UHT Pilot Plant Description
The UHT pilot plant is composed of the hot water system, ingredients dissolving system, blending or fermentation system, pilot UHT sterilizer, mini homogenizer, aseptic filler, operating platform, and auxiliary system(air compressor, chiller and RO water system).
The capacity of the UHT pilot plant is from 20L/H, 50L/H, and 100L/H available to choose from.
The whole system is designed with an integrated, compact structure, that can save space and move flexibly. The unit is based on a self-contained, skid-mounted design with the control panel positioned at the rear.
It is controlled by PLC, with a high degree of automation, and simple operation.
The UHT pilot plant is also equipped with a data record control system, which can record various experiment data, download data, online printing and generate the analysis curve. The complete data recording system will greatly help guide industrial production and teaching purposes in college.
The pilot UHT sterilizer is built with a hot water generating system and can be connected with a homogenizer and aseptic filler to make the aseptic products.
The independence of some stand-alone equipment can be used in production lines or independently without the need for additional facilities.
The main structure is made of high-quality 304 stainless steel and 316L stainless steel.
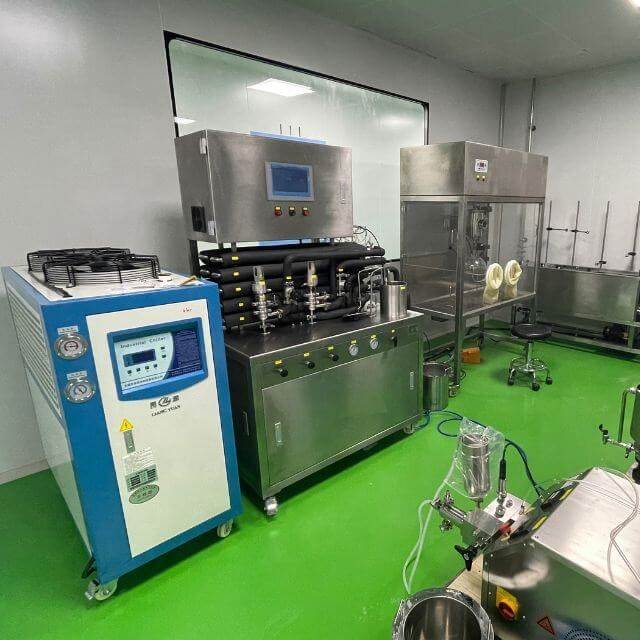
UHT Pilot Plant Application
The whole pilot UHT system can be used for liquid food and beverages, juice, tea drinks, plant-based drinks, flavored milk, dairy cream, fruit pulp/puree, milk, yogurt, fruit jam, fruit pulp products formulation testing, beverage processing technology verification and flavor testing: Ingredients formulation, UHT sterilizing, homogenizing process testing, aseptic filling, hot filling, cold filling products shelf life testing, testing for sequence of adding small ingredients, mixing temperature, stirring and emulsification time, flavor test after ingredients, homogenization temperature and pressure, sterilization temperature and time, filling temperature, etc.
-
Product Development & R&D
-
Used by food scientists to experiment with new formulations and ingredients.
-
Helps in testing how different heat treatments affect taste, texture, and shelf life.
-
-
Quality Control & Process Optimization
-
Ensures product stability and consistency.
-
Helps refine UHT processing parameters before full-scale production.
-
-
Shelf Life Testing
-
Determines how UHT treatment affects microbial stability and packaging interactions.
-
Supports regulatory compliance and safety assessments.
-
-
Small-Batch Production
-
Ideal for limited-edition products, niche markets, or clinical trials.
-
Reduces waste and cost compared to full-scale production.
-
-
Academic & Industrial Research
-
Used in universities and research institutes for studying food preservation techniques.
-
Helps in training students and professionals on UHT technology.
