PET Bottle Aseptic Filling Line Description
The PET aseptic filling line has the advantage of long product shelf life, keeping original flavor and nutrient of the products, saving packing material cost compared to PET hot filling system. It is especially suitable for producing high-quality NFC juice, plant-based milk, cereal drinks, etc.
The PET aseptic filling line is based on PET bottle packaging technology, starting from the microbial stability of the filled materials, it is a comprehensive application of filling technology, sterilization technology, and microbial control technology.
PET aseptic filling is to sterilize the material, sterilize the bottle and the cap separately to make them aseptic, and then fill aseptic material into the aseptic bottles and cap with aseptic caps in an aseptic environment. The sterility here is commercial sterility.
The aseptic bottle filling system can meet the filling of neutral products but also meet the multi-content compatible filling materials.
The filling uses non-contact electronic valves instead of mechanical valves to ensure that materials will not be polluted during the filling process.
The Capacity for the PET aseptic filling line is from 12000BPH-48000BPH, the filling temperature is 25℃-35℃. Applicable various shape bottles like round bottles and square bottles.
The key to PET aseptic filling production technology is to ensure filling, and the microorganisms inside the beverage after capping are controlled within the allowable range to achieve commercial sterility.
Using the new aseptic maintenance technology, the continuous production cycle of neutral products is ≥72 hours, and the continuous production cycle of high-acid products is ≥120 hours, and there is no need for any short-term sterilization in the middle.
The “mirror-level” stainless steel machine table is clean, and the residual pollutants are reduced to the minimum.
Compatible with the production of non-aerated products containing 3*3*3mm fruit particles/pulp.
The 100-level air filtration system of the filling machine adopts double-layer U15 sterile filters. Even if one layer of high-efficiency filter is damaged, it will not cause damage to the sterile environment. At the same time, a pressure difference alarm device is added to effectively monitor high-efficiency filtration. It reminds the operator to replace it in time, and at the same time, it also has the function of reminding and monitoring the reasonable flow of wind direction inside the equipment.
The new sealing technology ensures that the service life of the liquid inlet distributor is ≥6000 hours.
The PET bottle aseptic filling line is composed of the following system and machine:
- Material Sterilization System
- Bottle and cap sterilizer
- Aseptic rinsing, filling, capping systems
- Cap sorting and feeding system
- Automatic CIP, SIP system
- Disinfectant Dispensing and Recovery System
- Sterile water preparation system
- Class 100 cleanroom air purification system
- Steam Purification System
- Sterile compressed air system
- Exhaust gas treatment system
- Fully automatic SOP, COP system
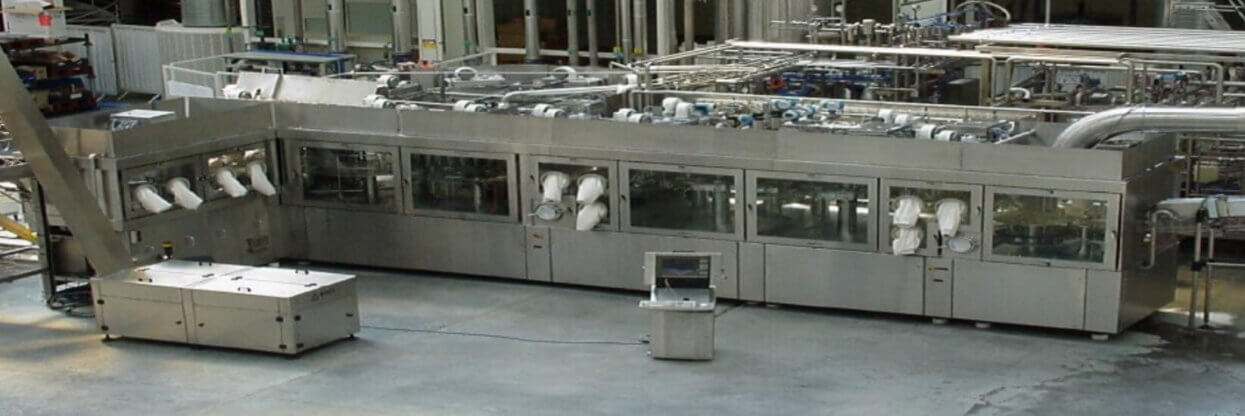
PET Bottle Aseptic Filling Line ClassificationÂ
PH value of materials: high-acid products PH≤4.5, low-acid products: PH>4.5, neutral product PH =6-7.
Material content: fruit juice, milk, yogurt, vegetable protein beverages, carbonated beverages, cereal beverages, tea beverages, coffee beverages, functional beverages, etc.
The viscosity of the material: the low viscosity value is juice, the high viscosity value contains fiber, and the pulp contains fruit particles.
