Project Description
Decanter Centrifuge Separator
Decanter Centrifuge Separator Description
- Separation technology plays important role in the production of juice, helping to preserve the precious natural substance of fruits and vegetables. We offer various decanter separator systems for the efficient production of high-quality fruit and vegetable juice.
- Decanters are used for the extraction of finely solubilized fruit and vegetable mashes, they excel in high yields and can be used flexibly for fruit juice extraction and solid-liquid separating in fruit juice processing.
- The decanter centrifuge has high throughput and high efficiency, optimum hygiene, gentle extraction, rapid juicing, reliable discharge of solids for varying consistency, lower water and energy consumption feature.
- It can be used for a wide range of fruit and vegetable juice extracting and solid-liquid separating like cherries, berries, dates, grapes, tropical fruits, root vegetables, herbs, peas and medical plants.
The Working Principle of the Decanter Centrifuge Separator
Two-phase Decanter Centrifuge Separator
The decanter centrifuge separator is mainly composed of a rotating drum, a spiral, a differential, and a machine base. The rotating drum and the spiral rotate with the same direction at a certain differential high speed. The material is continuously transferred into the spiral inner cylinder by the feed pipe and enters the rotating drum after acceleration. Under the action of the centrifuge force field, heavier solids are deposited on the drum wall to form a sediment layer. The spiral continuously pushes the deposited solid phase to the cone end of the drum and discharges it out of the machine through the slag discharge port. The lighter liquid phase forms an inner liquid ring, which overflows the drum continuously from the large end overflow port of the drum and is discharged out of the machine through the liquid discharge port. To realize the separation of liquid and solid phases with different densities. This machine can continuously feed, separate and unload material under high-speed operation. It has the characteristics of compact structure, continuous operation, stable operation, strong adaptability, large production capacity and convenient maintenance. It is suitable for separating suspensions containing solid phase with a particle size greater than 0.005mm, a weight concentration ratio ≤10% or a volume concentration ratio ≤70%, and a solid-liquid specific gravity difference ≥0.05g/cm3. Widely used in food and beverage, environmental protection, chemical, non-mineral, pharmaceutical and other industries.
Three-phase decanter centrifuge
The three-phase decanter centrifuge is formed by adding the heavy liquid pressure discharge mechanism on the basis of the two-phase horizontal screw machine structure. The material is continuously introduced into the spiral inner cylinder through the feed pipe, and enters the rotating drum after acceleration, using the liquid-solid-solid specific gravity difference. Under the action of the centrifugal force field, heavier solid phase deposits on the drum wall to form a sediment layer. The spiral continuously pushes the deposited solid phase to the cone end of the drum and discharges it out of the machine through the slag discharge port. The two liquid phase materials are divided into light and heavy two phases to form a light liquid phase and a heavy liquid phase respectively. The light liquid phase is discharged by gravity through the large end overflow of the drum, and the heavy liquid phase is discharged by pressure through the impeller mechanism. So as to realize the separation of liquid-liquid-solid three-phase mixture with different densities.
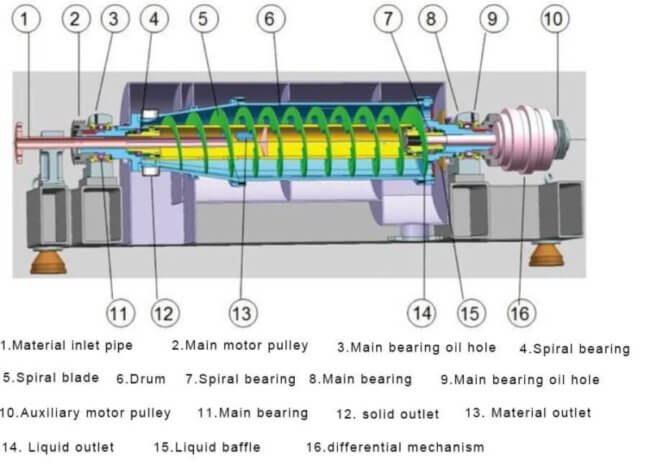
The Structure of the Decanter Centrifuge Separator
Feeding: The material is fed into the distribution chamber of the screw conveyor through the feed pipe, where the material is smoothly accelerated and enters the rotating drum through the outlet of the screw conveyor.