-
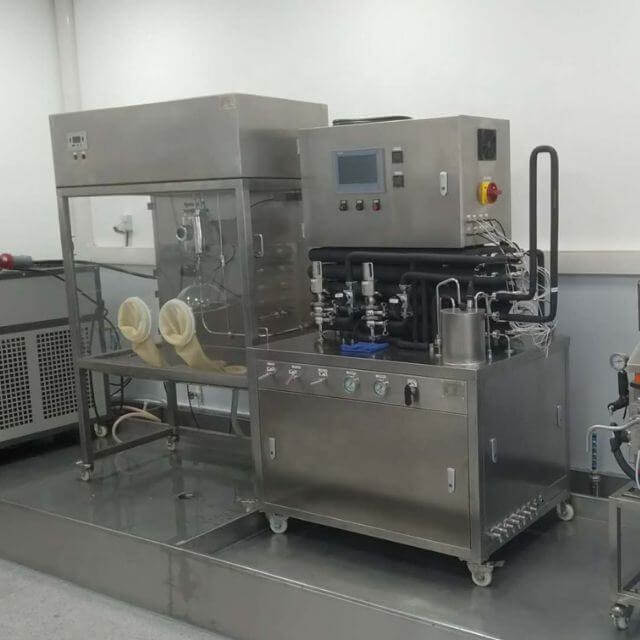
UHT Pilot Plant Machine Introduction
Ingredients formation and blending system
This whole system is composed of hot water tank, High shear emulsification tank and blending tank, products pumps, water pumps, pipelines and connecting valves.
The hot water is heated by electricity, and the hot water tank is polished inside and outside, with built-in heating tubes, float type liquid level gauge, upper flat cover and bottom elliptical head, SUS304 material, it has the following feature:
- Inner surface polished, Ra≤0.4μm, outer surface polished, Ra≤0.8μm;
- Structural form: vertical form, upper flat cover, lower standard elliptical head;
- Floor-standing frame structure, space-saving, easy to operate;
- Heating method: electric heating tube heating;
- Used for emulsification tank heating and blending tank insulation;
- Liquid level meter: float;
- Configuration: sight glass light, digital display thermometer.
The high shear dissolving tank is a jacketed tank heated by hot water, with top emulsifying head stirring, top opening cover, liquid level sensor and temperature sensor, and sight glass.
- Jacket heating, inner surface polished, Ra≤0.4μm, outer surface polished, Ra≤0.8μm;
- Structural form: vertical form, upper flat cover, lower standard elliptical head;
- Floor-standing frame structure, space-saving and easy to operate;
- The insulation material is chlorine-free rock wool;
- Stirring device: top emulsifying head;
- Stirring speed: 2900rpm;
- Liquid level meter: electrode;
- Configuration: sight glass lamp, digital display thermometer.
The blending tank is also a jacketed tank, eccentric vertical mixing 36rpm, CIP cleaning port, sample valve, electrode type level sensor, and temperature display.
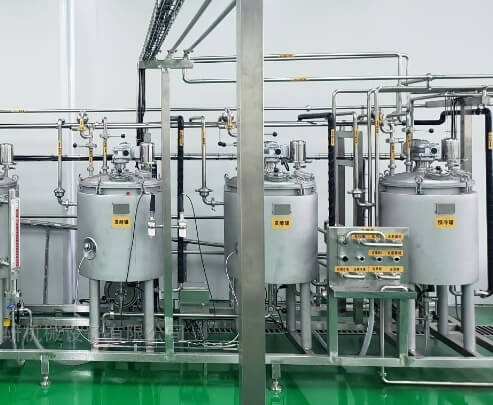
Pilot UHT sterilizer
FeatureÂ
The pilot UHT sterilizer is the core machine in the UHT pilot plant. It is widely used in liquid foods such as juice drinks, fruit puree, tea drinks, fresh milk and yogurt, and juice with fibers and particles.
It includes a tubular heat exchanger, machine frame, balance tank, material pump, tri-clamp type heat exchange system, built-in hot water system, steam control system, piping system, and electronic control system. When running, there is no need steam boiler and RO water treatment system.
Various sterilizing process: 25℃material inlet–65℃homogenizing—85-95℃/115℃/121℃/137℃ holding for 5S/10S/15S/60S/120S/300S sterilizing–5℃/25℃/43℃/85℃ material outlet.
Material feeding and discharging is automatic, sterilizing temperature and time automatic control and adjustable.
The whole system is made of SUS304/316L with an online CIP system, easy to clean and ensures hygienic condition.
Capacity is from 20L to 100L to choose from.
The homogenizer and aseptic filling chamber can be configured according to actual research and development needs. The aseptic filling chamber can adapt to a variety of packaging containers.
Good safety protection, the heat exchange tube is equipped with an insulation layer and a rack-mounted protective net to prevent operators from being burned.
The pilot UHT sterilizer can do the heat treatment of material viscosity less than 18000cP, and the material particle size less than 2mm.
The sterilization temperature is strictly controlled. When the sterilization temperature is lower than the set limit, the timer will terminate and reset to strictly ensure the sterilization effect of the equipment.
