High Shear Pump Working Principle
The high-shear emulsification pump is also called a tubular emulsifier or a continuous emulsifier. Its working principle is the same as that of an emulsifying tank. Under the combined action of centrifugal extrusion, friction, and collision in the narrow space between the rotor and the stator, the material is evenly distributed to each other, and a suitable emulsifier is added to achieve instant uniform emulsification of the two substances that are originally incompatible, so as to obtain a stable product.
The high shear emulsification pump is a high-performance equipment used for continuous production or circulating processing of fine materials. In the narrow space of the emulsification pump, there are 1-3 sets of multi-layer stators and rotors with dual engagement. Driven by the motor, it rotates at high speed to produce strong axial suction to suck the material into the cavity.
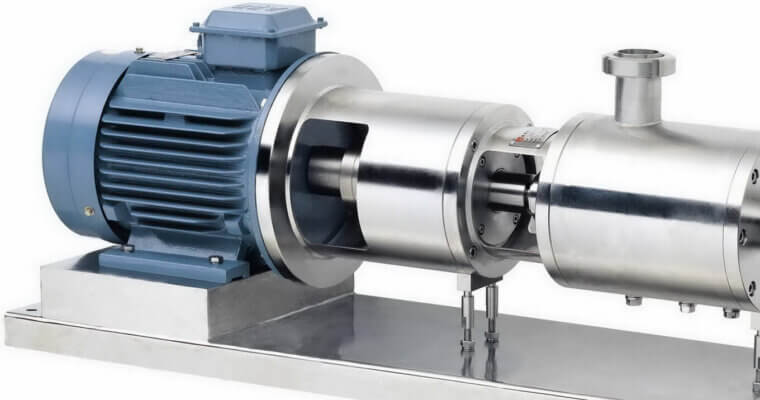
High Shear Pump Application
The high-shear emulsification pump is a kind of equipment that can fully refine and uniform the material. It is mainly used for liquid-liquid emulsification and homogenization, liquid-solid emulsification and dispersion. The high-shear emulsification pump has the functions of refinement, dispersion and homogenization. In the food and beverage field, it can be used for dispersing and dissolving vegetable soups, seasonings, stabilizers, and homogenizing emulsification of dairy products (cheese), jams (mayonnaise, ketchup), fruit juices, and flavoring agents.
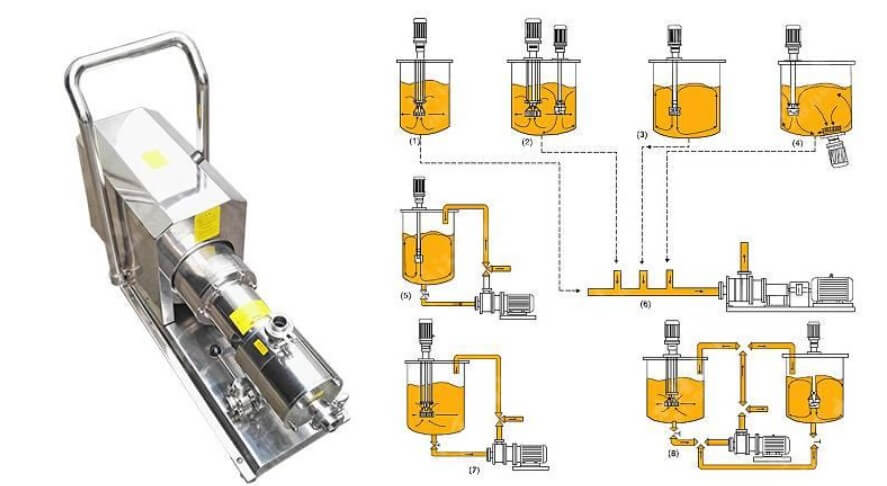
High Shear Pump Feature
-A high-shear emulsification pump, also known as a centrifugal homogenizer, is suitable for the previous process of materials.
–It has a feature of high efficiency, low energy consumption, time-saving, and labor-saving, suitable for industrial continuous production.
–There is no dead corner, and the material is 100% sheared through dispersion. The particle size distribution range is narrow, and the uniformity is high; the disassembly and assembly are simple and easy to clean, which can meet the needs of CIP cleaning in different occasions.
