Project Description
Pressure Nozzle Spray Dryer
Pressure Nozzle Spray Dryer Application
The pressure nozzle spray dryer is widely used for food and beverage products drying such as fatty milk powder, protein, cocoa milk powder, non-dairy creamer powder, substitute milk powder, egg white (yolk), food and plant juice powder, oats, banana powder, coconut milk powder, ginger powder, chicken juice, coffee extract, starch, instant dissoluble tea, soybean, peanut protein, hydrolysate, sugar, corn syrup, corn starch, glucose, pectin, malt sugar, sorbic acid potassium, and etc. It can also be used for drying Chinese traditional medicines, pesticides, antibiotics, medical drinking agents, and etc.
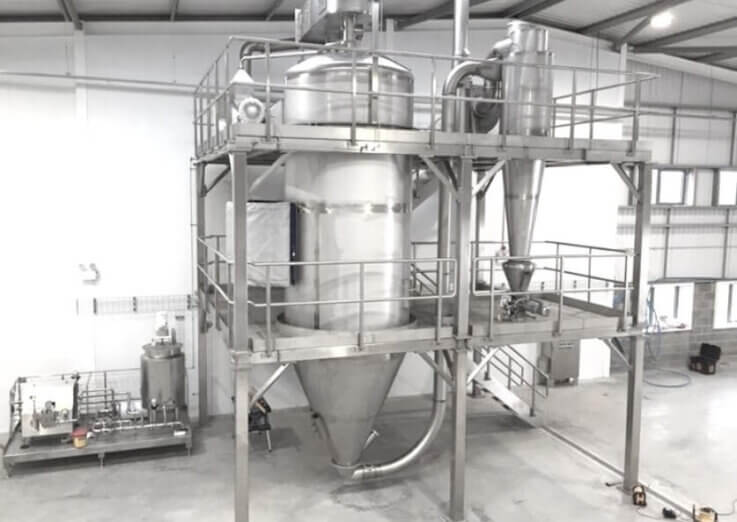
Pressure Nozzle Spray Dryer Working Principle
The pressure nozzle spray dryer uses a high-pressure diaphragm pump to spray the material liquid from a nozzle hole with a diameter of 0.5-1.5mm under a pressure of 7-20Mpa. Due to the high pressure and small nozzle hole, the material liquid is quickly atomized to a diameter of 10 -20μm mist droplets through amply heat exchange (5-30 seconds) after being in contact with the hot air, so that the solid matter in the material is dried into powder granules, most of the powder granules are collected from the outlet of discharge at the bottom of the dryer. The wasted air and fine powder are separated by the cyclone, the wasted air is exhaust from the draft fan, and fine powder is collected at the bottom of the cyclone. There is a second-grade duster equipped at the outlet; therefore, the recovery rate of the finished powder granule can be 96% to 98%.
Pressure Nozzle Spray Dryer CompositionÂ
- Concentrated material tank: store the material for a short time to balance the production capacity of the evaporator and spray dryer. The two tanks can be used and cleaned in turn to avoid bacterial infection. Made of SUS304-2B stainless steel plate, the thickness of the inner wall is 3mm, the thickness of the outer wall is 2mm, the welding bead is polished to 0.6um, the U-shaped insulation structure, the thickness of the polyurethane foam or rock wool insulation layer is 50mm, manhole, anti-mosquito respirator, respirator can be CIP cleaned.
- High-pressure pump, the pressure is 30-40MPa, it is used to form a high pressure to atomize the concentrated material in the tower. The main structural feature is a three-plunger high-pressure pump. The material contact surface is made of stainless steel.
- Hot air distributor, on the top of the drying tower, there is a guide cylinder air chamber, with an anti-rotation baffle in the middle, an air uniform plate and a guide plate at the bottom, which are insulated by 100 mm thick rock wool, and both inside and outside are made of SUS304-2B stainless steel The board is fully welded and the skeleton is made of carbon steel.
