Project Description
Falling Film Type Evaporator
Equipment Application Field:
The falling film evaporator is a key process equipment in liquid food and beverage processing plant, it is mainly used for the below two fields:
Fruit and vegetable juice processing field: It is suitable for making low viscosity heat-sensitive concentrated fruit juice like apple, orange, pineapple, pomegranate juice, coconut water, grape juice, guava and passion fruit juice, etc.
Milk and dairy field: Used for the concentration of milk and the production of condensed milk. These evaporators allow for the removal of water from milk, leading to increased solids content and the creation of condensed milk.
Sugar syrup production: used in the production of sugar syrups from sugar beet or sugar cane juice. The evaporators help concentrate the sugar solution by removing water, resulting in a thicker syrup that can be used in various food and beverage applications.
Other liquid food and beverage processing fields: It can be also used for coffee extract, tea extract, plant extract, glucose, starch, xylose concentrating and evaporating.
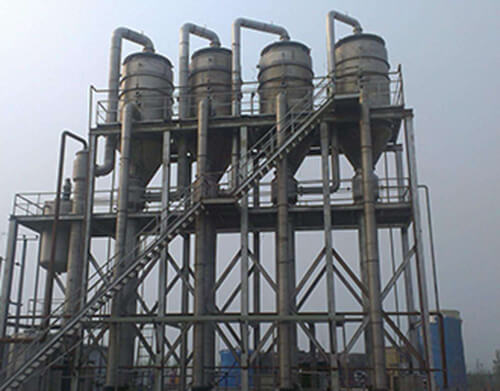
Machine Structure:
1. This falling film evaporator is mainly composed of the vertical type tubular or plate heater, liquid-vapor separator, condenser, vacuum system, vertical type tubular or plate cooling system, material transfer pump, condensate drainage pump, operating platform, control and monitor system(used for monitoring various parameters such as temperature, flow rates, and pressure to ensure efficient and safe operation), electrical instrumentation control cabinet and valves, pipelines and other systems.
2. All parts of falling film evaporator equipment that are in contact with materials, steam, secondary steam, and condensed water are all SUS304 or SUS316L.
3. The evaporator can be made into one effect, double effect and triple effect or multi-effect according to clients’ customized requirements.
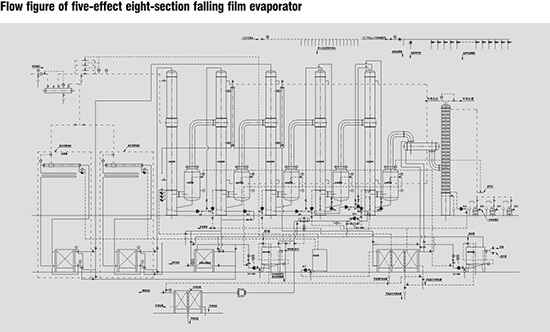
Working principle:
The raw fruit juice is feeding on the top of the evaporator and evenly distributed through the distributor to the inner wall of the heating tube. Under the gravity, it forms film shape and falls down along with the tube wall. During the descent, it is heated by the heating tube and continuously evaporates, the concentrated juice and steam generated during evaporating processing enter the gas-liquid separation chamber from the bottom of the heating chamber, and they will be separated into secondary steam and concentrated juice. Secondary steam is discharged from the top and the concentrated juice is discharged from the bottom.
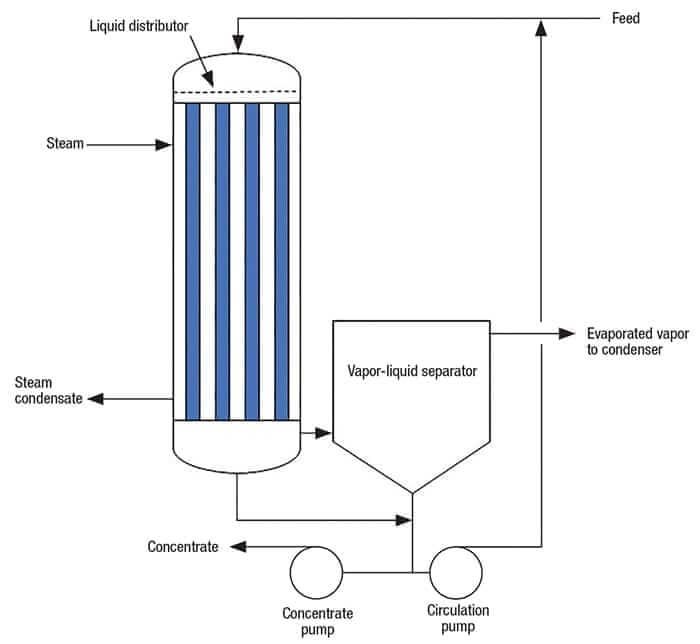
Advantages of Falling Film Evaporator:
(1) The material passes through one time, and the heating time is short, which can prevent thermal decomposition.
