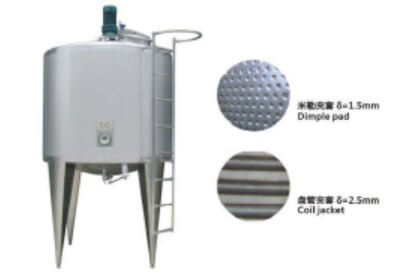
Application
Fruit juice or milk heating or cooling, ingredients mixing, ice cream aging, food and beverage blending, batch sterilizing, cream storage, juice, wine or yogurt fermentation.
- Liquid food and beverage heating and cooling: Jacketed tanks are often used for precise temperature control in processes such as pasteurization, cooking, cooling, and fermentation in juice, puree, sauce and dairy production. The jacketed design allows for the circulation of hot or cold fluids (steam, hot water, or chilled water) around the tank jacket, ensuring that the product inside is heated or cooled uniformly.
- Mixing and Blending: It can also be used for mixing and blending food and beverage products. The jacket can help maintain the desired temperature during mixing, ensuring consistent product quality.
- Storage: Stainless steel jacketed tanks are suitable for storing ingredients, intermediate products, or finished products in a temperature-controlled environment. This is essential for items like fruit juice, chocolate, sauces, and dairy products.
- Fermentation: In the production of certain beverages, such as beer and wine or yogurt, jacketed tanks can be used for fermentation. The temperature control offered by the jacket helps maintain the optimal conditions for the growth of yeast and other microorganisms.
- Chilling and Cooling: For products like fruit juices and concentrates, milk and dairy products, it’s essential to rapidly cool them after processing. Jacketed tanks are used to chill products quickly and efficiently.
- Chocolate Tempering: In chocolate production, jacketed tanks are employed to precisely control the temperature of the chocolate during the tempering process. This ensures that the chocolate has a glossy appearance and a smooth texture.
- Sauces and Soups: In the preparation of various sauces and soups, jacketed tanks are used to cook and heat the ingredients while maintaining even temperatures.
- Pasta Production: In pasta production, jacketed tanks can be used for cooking and cooling pasta products, helping to achieve the desired texture and consistency.
- Dairy Processing: Dairy products such as yogurt and cheese require precise temperature control during various stages of production. Jacketed tanks can be used for pasteurization, fermentation, and cooling in dairy processing.
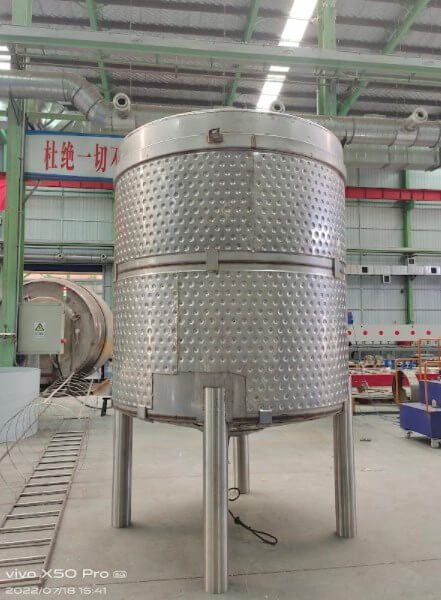
Jacketed Tank Type
Heating or Cooling Medium
Steam heating: The jacketed tank will add one more steam valve control system(steam stop valve, pressure reducing valve, safety valve, pressure gauge, etc.). Saturated Vapor will directly inlet into the jacket layer and heat exchange with material. This type of heating is suitable for high heating temperature, low heat sensitivity material.
Electronic heating: One heater will be mounted on the top of bottom of the tank jacket, then the water is passed into the jacket and heated by the electronic heater, the hot water will make heat exchange with material. This type of heating method is suitable for low-temperature heating and heat sensitive materials.
Thermal oil heating: The heat transfer oil circulating heating jacketed tank needs to be equipped with a heat transfer oil boiler to heat the heat transfer medium (heat transfer oil) to a certain temperature, and then use the pump body to transport it to the jacket of the jacketed tank for circulating heating. Because this heating method heats the material unevenly, it uses less.