- Tower body, the inner body is made of SUS304-2B stainless steel material, the thickness of the top plate inside the tower is 3mm, the thickness of the cylinder and the cone plate is 3mm, the weld seam is polished, and the outside of the top cover is covered by stainless steel 4mm checkered plate and 100mm rock wool The inside and outside are fully welded and insulated, the cylinder is 100mm air-insulated, the vertebral body is 80mm air-insulated, the skeleton is made of carbon steel, the outer skin is made of 1.0mm SUS304-2B stainless steel plate, equipped with 2 imported explosion-proof doors with safety certification, 2 pcs Inspection door 550×650mm inner flat heat preservation square door.
- One set of built-in fluidized bed and air inlet system is located at the lower part of the tower cone, so that the powder falling into the built-in fluidized bed will be in a state of thinning and flowing under the action of the lower wind, so that the powder can be further dried and the powder layer can be adjusted Thickness, into the vibrating fluidized bed. Made of SUS304-2B stainless steel, the cylinder is 80 mm in air insulation, and the outer cylinder is made of 1.0 mm SUS304-2B stainless steel plate. There are 2 inner flat inspection manholes, a sight glass and a powder outlet pipe. There is an independent air intake heating system, and the air intake adopts a sub-high-efficiency filter with a precision H11 filter element.
- Two-stage series cyclone + cloth bag powder capture system, used to recover the fine powder entrained in the hot air discharged from the tower body, made of SUS304-2B stainless steel material, thickness 3mm, internal weld seam ground and polished. The hot air discharged from the drying tower first enters a first-stage cyclone powder catcher, where more powder is collected, and the hot air discharged from the first-stage cyclone powder catcher enters the second-stage bag-type powder catcher to increase the yield of the product and meet the requirements of environmental protection dust emission standards. Equipped with air hammer, inner flat manhole, inner flat hand hole, cleaning nozzle and connecting pipes. The bag powder catcher is equipped with a compressed air pulse blowback system and CIP cleaning system.
- Air filter, the air enters the main intake fan through the filter, so that the general dust and bacteria cannot enter the product, the filter shell and frame are made of SUS304 stainless steel, sub-high efficiency standard size quick-install filter element, precision H11 filter element.
- Inlet fan, centrifugal type, high-strength fan casing and shock-absorbing bracket made of carbon steel, coated with anti-corrosion paint, flexible joints at the air pipe connection, frequency conversion control.
- Exhaust fan, the exhaust air after drying the material is discharged outside, so that the system can generate the required negative pressure. The impeller and shell of the exhaust fan are made of carbon steel, frequency conversion.
- Air heater, 1.8~2.2MPa steam enters the heating tube to heat the air entering the heater and send it into the tower for drying materials. The design pressure of the heater is not lower than 3.5MPa, and the heating tube and frame are made of stainless steel.
- There are 2 sets of cooling systems on the top of the tower, with 2 separate fans for air supply, one way to cool the jacket tube of the spray gun rod and the nozzle to avoid coking of the coke tube and the nozzle, and the other way to protect the top of the tower from coking powder. Centrifugal fans are used to filter the incoming air with sub-high efficiency. The fans are made of carbon steel and the pipes are made of stainless steel.
- 1 set of electrical control cabinet, the high-pressure pump, inlet and exhaust fans are controlled by PLC with frequency converter. Low limit alarm for wind temperature, low limit alarm for material tank, automatic replenishment of water when material is cut off, high limit alarm for exhaust air temperature, super high limit closing steam valve, automatic control of negative pressure in the tower and alarm for negative pressure over limit.
- The air ducts, manholes, hand holes and flanges that make up the drying system are made of SUS304, and the top of the tower and the top of the cyclone separator are equipped with stainless steel safety guardrails.