The whole system can be integrated with DSI(Direct Steam Injection/Infusion) heating, which is used for sterilizing high-fat and high-protein products like cream, coconut milk, soy milk products.
Operation process:
- Material feeding: Feeding in the previous process / manual feeding;
- Material preheating: Shell side hot water pipe side material heat transfer to heat material to 60-70℃; Through the temperature sensor and hot water flow regulating valve linkage realization;
- Homogenization: Homogenizer homogenizes materials into more uniform materials at 60-70℃;
- Sterilization: Hot water continues to heat the material to the sterilization temperature, realized by the linkage of the temperature sensor and hot water flow regulating valve;
- Material holding: Can achieve 5 / 10 / 15 / 300SÂ holding;
- Tap water cooling: First stage using tap water exchanges heat with material, which reduces the material’s temperature to 43℃;
- Ice water cooling: The second stage using ice water exchanges heat with material, which reduces the material temperature to 25-30℃;
- Filling: After the material is cooled to the filling temperature, then can be discharged to the filling machine for filling.
Configuration:
- Intelligent PID adjustment satisfies smooth transition during process switching and reduces temperature fluctuations
- Superheated water is heated, and the back pressure valve ensures the operating pressure.
- The tube material of the material contact part is: SUS316, and the other parts are SUS304
- Hot water heating, ice water cooling, high-temperature alarm, low-temperature reflux,
- JUMO or NEGAL temperature sensor,
- GEA or APV pneumatic butterfly valve and directional valve,
- With CIP cleaning system and SIP disinfection system,
- Operation control is controlled by Siemens or an equivalent brand PLC control system.
- Siemens or equivalent brand color touchscreen operation
- A set of product temperature and pressure data recording software packages
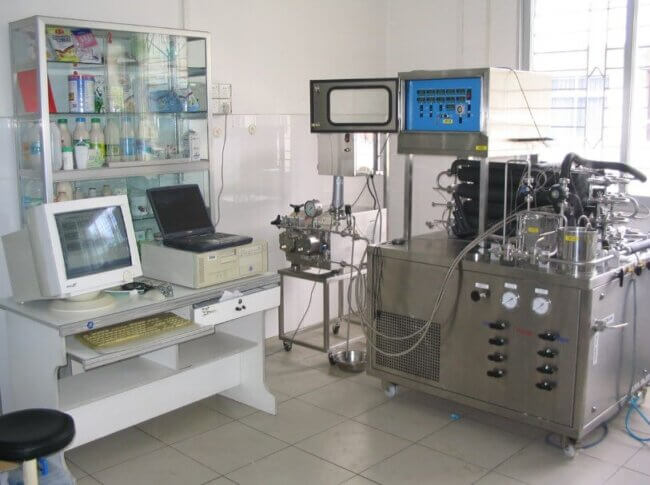
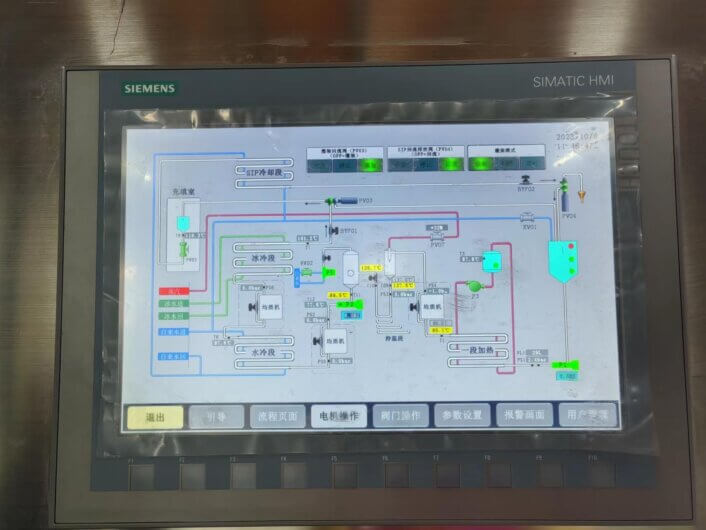
Mini High-pressure homogenizer
The inline mini high-pressure homogenizer disperses and emulsifies materials to get smoother tissues, it can be installed upstream or downstream of UHT system according to customers’ requirements.