Chill water cooling: The jacketed tank can also pass into chill water to cool down the material. It needs to equip one more water chiller to supply chill water to the tank. It is usually used for cooling down the milk in batch tanks.
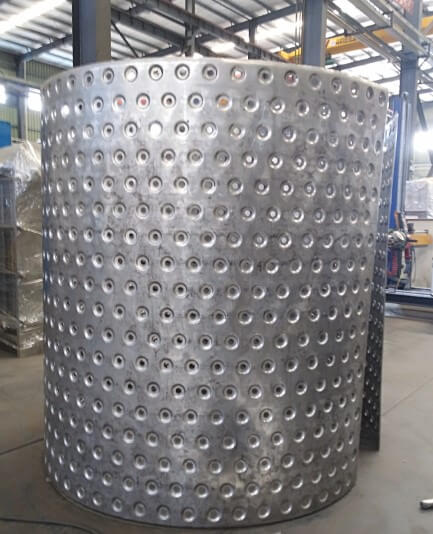
Jacket Structure
Dimple jacket: The jacket has 0.8-1.5mm dimple pad with PU insulation; heating or cooling medium will flow onto the dimple pad to do heat exchange with the material. The dimple jacketed tank is suitable for feeding hot water or chill water to heat or cool materials in the tank with low heat transfer efficiency.
Half pipe coil type jacket: The jacket layer is 2.5mm coil pipes with rock wool insulation; steam will do heat exchange in the coil pipes. Heat exchange efficiency is higher than the dimple jacket.
Plain-type jacket: The hollow jacketed tank has the highest heat exchange efficiency and high cost. It is generally used for heat-sensitive materials that require rapid heating or cooling.
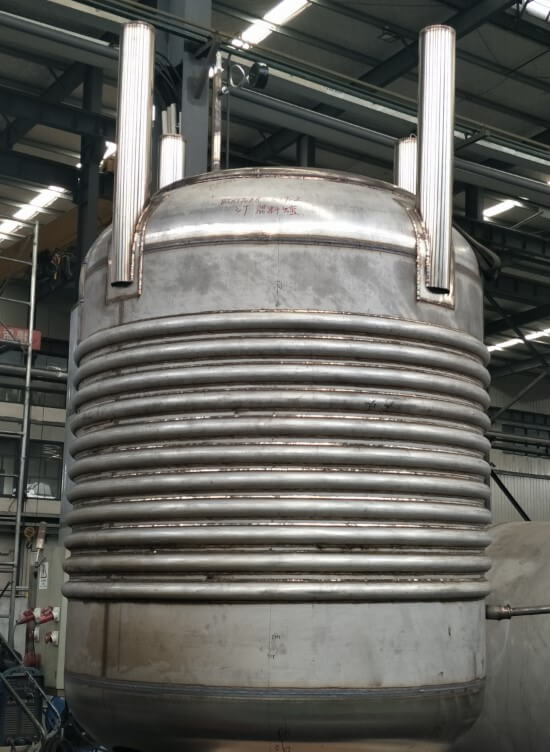
Technical Parameter
Model | Volume | Size(D*H) | Diameter of Inlet&Outlet |
---|---|---|---|
BDG-500 | 500L | φ800*H2140mm | φ38/φ51mm |
BDG-1000 | 1000L | φ1050*H2380mm | φ38/φ51mm |
BDG-1500 | 1500L | φ1180*H2550mm | φ38/φ51mm |
BDG-2000 | 2000L | φ1340*H2760mm | φ38/φ51mm |
BDG-3000 | 3000L | φ1540*H3050mm | φ38/φ51mm |
BDG-4000 | 4000L | φ1650*H3200mm | φ38/φ51mm |
BDG-4000 | 4000L | φ1650*H3200mm | φ38/φ51mm |
BDG-5000 | 5000L | φ1780*H3250mm | φ38/φ51mm |
BDG-6000 | 6000L | φ1900*H3350mm | φ38/φ51mm |
BDG-8000 | 8000L | φ2060*H3800mm | φ65/φ51mm |
BDG-10000 | 10000L | φ2300*H4050mm | φ65/φ51mm |
BDG-12000 | 12000L | φ2520*H4450mm | φ65/φ51mm |
BDG-15000 | 15000L | φ2540*H4700mm | φ65/φ51mm |