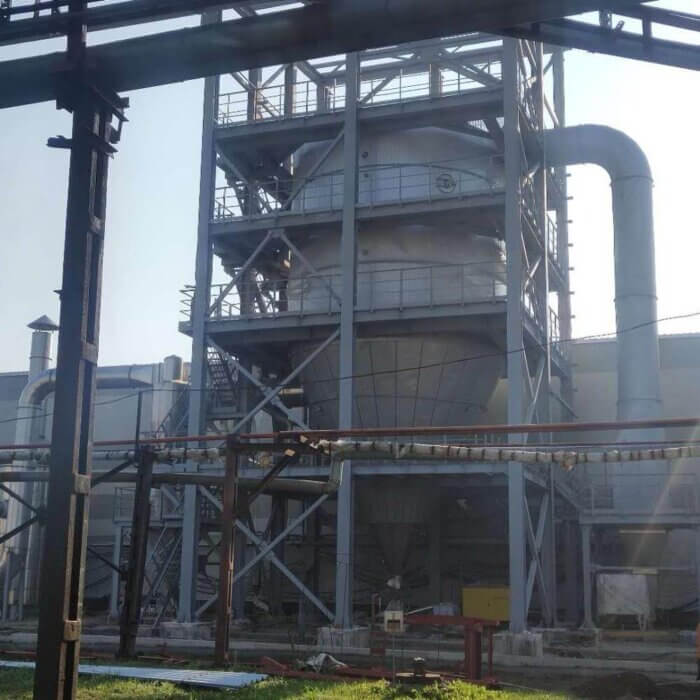
Pressure Nozzle Spray Dryer Feature
- Rapid drying speed. The surface area of the material will be enlarged greatly when the liquid raw material is atomized and 95% – 98% of water can be evaporated instantly in the hot airflow. The drying time only need to take several seconds. This dryer is especially suitable for heating-sensitive materials.
- The finished product is ball granule with a uniform size. Its fluidity and solubility are good. The quality and purity of the product are very high.
- Depend on the characteristics of raw material, the dryer can use hot air to dry or use cool air to granulate.
- Simple and stable operation. The control system is convenient which is easy to realize automatic operation.
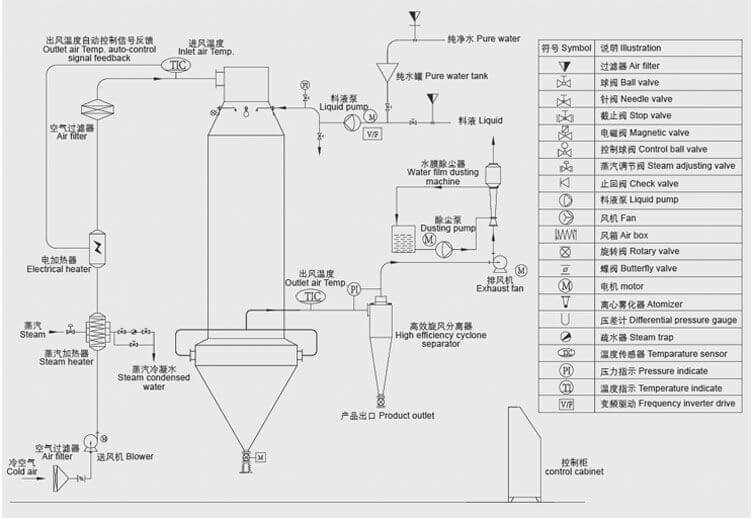
Technical Parameter
Model | XPG-50 | XPG-100 | XPG-150 | XPG-200 | XPG-300 | XPG-500 | XPG-1000 | ||||||
---|---|---|---|---|---|---|---|---|---|---|---|---|---|
Water evaporation capacity | 50KG/H | 100KG/H | 150KG/H | 200KG/H | 300KG/H | 500KG/H | 1000KG/H | ||||||
Size(φ*H) | 1600*8900mm | 2000*11500mm | 2400*13500mm | 2800*14800mm | 3200*15400mm | 3800*18800 | 4600*22500mm | ||||||
Diaphragm pump pressure | 2-10MPA | ||||||||||||
Power | 8.5KW | 11KW | 14KW | 22KW | 24KW | 30KW | 80KW | ||||||
Inlet air temperature | 140-350℃ | ||||||||||||
Product moisture content | <5%, can reach to 0.5% | ||||||||||||
Material recovery rate | >97% |