–It has a certain self-suction and low-lift conveying function; the production process can realize automatic control; it can be equipped with a cooling system without external cooling water. Under normal circumstances, the emulsification pump can withstand a high temperature of 80°C, but a cold water system can be added to withstand a high temperature of 150°C.
–The pump shaft is supported by a bearing box, and the working chamber can be selected as a 1-stage, 2-stage, or 3-stage combination. At the same time, the clearance and size of each stator and rotor can be designed and adjusted according to actual conditions to meet the working conditions and energy consumption requirements of different customers.
–The mechanical seal adopts a double-end face structure and is equipped with cooling water. Different mechanical seal flushing solutions can be configured separately in combination with special working conditions.
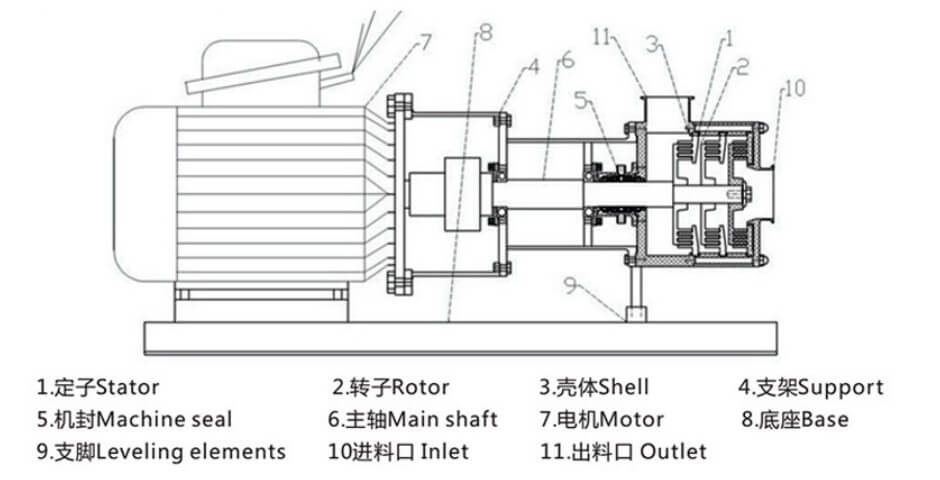
High Shear Pump FAQ
The difference between emulsifying machine and emulsifying pump:
The emulsifier is an input device (inserted into the tank), and the emulsification pump is a pipeline device (through a pipeline). The emulsifier also has a certain stirring function. The emulsification pump has a certain lift and can be transported in a short distance.
The difference between single-stage emulsification pump and three-stage emulsification pump
The main difference is emulsification fineness. The three-stage emulsification pump has three sets of stators and rotors, which are divided into coarse teeth, middle teeth and fine teeth, and there is only one set of single-stage emulsification pumps.
–Coarse teeth, impact, crushing, shearing, dissolving, coarse dispersion
–Middle teeth, disperse, refine, accelerate dissolution, emulsify
–Fine teeth, ultra-fine dispersion, enhanced emulsification, homogenization, and pulping
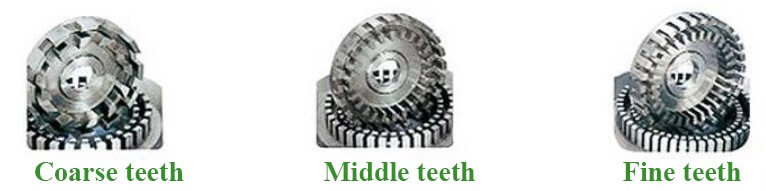
Technical ParameterÂ
Model | Power | Rotor Speed | Flowrate |
---|---|---|---|
BLR3-60 | <4KW | 1450-2950RPM | 0-4T/H |
BRL3-100 | <7.5KW | 1450-2950RPM | 0-12T/H |
BRL3-120 | <11KW | 1450-2950RPM | 0-12T/H |
BRL3-140 | <15KW | 1450-2950RPM | 0-18T/H |
BRL3-165 | <22KW | 1450-2950RPM | 0-22T/H |
BRL3-200 | <37KW | 1450-2950RPM | 0-30T/H |
BRL3-220 | <55KW | 1450-2950RPM | 0-40T/H |
BRL3-240 | <75KW | 1450-2950RPM | 0-55T/H |