Drum: Separate the materials in the cone and column drum. The drum rotates at a certain speed according to the separation requirements. The mixed liquid rotates under the drive of the drum, forming a concentric liquid layer along with the drum shell, mixing The denser solids in the liquid are deposited on the inner wall of the drum under the action of centrifugal force.
Screw conveyor: The screw conveyor and the drum rotate asynchronously in the same direction, and the separated solid is pushed toward the cone section along the axial direction. The cone section has a certain cone angle. The residence time of the solids in the cone section can be achieved by changing the differential speed. The length of time is an important factor in determining the moisture content of the solid. The solid deposited on the inner wall of the drum is pushed by the screw conveyor to the solid slag outlet of the drum and discharged.
Overflow plate: The liquid flows to the cylindrical end of the drum after clarification, and flows out through the adjustable overflow plate. The overflow plate determines the depth of the liquid layer. The greater the depth of the liquid layer, the higher the liquid phase clarification. The clarified liquid is discharged by gravity. According to the requirements of material separation, a suitable overflow plate can be selected.
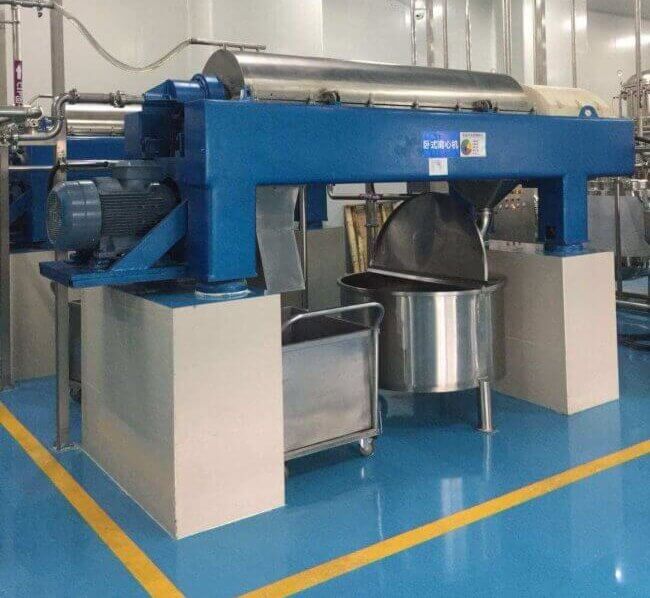
Drive Method of Decanter Centrifuge
The common driving methods of decanter centrifuge are single motor drive, dual-motor drive and hydraulic transmission
- Single motor drive: The drum and screw are driven by the same motor, and it is difficult to control and adjust the differential speed. Now it is rarely used.
- Dual-motor drive: The drum and the spiral are driven by the main motor and the auxiliary motor, and are equipped with dual-frequency electric control boxes, which can easily adjust the speed and differential speed, and are widely used.
- Hydraulic transmission: the high-speed hydraulic motor is used to drive the drum, and the low-speed high-torque hydraulic motor (hydraulic differential) is used to directly drive the screw, and the corresponding hydraulic pump station is equipped. It can realize step-less speed regulation and differential speed less than 1r/min. Compared with mechanical differential, the torque transmitted by hydraulic differential is the largest under the same size. The disadvantage is the high price.
Three Major Applications of Decanter Centrifuge
Decanter centrifuges are commonly used in the food and beverage processing industry for various applications that involve the separation and clarification of liquids or the dewatering of solids.
- Fruit and vegetable juice processing: When the decanters are applied to fruit juice extraction, they can separate off pips, peels hard tissues, peels black dots, and fibers from the juice. Centrifuges and decanters separate and clarify fast and efficiently with optimum yield.
- Plant-based milk processing: When the decanter centrifuge is used for plant-based product processing(soy milk, oat milk, peanut milk, walnut milk), it is mainly used to remove the big particles and solids from the plant-based slurry.
- Fruit oil processing: Decanter centrifuge plays a crucial role in fruit oil production such as citrus oil, avocado oil, coconut oil and olive oil. The decanter is mainly used to separate water, solids, and fat in fruit mash to obtain pure oil products.