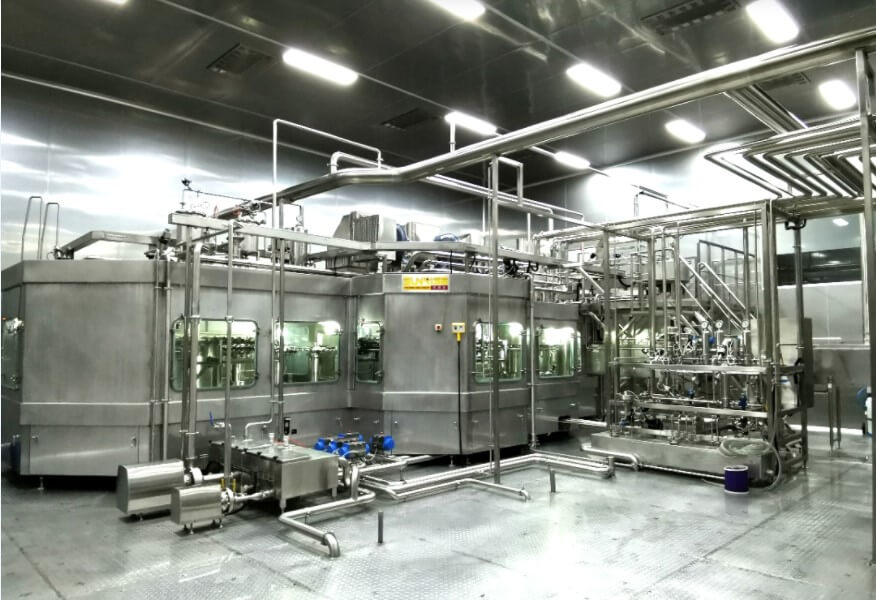
PET Bottle Aseptic Filling Line Process RequirementsÂ
To meet the conditions of the PET aseptic filling line, the following process requirements must be met: aseptic material, the establishment of an aseptic environment, maintenance of a sterile environment, empty bottles and caps are sterile, sterile water treatment.
Aseptic material
UHT sterilization and aseptic tank storage, aseptic maintenance period ≥ 120 hours. The feed liquid material is sterilized at 135-137℃ for 3-5S to make the feed liquid reach a commercial sterile state. Removal of microorganisms on the surface of equipment and pipes to achieve a sterile state.
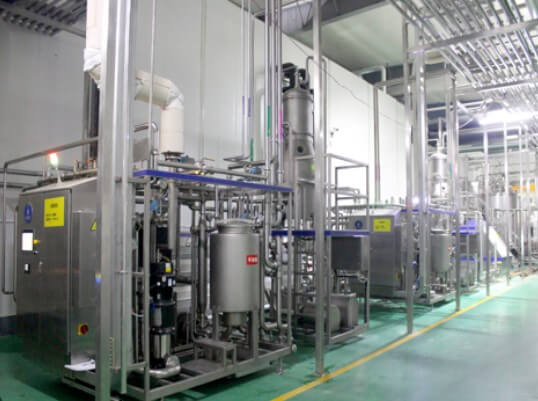
The establishment of aseptic environment
Filling area establishing a sterile environment through standard COP, CIP, SOP, SIP systems.
SIP system: The temperature of superheated water or steam sterilization is 121℃-135℃, and the time is 30min. There should be no leakage of steam or condensed water.
SOP system: Ensure that the sterile area is dry, clean and relatively airtight, and control the concentration, temperature and sterilization time of DES or PAA.
CIP system: After the production is completed, it is necessary to thoroughly clean the interior of the equipment and the pipeline with acid-base cleaning solution, hot water and sterile water to ensure the sterile state.
COP system: COP systems are used to clean pieces of equipment that wouldn’t be touched by the CIP system. Equipment could include fittings, clamps, product handling utensils, tank vents, pump rotors, impellers, casings, hoses, etc.
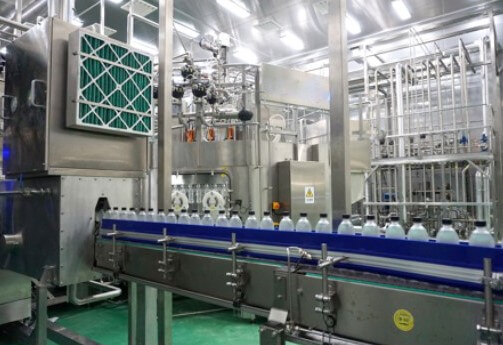
Maintenance of a sterile environment
Aseptic air system: During production, sterile air is always blown into the sterile area, and the sterile air is filtered by HEPA filter.
100 level cleaning room: The main filling machine area is required to reach 100-level cleanliness, and there is a 10,000-level purification room outside. The cleanliness of the air in the filling environment is ensured through the purification room, and the temperature and humidity of the purification room are controlled at the same time. In the 100 level cleaning room, the maximum allowable number of dust particles per cubic meter (greater than or equal to 0.5μm) is 3500, and the number of planktonic bacteria is 5.