(2) Continuous operation, high effective time utilization rate of the equipment.
(3) Both evaporation and preheating are carried out under a small temperature difference, so it is not easy to coke, and also suitable for secondary steam recompression and multi-effect process operation.
(4) Due to multi-effect operation and secondary steam recompression, heat energy consumption is small.
(5) Low cooling water consumption.
(6) High heat transfer coefficient and good heat transfer performance.
(7) Can be used for materials with higher solid content and viscosity.
(8) High automatic and continuous: Automatic control of preheating temperature; Automatic evaporation temperature control; Automatic control of discharge level of concentrated juice; Automatic control of brix value of concentrated juice; Equipment CIP cleaning automatic control; automatic condensate level control; Automatic control of material feed flow.
(9) Because the material is evaporated into a film in each tube, the heating time of the material liquid is very short, so it is particularly beneficial to the evaporation and concentration of food, and the nutrient content of the food is greatly preserved.
(10) All the control systems use imported famous brand, such as steam group use Spirax Sarco brand. Touchscreen and PLC use the German SIEMENS brand. The electromagnetic valve uses the Japan Koganei brand. Frequency transducer uses DANFOSS brand. Low-voltage appliances use the Schneider brand.
(11) Aroma recovery system can be added into the evaporator when producing apple or orange concentrated juice processing line.
(12)hygienic design – Clean-in-Place (CIP)-compatible with automatic sequences.
(13)It takes a lot of energy to vaporize water from a solution. This energy is provided in the form of steam. In order to reduce the consumption of steam, the evaporator is usually designed to be multi-effect: two or more units operate under in the lower pressure to obtain a lower boiling point, in which case the steam produced in the previous effect is used as the heating medium for the next effect. In this way, the required amount of steam is approximately equal to the total amount of volatilized water divided by the effective number, thereby greatly saving steam energy consumption.
(14) The falling film evaporator can be divided into tubular-type falling film evaporator and plate-type falling film evaporator according to the different heat exchangers, the materials distributed in the heating chamber were evenly dispersed. Compared with other evaporators, the plate evaporator has a great advantage for the concentration of some heat-sensitive dairy products and juices because of its high heat exchange efficiency and shorter residence time of the product in the heater.
(15) The evaporation capacity is from 1000L per hour to 65000L per hour, and the evaporation temperature is from 40℃ to 90℃ according to the different products.
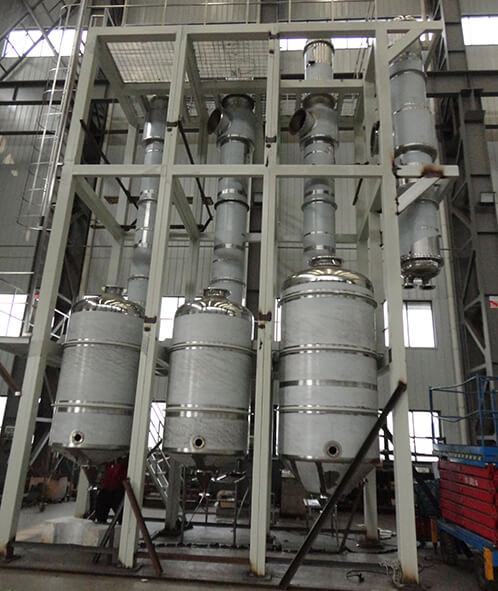
Technical Parameter:
Model | Single effect | Double effect | Triple effect | Forth effect | Fifth effect | ||||
---|---|---|---|---|---|---|---|---|---|
Evaporating temperature | 45-90 ℃ | ||||||||
Steam consumption | Depend on the capacity and evaporating temperature of the material | ||||||||
Steam pressure | 0.5-0.8MPA | ||||||||
Material discharge brix | Depend on the material character | ||||||||
Material Feeding brix | Depend on the material character | ||||||||
Capacity(LPH) | 300-2000LPH | 1200-4000LPH | 500-15000LPH | 5000-50000LPH | 10000-65000LPH |