- Wine and Beer Clarification: Decanter centrifuges are used in the clarification of wine and beer. They separate the suspended solids, such as yeast, sediment, and impurities, from the liquid, resulting in clear and visually appealing beverages. This process is essential for improving the quality, stability, and taste of the final product.
The main function of the decanter centrifuge is as follows:
- Solid-phase dehydration: the solid particles used to process the material get the dehydration effect.
- Particle size classification: used to remove solid particles with larger particle size in feed liquid.
- Liquid phase clarification: used to remove solid particles in suspension to obtain a clear liquid.
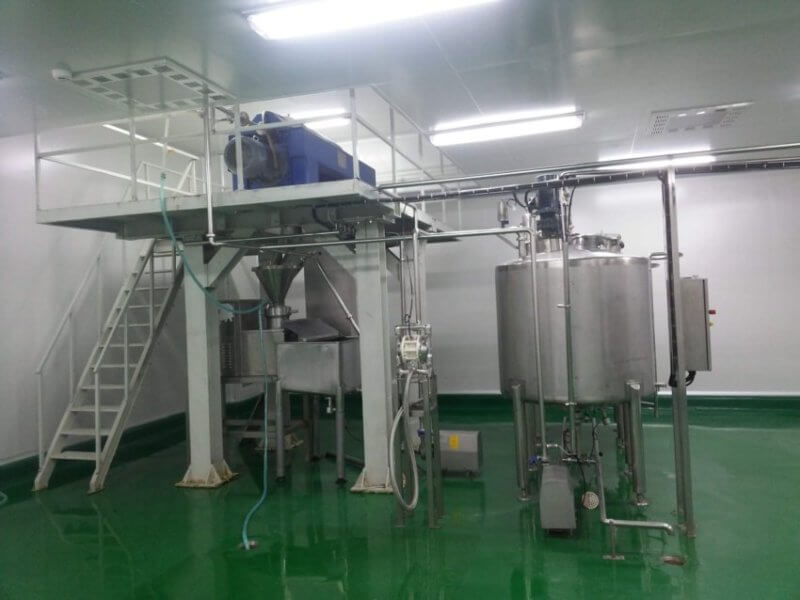
Technical Parameter of Decanter Centrifuge
Model | Drum Diameter(mm) | Capacity(L/H) | Power(KW) | Weight(KG) | Size(mm) |
---|---|---|---|---|---|
LW 250 | 250 | 1000-4000 | 11 | 1200 | 2650* 720* 900 |
LW (F)250 | 250 | 1000-4000 | 11 | 1200 | 2650* 720* 900 |
LW 250(W) | 250 | 1000-5000 | 11 | 1300 | 2750* 720* 900 |
LW 350 | 350 | 5000-15000 | 22 | 2000 | 3585* 980* 1238 |
LW (F)350 | 350 | 5000-15000 | 22 | 2000 | 3585* 980* 1238 |
LW (S)350 | 350 | 2000-10000 | 22 | 2000 | 3676* 980* 1238 |
LW 450 | 450 | 5000-20000 | 30 | 3000 | 4380* 1080* 1360 |
LW (F)450 | 450 | 5000-20000 | 30 | 3000 | 4380* 1080* 1360 |
LW 450(W) | 450 | 5000-28000 | 30 | 3200 | 4380* 1080* 1360 |
LW (S)450 | 450 | 5000-15000 | 37 | 3200 | 4195* 1080* 1360 |
LW 520 | 520 | 10000-20000 | 45 | 5000 | 4840* 1160* 1465 |
LW (F)520 | 520 | 10000-26000 | 45 | 5000 | 4840* 1160* 1465 |
LW 520(W) | 520 | 10000-35000 | 45 | 5000 | 4840* 1160* 1465 |
LW 550W | 550 | 10000-45000 | 55 | 6500 | 5038* 1388* 1578 |
LW 650(W) | 650 | 25000-60000 | 75 | 8000 | 5500* 2280* 1340 |
LW 720(W) | 720 | 35000-85000 | 110 | 13000 | 5600* 3280* 1450 |