- Inlet and outlet pressure display;
- Contains two modes: feed hopper and pipe connection;
- Material pipeline feeding mode, CIP cleaning pipeline;
- Double plunger design RE type ceramic homogenizing valve material;
- Two-stage homogenizing valve, adjustable pressure range: 0-600bar;
- Use the handwheel to manually adjust the homogenizing pressure, and the pressure is continuously adjustable;
- Continuous injection, standard processing volume: 20L/H, 50L/H and 100L/H, minimum processing volume is 500 ml;
- The compression head is made of high-quality, high-strength and corrosion-resistant SAF2507 special duplex stainless steel;
- High-precision digital display hygienic diaphragm pressure gauge;
- Special solid ceramic plunger, equipped with special seal and sealing gasket, no lubrication required;
- A set of standard spare parts package (contains a set of standard spare parts and a set of special tools marked equipped)
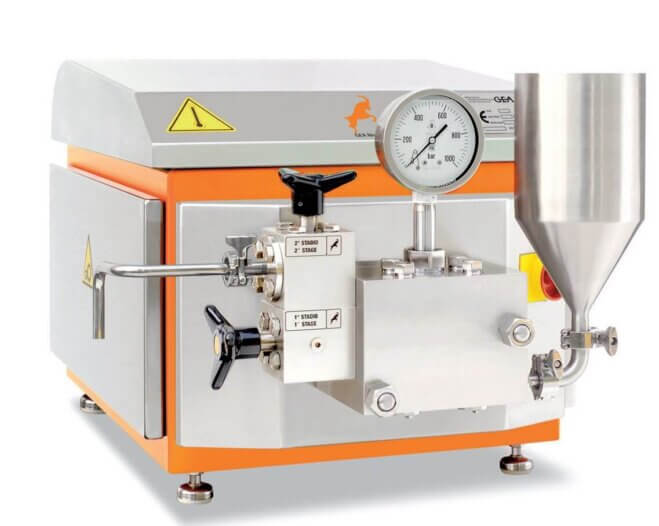
Aseptic filler
This equipment is a vertical flow-shaped sterile operating table and an air purification system composed of a fan, primary effect, high-efficiency filter and ion generator.
When working, the outside air is pre-filtered by the primary filter, and then sent to the high-efficiency filter by the fan to reach high ultra-cleanliness (level 100) in the operating area. Finally, it is sterilized by the ultraviolet lamp and ion generator to form an ultra-clean environment locally.
The working unit is independent; the foot switch controls the filling switch, and the operation is completely matched with the UHT system.
The built-in product buffer tank is equipped with a single-head pneumatic filling valve; the built-in automatic capping device is optional for batch production of samples.
Performance indicators:
- Laminar flow method: vertical laminar flow
- Average wind speed: ≥0.4M/S, four speeds adjustable.
- Cleanliness: Class 100, in line with federal 209D100 standard
- High efficiency filter specifications: 1220X610X50
- Lamp power: 20 W
- Applicable filling products: milk, milk drinks, juice, ketchup, condiments, additives, tea drinks, beer, cream, butter, ice cream and other products
- UV lamp power: 18 W
- Fan power: 140 W, small vibration and low noise.
- Air volume: 900-1400M3/H
- Noise: less than 60db (A)
- Capacity: 50-300 bottles/h
- Overall size: 1280 (L) × 670 (W) × 1850 (H) mm
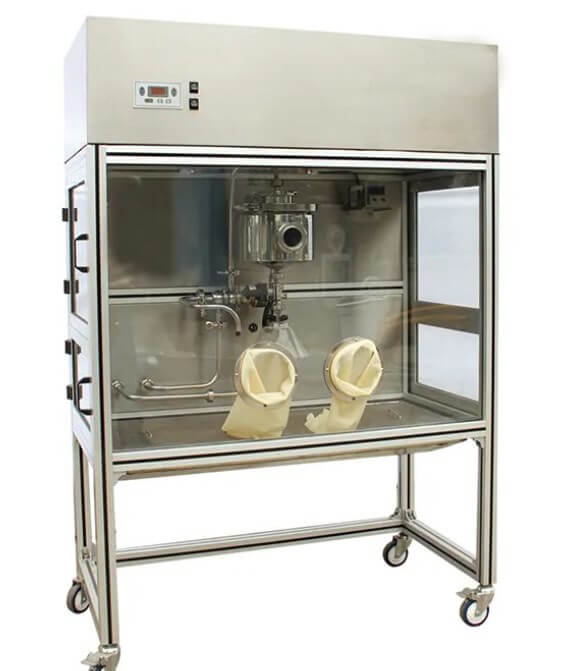