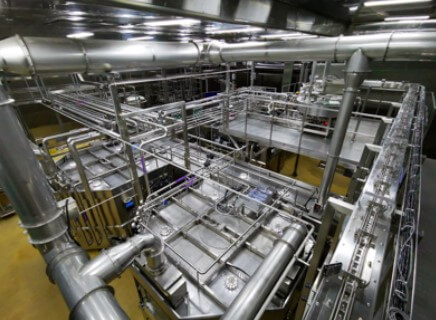
Empty bottles and caps are sterile
Through PAA wet sterilization or dry H2O2 sterilization, the packaging material(bottles and caps) is sterile.
- Immersion sterilization for bottles and caps: used for off-site blowing bottles, which can have an ideal effect on bottles with serious pollution, and low-temperature disinfectant reduces the consumption of disinfectant.
- Rinse-type sterilization for bottles and Caps: This type of production line has higher requirements for bottles than the immersion type. It adopts on-site blowing of bottles, and the blowing machine is connected to the filling machine through clean air delivery, or a blow-fill-rotator integrated machine is used to achieve high-efficiency production. Rinse the bottle and the caps with 2 channels of H2O2 disinfectant, and then rinse off the residual disinfectant inside the bottle with sterile water, then use the aseptic air to blow off the water in the bottles.
- H2O2 dry sterilization: sterilize bottles and caps by vaporizing H2O2 spray flushing, and blow-dry with sterile hot air, the production process does not need to rinse the bottles with sterile water, saving energy, reducing costs, and start-up time is short, dry sterilization adopts blowing, filling and rotating integrated machine, which occupies a small area.  Bottle sterilization: Using a unique mechanism to spray hydrogen peroxide vapor into the bottle with high-temperature sterile air, moving the nozzle can smoothly insert the bottle mouth into the bottle, making the gas flow easier to cover the inner wall of the bottle. The unique cup cover design can effectively sterilize the bottle mouth. Bottle drying: Use sterile hot air to blow into the bottle to vaporize and decompose the residual hydrogen peroxide on the inner and outer walls of the bottle, so that the residual amount is less than 0.5ppm.
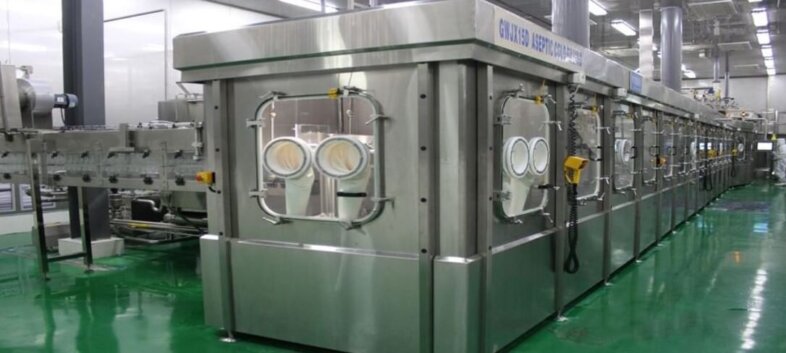
Sterile water treatment
The water was sterilized at 130°C for 30S by a UHT sterilizer. The sterile water is mainly used for washing bottles and caps.
PET Bottle Aseptic Filling Line Technological Flowchart
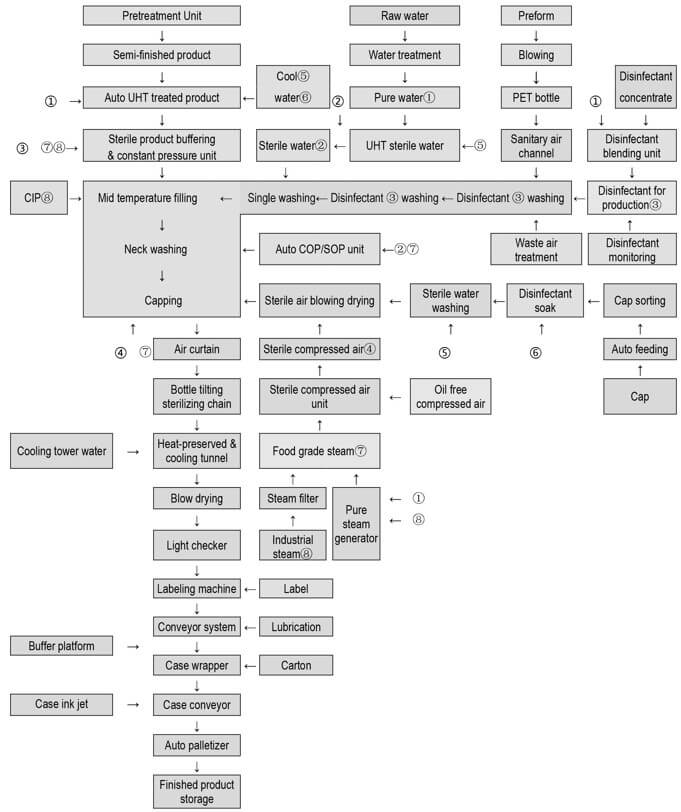